
Aerospace, Part 3 – Drag Finishing for Airbus Helicopters
, roslerusa - Torna alla panoramica
The aerospace industry demands high repeatability and adherence to strict production tolerances. As we discovered in Aerospace, Part 2, Rosler Metal Finishing’s drag finishing systems produce exact results every time.
Airbus Helicopters
After using Rosler drag finishing systems for a number of years, Airbus Helicopters knew just who to turn to for help with a new helicopter model.
We took on the challenging task of finishing larger gear components for the new design as well as incorporating expanded capacity for their existing helicopter models, developing an innovative drag finishing system with automatic work piece clamping and a clever work piece handling system.
Based on numerous processing trials in our test center, Rosler developed an entirely new drag finishing concept that meets all customer requirements. Flexible yet robust, the new drag finisher is capable of finishing approximately 35 different work pieces made from special, high-performance steel alloys with diameters from 40-800 mm and individual weights of up to 75 kg.
Technical Specifications
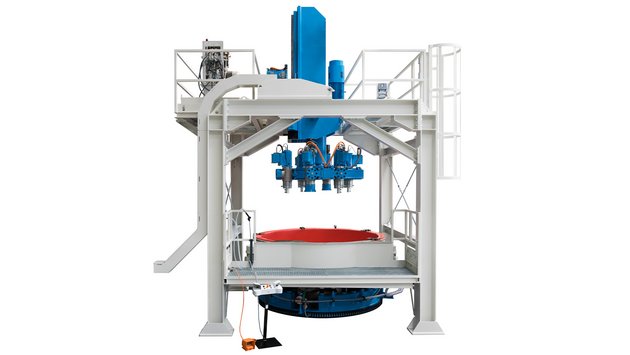
With work bowl dimensions of 1,700 (H) x 2,600 (Ø) mm, this new machine is one of the largest ever built.
To allow the operator easy, ergonomic access to the work stations, the machine was placed in a foundation pit. Three 3.6 kW vibratory motors mounted to the sidewall of the work bowl ensure that the processing media in the work bowl weighing about 6.7 metric tons is thoroughly mixed in between process cycles.
A crane placed behind the machine allows easy and quick filling of media into the work bowl. Worn media that has become too small is discharged through screens in the work bowl bottom. A level indicator shows the operator when to add new media, which is done manually. A Z1000 centrifuge with fully automatic sludge discharge cleans the process water, with a timer controlling the automatic compound replenishment.
The rotating carousel (spinner) is equipped with six workstations with independent rotary drive units. Additionally, the workstations can be shifted to form a smaller or larger circle with adjustable angles. The system allows the simultaneous processing of two large and four small gear components.
Since some of the work pieces are quite heavy, they are loaded/unloaded with a part manipulator. The operator guides the handling system holding one single work piece in a precisely defined position to the workstation. After the work piece has been mounted to the station, it is automatically clamped. Smaller gears are mounted manually.
Based on the cycle times in the existing drag finishing system, the process parameters like circular orbit, rotary speed, and covered distance were translated to the larger, new machine in a manner so that no changes had to be made to the existing finishing process.
For unloading the finished work pieces, the carousel moves into a position that allows the operator to spray-rinse them with water and then remove them from the workstation
Monitoring for Process Safety

In order to meet the high safety standards required in the aerospace industry, all equipment functions are continuously monitored and controlled. This includes the movement of the work piece handling system as well as the correct positioning of the work pieces in the workstation clamping system. Any deviations will cause the automatic stop of the machine.
To make certain that the process water is safely evacuated from the work bowl, the draining screens in the work bowl bottom are not only flushed with water but also regularly cleaned with compressed air. Maintenance is made easy with a central lubrication system that automatically supplies the guides and workstations with grease according to preset time intervals.