
用途广泛且满足各种需求
我们的抛丸设备在表面处理领域功能全面,其涵盖去毛刺、除鳞、去砂、除锈、打毛、消光、圆边、固定以及喷丸硬化等功能。这是因为表面的功能和外观不仅是技术产品的重要质量标准,它们也其在市场上的成功做出了重大贡献。。因此,表面处理在大多数情况下是不可避免的,必须作为一个额外的增值步骤纳入现有的生产过程中。
很少有技术工艺能像喷砂技术那样用途广泛,特别是对于金属表面。Rösler 设备也可以处理矿石材料,如水泥、沙石,以及玻璃、纺织品、木头和塑料。
我们为您提供智能、灵活、个性化的定制服务
Rösler 拥有大量的产品设备供您选择,不论是精密压缩空气的抛丸设备还是高效涡轮抛丸设备。涡轮抛丸设备的特点是耗能少、作用范围广、表面均匀(即所谓的“热点”)。喷射式和压力式抛丸设备的强项在于既可以自动化运转,也可以手工操作,可以用于小面积、点状作业。此外,还可以使用高磨蚀性的丸料,如刚玉、碳化硅、玻璃珠甚至细小的塑料颗粒。而在涡轮喷砂系统上,只有在特殊情况下才能使用这些丸料。




不仅如此
您选择了我们的设备,就代表着我们的整个产品世界将不断为您提供全方位服务。我们为您提供所有零部件、周边解决方案以及服务,并且根据您的要求进行优化和个性化定制。其中包括:
- 我们遍布全球的行业专家与世界各地的分支机构合作,为客户提供最佳咨询服务
- 使用最先进的模拟解决方案,来模拟并最终优化设计高要求的喷丸工艺
- 数字化工艺监测,实现更稳定和经济的过程
- 享受专业咨询服务,并在我们的全球客户体验中心进行测试
- 最先进的生产车间,垂直化生产范围独一无二
- 抛丸设备的售后服务,包括个性化定制维护合同和改造咨询服务
- 本公司服务和应用工程师在全球现场提供支持
- 我们的 Rösler 学院对您的专业人员进行培训和进修
我们为您定制个性化流程——专业化定制

凭借我们多年积累的工艺技术专长,快速识别复杂系统组合的专业能力,以及在我们全球客户体验中心完成的无数次测试和模拟,我们有能力可靠地找到满足您各种要求的最佳解决方案。我们为客户提供最高水平的质量和经济效益,使他们拥有决定性的竞争优势。我们出货的90%的喷砂设备是为满足客户的个性化需求而设计的。我们几乎涉及到每一个行业。对于航空航天和汽车行业,我们法国的子公司也是该行业中的佼佼者。您知道吗,我们也在开发喷丸强化领域的特殊解决方案?
由于表面处理的经济效益和成本效益取决于设备技术的设计以及工艺,我们使用最现代的多物理场模拟软件来优化和锁定喷砂工艺和设备技术的设计。其结果就是为您带来显著的附加值:加工效率更高、速度更快、磨损更少、成本更低,并在喷砂过程中优化除尘。
创新、耐用、高效——为您提供最强动力
我们抛丸设备的特点在于使用寿命长、维护工作量少和具有创新功能。
这不仅仅是表面工夫,而是给您带来真正的附加值。我们的抛丸室厚度(10毫米,而不是市场上常见的8毫米),在吊钩式抛丸设备内的两侧可使用单独更换的锰钢板,以及流体优化空气分级器可使设备和磨料高效地运转。我们还非常重视降低机器连续操作的任务复杂性,从而优化人机工程学和用户友好性,用最现代化的控制结构简化操作。
然而,每台抛丸设备的核心是其涡轮机(抛丸器)。最近几年里,我们投入了大量精力来深入开发这一决定性设备组件,我们的 Rösler 专利涡轮技术能够为您带来决定性竞争优势。我们的伽马涡轮机能在相同的能量输入的情况下将功率最多提高 20%。此外,两侧双用叶片还可以减少高达 30% 的运营成本。
数字化和过程监控在抛丸技术领域也发挥着越来越重要的作用。我们的 Rösler Smart Solutions 能够为客户过程监控的各个领域提供数字化解决方案。从零件质量到运行参数分析,再到预测性检修。最终,您能对偏差和故障更快作出反应,主动监测,减少您的问题处理成本,在商业中享有更多优势。
涡轮机抛丸设备
压缩空气抛丸设备
湿式抛丸设备
塑料抛丸设备
抛丸 喷丸 的关键点是什么? 请浏览常见的问题
抛丸处理是表面处理或表面精加工的必要技术。因此它提供了多种用于表面机械精加工的 方法。有干式抛丸工艺和湿式系统,使用抛丸介质和水混合或纯水。干式抛丸通常用于表 面织构化、去毛刺、油漆和其他涂层剥离、除锈、清砂、除氧化层以及最后但并非最不重 要的抛丸强化。湿法喷砂大体上是一个特别温和的表面处理过程。典型应用包括精密部件 的温和表面清洁、工具等物品的轻度边缘倒圆处理,以及装饰性表面效果的打造。在抛丸 处理过 程中,丸料以高达 170 m/s 的速度被抛到工件表面。在干式抛丸系统中加速抛丸介 质所需的动能由抛头(抛丸轮)和压缩空气产生,而在湿式喷砂系统中则使用高压泵。喷 丸结果通常取决于机器类型、工艺参数,最重要的是,取决于用于特定喷丸作业的丸料的 类型和尺寸。
- 在抛头喷丸处理技术中,所谓的抛丸轮(也称抛头)的高速旋转被用 于加速并将丸料抛到 工件表面上。抛头抛丸机最常见的应用是除锈、去毛刺、去氧化层、去砂和表面粗糙化 (使表面更粗糙)。
- 压缩空气喷砂技术特别适合针对较小表面积进行精准喷砂处理。该技术还可使用磨蚀性极 强的矿物喷砂介质,同时也是抛丸强化工艺的首选技术方案。
- 在湿式喷砂系统中,喷砂介质和水的混合物(即所谓的“浆料”)被泵送至湿式喷枪,并最终在压缩空气的作用下加速喷出。
- 在高压水射流喷砂系统中,使用纯水混合对零件进行喷砂处理,压力非常高。水射流产生的压力高达4000巴(58000磅/平方英寸),仅使用纯水就能去除最坚硬的涂层。
- 湿式喷砂和高压水射流喷砂在航空航天工业中经常被使用。
- 抛丸强化 作为一种特殊的喷砂处理工艺,主要应用于承受动态工作载荷的汽车和航空航 天零部件。通过弹丸 锤击 工件表面,可在表层形成残余压应力层。这种处理能显著提升 零部件抗弯曲和抗拉伸应力能力,并大幅延长其使用寿命。
- 塑料去飞边作为另一种特殊的喷砂处理工艺,专用于热固性塑料及部分热塑性材料等塑料 部件的飞边去除与倒角加工。一般而言,塑料去飞边系统所需的能耗显著较低,且采用专 门配制的较软喷丸介质。
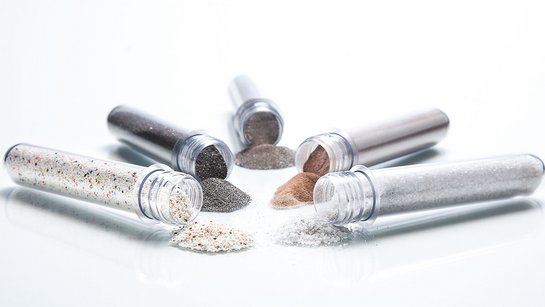
为特定抛丸作业选择最合适的喷砂介质是工艺开 发过程中最重要的决策之一。用户可从多 种喷砂介质中进行选择,其中部分介质可完成相同的抛丸处理任务。关键选择标准包括预 期喷砂效果、设备预计磨损率以及喷砂介质的成本效益。
可以使用最常见的喷砂介质,可分为金属、天然或合成矿物材料以及天然或合成有机材料。最常见的介质一览如下:
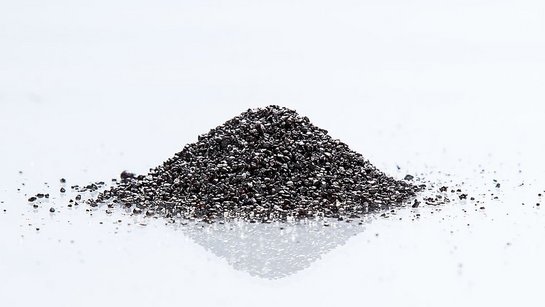
钢铁制成的金属介质:
- 钢丸(圆形)、钢砂和冷硬铁砂是进行强力表面清理、除锈、除氧化层、除砂、去毛刺、 表面纹理处理、制造哑光效果以及抛丸强化(仅限球形介质)的理想选择。这些材料既可 用于抛头抛丸设备,也适用于压缩空气吸入(喷射)式或压力喷砂系统。
- 切割钢丝喷砂介质具有多种形状(圆柱形、圆边、近圆形或完全圆形),适用于常规清 洁、除锈、除氧化层、除砂、去毛刺 轻微倒圆角处理,并常用于抛丸强化。该切割钢丝介 质既适用于抛头系统,也兼容压缩空气吸入(喷射)和压力喷砂系统。
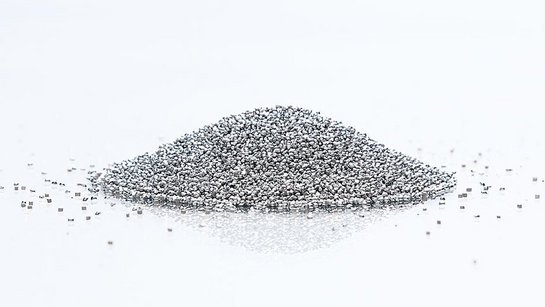
不锈钢喷砂介质:
- 铸造不锈钢丸(完全或部分圆形)与砂粒适用于表面清洁、 除氧化层、除砂、去毛刺 轻微 倒圆角、表面纹理处理、制造哑光效果以及喷丸处理(仅限球形介质)。这些材料可在抛 丸机、压缩空气吸入(喷射)以及压力喷砂系统中使用。
- 切割钢丝不锈钢介质(圆柱形、圆边、接近圆形或完全圆形)用于除鳞处理,也常用于抛 丸强化。这类介质可在抛丸机以及压缩空气吸入(喷射)和压力喷砂系统中使用。
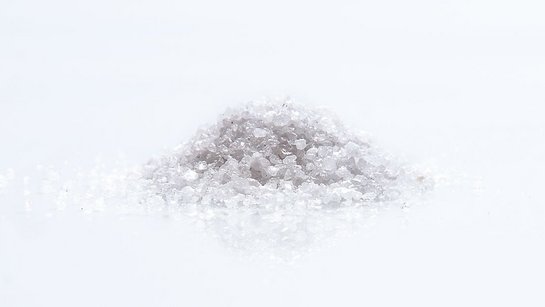
矿物喷砂介质:
- G玻璃珠、玻璃砂、陶瓷珠、陶瓷砂、刚玉和碳化硅用于表面清洁、粗糙化处理、形成亚光效果和去除毛刺。它们仅可用于压缩空气喷砂系统。

金属非铁质喷砂介质:
- 黄铜屑、小黄铜颗粒、黄铜切丝、铝颗粒、铝切丝、锌颗粒和锌切丝均用于表面清洁和去毛刺。它们可用于抛丸系统以及压缩空气吸入(喷射)和压力喷砂系统。
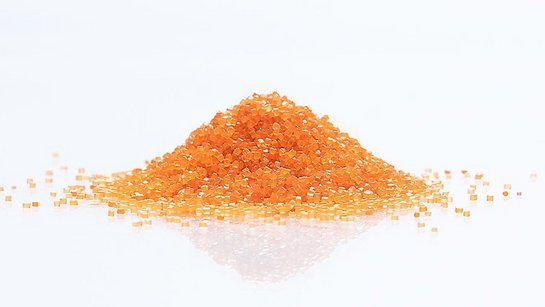
天然矿物喷砂介质:
- 石榴石砂、苏打砂和石英砂适用于脱漆、除垢、除锈、表面清洁、打造亚光效果和去毛刺。它们仅可用于压缩空气吸(喷)射机和压力喷砂机。然而,对于石英砂,这一说法并不完全准确:在许多国家,包括德国,都禁止使用石英砂进行喷砂,因为它会以矽肺病的形式对健康构成严重危害。在湿式喷砂工艺中,由于不会产生粉尘,因此仍可使用石英砂。
用户还必须在处理小批量至极小批量、大规模生产的零件的完整批次,还是单件处理之间做出选择。典型的批量处理系统包括滚筒式抛丸机、多滚筒抛丸机和带旋转篮的手动抛丸柜。旋转吊钩抛丸机可用于单件处理以及较大工件的批量处理。最常见的是辊式输送带和钢丝网带抛丸机,它们可用于各种抛丸应用;而机器人抛丸机则用于特殊任务和敏感工件的处理。我们工厂出厂的抛丸机中,有90%是为客户定制设计的,以精确满足客户的需求。
Rösler主要销售抛头和抛丸机,因为它们功率大且处理时间短,同时,公司每年也会向世界各地需要解决复杂任务的客户交付多台机器人设备。每当需要处理大面积表面时,涡轮式抛丸机都是最具成本效益的解决方案。此外,与涡轮式抛丸机可实现的吞吐量相比,其成本支出和运营成本相对较低。