用途广泛,满足各种使用要求
Rösler的光饰技术可用于超过 1,000 种表面加工用途。无论是金属、塑料、陶瓷还是木材等材料,也无论是除毛刺、除油脂、除锈或是抛光等技术,Rösler的光饰设备用途非常全面,没有任何材料工艺限制,让用户安全并且放心地用于例如航空、医疗器械、汽车行业或珠宝首饰、硬币等各种各样的行业。在当下,每一个工件都会出于功能或美学考虑而需要表面处理。因此,我们的振动光饰技术是来源于自然的技术,在添加磨料和化合物的情况下模拟大自然河床中的沙子、水和鹅卵石之间的摩擦动作,从而对表面进行光饰处理。
此外,较之于竞品工艺,振动光饰技术具有许多优点,即通过各种工艺的搭配组合,可同时执行多个工作步骤。因此,加工过程时间显著缩短、更节约资源,且经济效益更高。
如:
- 本公司开发/生产的约 15,000 种工艺介质
- 匹配的周边设备,如可持续性干燥解决方案、节约资源的离心机技术,或工业清洗设备
- 数字化工艺用水监测,实现更稳定和经济的过程
- 享受专业咨询服务,并在我们的全球客户体验中心进行各种测试
- 个性化定制服务合同
- 本公司服务和应用工程师在全球现场提供支持
- Rösler 学院对您的专业人员进行培训和进修
- 最先进的生产车间,垂直化生产中的佼佼者
我们为您提供的所有一站式工艺辅助产品全都出自于本公司,这就是我们引以为傲,并且也能让您具备独占鳌头的优势!
我们为您定制个性化流程——专业化定制

拿厨艺来打个比方:仅仅知道如何正确地使用食材并不能成为大厨。只有结合适当的经验、各项配料的用量恰到好处,才能呈现出最佳的结果。当然,我们的振动光饰技术也是如此。
过去 90 年里,Rösler 公司在振动光饰技术方面积累了丰富的经验,当然作为客户,您也可以从中受惠。我们在全球客户体验中心,为各行各业进行了数万次试验,这一点对我们工艺技术的持续发展至关重要。秉承着本公司“Findig a better way”的理念,不论是标准流程、特殊解决方案还是高度自动化的生产单元,我们都能轻松掌握,因此我们希望成为贵司质量和经济效益方面的优势,凭借我们全球独特的服务组合,为您的表面加工带来最佳效果。
Rösler 为您带来附加价值——动态发展、可持续性、经济效益
不计其数的振动光饰工艺以及如今运用于全球各地的各种设备,都是由我们定制,并满足特定的客户要求。
例如,许多高科技行业在对复杂的、高质量的精密部件进行精加工时,都依赖于 Rösler 表面修整器。我们的六轴关节臂机器人能够对工件进行工艺可靠、经济可行和可重复的精加工,在从前,这类工序对其中一部分只能由手工完成。
从资源保护的角度来看,对工艺用水进行生态化合理利用也变得越来越重要。由于我们在机器技术和工艺介质(磨料、化合物和工艺用水净化器)方面的不断发展,现在几乎所有的振动光饰工艺都可以与 Rösler 工艺用水系统实现联动,利用循环系统技术对振动光饰过程中产生的工艺用水完全回收利用。您也可以采用本公司新设立的品牌 Rösler Smart Solutions 旗下的数字化工艺用水管理系统,该系统在任何时间任何地点都可以对产品工艺进行检测,并且在必要时为您快速提供简单易行的最佳处理建议。
我们的 RT Euro-DH 旋转干燥器也能够大幅提高振动光饰过程中的可持续性。我们为这个最新规格的产品配备了新开发的热块加热元件,可节省高达40%的能源,从而为您提供一个以环保和可持续方式进行振动光饰的完美解决方案。
振动光饰技术的关键点是什么?请浏览常见的问题
批量光饰、滚磨表面处理和振动光饰是描述同一技术的不同术语,即通过机械方式对工件进 行表面处理。该技术使用抛光或研磨介质(通常也称为“磨料”或“滚磨石”),并通常配 合液体添加剂(水与化合物的混合液),在振动光饰机、离心机或拖拽 冲浪式振动光饰机 等专用设备中进行操作。类似的工艺是滚轧精整,其中材料在不振动的情况下仅通过旋转运 动被去除。
在振动光饰加工过程中,设备驱动介质与工件产生持续“摩擦”作用。由此产生的(显著程 度不一的)磨损会去除工件表面材 料,从而实现去毛刺、表面平整、抛光或清洁等效果。 振动光饰广泛应用于多个行业。例如,它既可用于处理汽车车轮或大型船用螺旋桨等单个大 型部件,也能以经济、可控的方式对大批量小型工件进行一致性表面处理。
在最常见的振动光饰机中,介质 和工件的运动是由振动引起的:与由树脂或陶瓷制成的合适 的研磨或抛光介质一起,将未经处理的未加工工件放入圆形或矩形加工碗中。带有不平衡装 置的电机会在滚筒中产生振动,并导致介质持续摩擦工件。这将导致从工件表面去除材料。 主要通过添加液体化学化合物,可实现防腐、去油或一般清洁等额外表面处理效果。
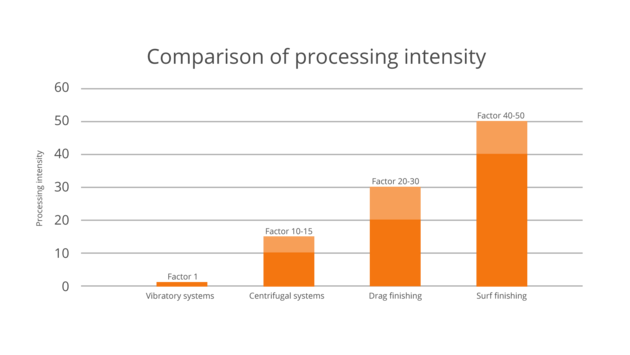
用于加工大量非精密工件的最受欢迎的振动光饰设备是旋转振动机,其有不同版本和尺寸 可供选择。只要工件尺寸不过大且不易碎,这类设备几乎能对所有材质的工件进行表面处 理。对于加工较长且相对笨重的工件,可采用带有矩形处理槽的桶式振动机。与振动设备 相比,离心盘振动机、拖拽式及冲浪式等特殊振动光饰系统具有显著更高的加工强度,可 在极短周期内完成疑难加工材料的处理。例如,由 Rösler 优化的冲浪式振动光饰技术是当 前市场上强度较高的光饰技术工艺 ,其加工强度可达传统振动系统的 50 倍。拖拽式与冲浪 式振动光饰技术的另一优势在于,整个加工过程中工件互不接触,这对骨科植入物、喷气 发动机零件等极端精密工件的处理尤为关键。
-
去毛刺
许多用户使用振动光饰技术主要用于去毛刺,即去除锐边、以锋利形式溢出的材料以及前 道工艺制造步骤产生的一般边缘缺陷。多数情况下,只有在工件进行了振动光饰作业(通 常称为“滚磨”)之后,才可能进行进一步的后道制造工艺。通过适当的研磨和抛光介质 和化合物,几乎所有材料,甚至树脂、木材和橡胶制成的工件都可以进行处理。 -
抛光
抛光是振动光饰技术中最重要的应用之一。抛光目标可以是纯粹的观赏价值,但它们也可 以是功能性的,例如减少摩擦。抛光的特点是磨损极小,仅去除少量材料,却能使工件表 面变得极其平滑和光亮。通过结合使用不同介质与特殊抛光剂(如膏状抛光剂),并采用 多步骤工艺,来实现高光泽度的表面。 -
表面清洁
清除工件表面的污垢、氧化物层和其他污染物。与其他表面处理作业一样,清洁在许多情 况下是安全有效的后道制造工艺的必要先决条件。例如,拉深工件上覆盖有油和润滑脂, 必须清洁后才能进行进一步加工。振动光饰也用于一些不寻常的应用,如大规模的美食操 作中的餐具清洁或硬币坯饼的清洁和抛光。 -
边缘倒角
边缘倒角是一种特别密集的去毛刺工艺,是批量光饰的另一个重要应用。在前道工艺作业 中通常会产生锐边和毛刺。这种锐边的半径(倒圆)会 产生许多积极的效果:它有助于减 少后道工艺设备的磨损,并减少装配操作中受伤的风险。此外,它还增加了各个部件的使 用寿命。并且,如果对部件进行涂覆,则提高了涂层的耐用性。
振动光饰技术几乎适用于所有工业领域:
- 汽车工业中用于变速箱部件、活塞环或轴承零件 的去毛刺、表面平滑及抛光;亦适用于可见部件和汽车轮毂的表面 处理 。
- 在航空航天工业中用于涡轮叶片及其他高精度部件的去毛刺和表面光整加工。
- 在医疗工程中用于抛光骨科植入物,如髋关节和膝关节,以及手术器械。
- 在机械制造领域,用于工具、轴承部件及机械总成 的表面处理 。
- 在珠宝行业中用于对贵金属制成的小饰品进行抛光和打磨。
- 用于外壳表面处理和电气接触区域的电子元件。