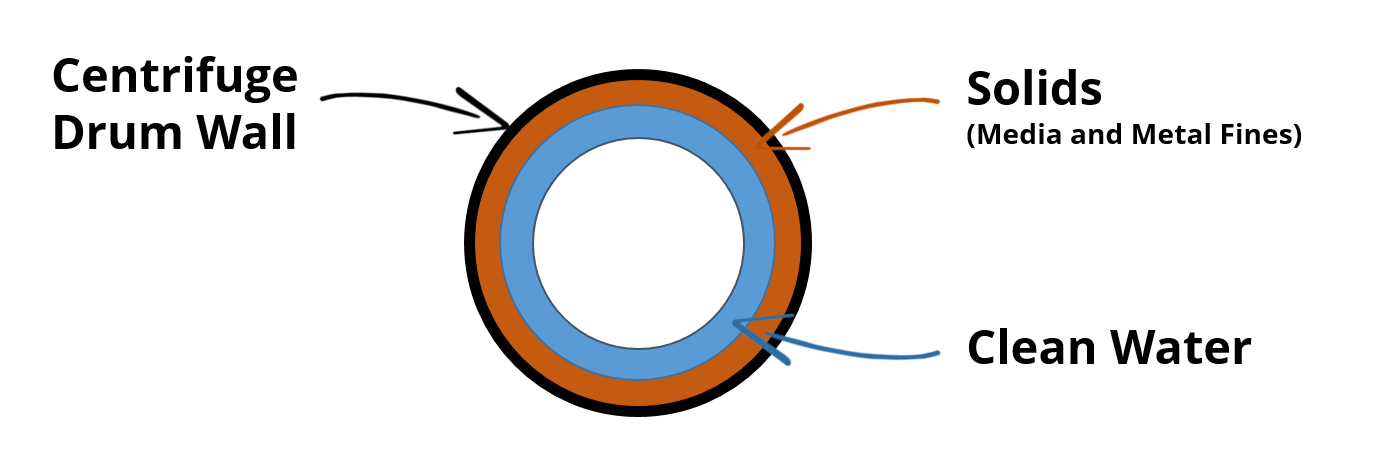
Combining the direction of rotation and centrifugal force, Rosler’s centrifuge technology takes advantage of the weight difference between the liquid phase and the solids in the process water to separate “dirty” solid particles from clean, reusable process water.
The effectiveness of this technology lies in the centrifugal force that is created. For example, a modern fighter jet develops a G-force of about 10-15 while a high-speed centrifuge drum generates a force of more than 2,000 G.
The physics of centrifuge technology combined with mass finishing equipment creates efficient and ecologically sound manufacturing processes, albeit with some key limitations.
Collection by Force
The solids, primarily consisting of media and, to a lesser degree, of metal fines from the work pieces, found within “dirty” process water are heavier than the water itself. As the drum spins, heavier solids are deposited on the drum wall in the form of sludge, whereas the lighter-weight liquid remains on the inside of the drum. With the addition of special cleaning additives known as flocculants, even oil carried into the mass finishing process can be removed from the process water.
As shown in the diagram below, dirty process water is pumped down into the centrifuge drum (1) which is then accelerated by the applied centrifugal force. While the cleaned water is picked up by a so-called collection tube (2) for reuse, the sludge (3) is collected and periodically removed from the drum by mechanical or manual means.
Limits of Cleaning
The presence of solids in the process water is a must. Centrifuge technology works best when the process water contains a certain amount of solids and there is a notable weight differential between the liquid phase and the solids. Through the addition of special water cleaners, centrifuges can also remove oil from mass finishing process water, provided, of course, that the oil content is not too high.
There are a few exceptions in which certain applications produce no or only very few solids in the process water, making centrifugal cleaning difficult or impossible. This is the case with:
- Ball burnishing and pressure deburring when steel media is used instead of ceramic.
- Part-on-part finishing when no media is used at all.
- High-end polishing operations where residual solid particles in the recycled process water might negatively affect the polishing quality.
While process water from these applications is not suitable for centrifugal cleaning and recycling, it must be cleaned with other cleaning methods prior to discharge.
Disposal of the Depleted Process Water
If properly maintained, process water can last for a long time, usually between 3 to 12 months. Once it becomes too contaminated for cleaning, it must be replaced with a new batch of fresh water and compound.
Reasons for depletion include:
- An abundance of solid fines which are too small to be picked up by the centrifuge.
- Too much oil carried into the finishing process.
- A bacteria buildup due to poor maintenance.
- The build-up of salts in the water that affect the finishing process.
In such cases, the depleted process water must be cleaned in a “floc & drop”, membrane, or evaporation system prior to disposal. Depending on the type and level of contamination in the “dirty” water, straight sewer discharge could be illegal, costly, and/or unsafe.
The Rosler Way
The experts on the Rosler team can help identify the best centrifuge technology for your unique process challenges and develop solutions accordingly. Contact Rosler today to learn how we can improve and enhance your mass finishing process.
Previous posts in the Centrifuge Technology series include:
- Part 1 – “Water Cleaning Systems Replace Outdated Methods.”
- Part 2 – “Operational and Economic Benefits of Recycling Process Water.”
- Part 3 – “Mechanics and Limitations of Water Recycling.”
- Part 4 – “Pre-Conditions and Consumables Enhance Process Efficiency.”
Upcoming posts in the Centrifuge Technology series will include:
- Part 5 – “Potential Issues and Remedies for Water Recycling.”
Sign up for enews alerts to be notified of new posts!