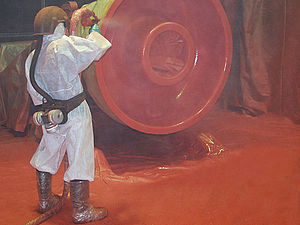
Monitor Wear Linings to Maintain Process Efficiency, Increase Equipment Longevity
, sramaker - Retour à l'aperçu
Mass finishing machinery is a major investment for most companies. Proper maintenance and preventative repairs over the life of these useful and necessary machines will greatly improve the return on such investments, drive productivity, and extend the working life of the equipment itself.
Rosler stresses the need to regularly inspect the linings of vibratory tubs and troughs to identify repairable issues before permanent damage occurs.
Media-Induced Wear
To effectively finish work pieces, media must be matched to the specific finishing task and initial state of a work piece. For example, media used for deburring/edge radiusing and surface grinding can be very abrasive. If not properly protected by a suitable wear lining, the steel construction of a work bowl would be completely worn through in a few hours by contact with the media and work pieces.
Polyurethane and, to a certain degree, rubber are excellent lining materials providing wear protection for thousands of operating hours. Even these materials wear though and must be periodically replaced with a new lining. (More information about specifying liner materials is available in a previous blog post.)
Maintaining Process Stability
Checking your work bowl lining for wear and replacing it in a timely manner is essential for the stability of your mass finishing process as a whole. In addition to worn work bowls, failure to ensure a proper protective lining can create other problems including:
- Work pieces getting stuck in the machine and, therefore, jeopardizing the integrity of different work piece batches.
- Media, water, and process chemicals can leak from the machine if the metal processing bowl is worn through and holes or cracks appear.
- Severe machine malfunction can occur when media or parts can get trapped in worn spots during the separation phase when the finished work pieces are separated from the media.
- Damage to the work bowl that is beyond repair, causing an unnecessary downtime and requiring costly replacement parts. A weakened bowl can crack and make the entire machine unusable
Check your bowl lining at least monthly for wear or rips. Especially the areas around drains, the parts loading chute, and around the unload areas will see the highest wear. The ânail testâ makes checking the liner thickness easy. Push a nail trough the liner until you hit the base metal and record the thickness of the liner. Keep track of the liner thickness over time to predict when you will need to replace your liner.
Just as optimal media mix must be regularly monitored, so must the condition of a work bowl. If not, the entire process and downstream operations may suffer.
Reline Expertise
This work bowl is being relined with sprayedâon polyurethane at a Rosler reline shop.
Rosler maintains a shop offering reline services for work bowls of all types and makes. With the unique Rosler ThermoStrip procedure, we can patch and repair worn work bowls to restore process efficiency and extend the life of your equipment whether Rosler designed it or not.
The Rosler Way
Our worldwide network of service providers is positioned to provide expert service and guidance. Contact us to discuss how we improve your process and increase the lifespan of your equipment.