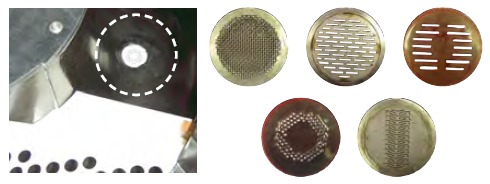
Mass Finishing Process Water, Part 2 â Maintain Adequate Drainage to Protect Your System
, sramaker - Retour à l'aperçu
Numerous functions and calibrations factor into developing a precise and stable mass finishing process. From media and compounds to work piece characteristics and processing times, successful finishing requires each process aspect to be carefully monitored and evaluated. When it comes to process water flow rates, poor drainage from the machine can cause quality control issues as well as equipment damage and costly downtime.
While simple in their function, drains play an integral role in regulating the flow of process water out of the machine. With the exception of intentional âfloodingâ of the process bowl for sharp work pieces, the same amount of compound and water entering the machine must be flushed out again. Otherwise, contaminants in the form of dirt, media, metal fines, and, frequently, oil will accumulate in the process water. Since this buildup can cause the finishing process to deteriorate and even collapse, mass finishing machines must have sufficient drainage!
With more than 80 years of experience, Rosler can expertly design mass finishing technology and troubleshoot issues to protect your system for the life of the machine.
Machine Features
Most mass finishing machines, including rotary and tub vibrators and dragâ, plungeâ, and surfâfinishers have special drainage screens built into their work bowls. High-energy centrifugal disc finishing machines differ since the âdirtyâ process water is evacuated through the gap between spinner and work bowl.
Drain types used in rotary vibrators.
Made from plastic such as polyurethane or stainless steel material, these drains must allow process water and media debris to be flushed from the system while retaining usable media mix and the work pieces.
Machines utilizing small media, including steel media for ball burnishing or pressure deburring, always require more drains since small media has a much higher water retention rate than large media.
Regardless of the media size, drains can be easily plugged with media debris, flashes from die castings, small metal pieces, etc., and it is essential to make sure that the drains are regularly inspected and cleaned.
Drain for undersized media seperation in the work bowl.
Manual Evaluation
Taking action to prevent process failure, machine damage, and costly repairs and downtime will improve process results and machine longevity.
To ensure proper process water drainage:
- Make sure that the work bowl of your mass finishing machine contains enough drains. If additional drains are needed, they can be easily installed while the work bowl is being relined. Alternatively, a suction pump can be installed for faster evacuation of the process water, if needed.
- Regularly inspect the machine drains and make sure that they are in good condition, functioning properly, and removing debris appropriately.
- Install drains with bigger or differently shaped holes if plugging occurs.
The Rosler Way
Working with an experienced supplier is the best way to develop and maintain a mass finishing operation. From selecting the right type of machine for your needs to suggesting everyday actions to ensure adequate drainage, Rosler develops lasting solutions. Contact us to learn how we can put our surface finishing expertise to work for you!
The complete Mass Finishing Process Water Series includes:
- Part 1 â Understand When to Balance Flow or Flood the Process Bowl.
- Part 2 â Maintain Adequate Drainage to Protect Your System.