Onbegrensde toepassingsmogelijkheden – ongeacht de behoefte
Rösler-glijslijptechniek biedt u meer dan 1.000 mogelijkheden voor oppervlaktebewerking. Of het nu gaat om metaal, kunststof, keramiek of hout, of om bewerkingen zoals ontbramen, ontvetten, walshuid verwijderen, ontroesten of polijsten: glijslijpinstallaties zijn bijna oneindig toepasbaar en bewijzen zich al tientallen jaren dag in dag uit in tal van industriële sectoren, zoals de luchtvaart, medische technologie, de automobielindustrie of munt- en sieradenindustrie. Tegenwoordig kan bijna geen enkel werkstuk meer zonder een functionele of esthetische oppervlakteafwerking. De glijslijptechniek gebruikt de natuur als model en polijst met toevoeging van slijpmedia en compounds het oppervlak glad, zoals zand en water de kiezels in een rivierbedding polijsten.
In vergelijking met concurrerende processen biedt de glijslijptechniek een doorslaggevend voordeel: door het combineren van processen kunnen vaak meerdere processtappen tegelijk uitgevoerd worden. Daardoor is het bewerkingsproces aanzienlijk korter, zuiniger met grondstoffen en economischer.
Al uw procesingrediënten uit één hand – ons aanbod voor u
Als markt- en technologieleider in glijslijpen bieden wij u een haast ongelimiteerd aanbod van de meest verschillende glijslijpsystemen. Ons productportfolio omvat robuuste alleskunners zoals de duizendvoudig bewezen rondvibrator, maar ook volautomatische systemen met hoge precisie, zoals onze sleep-finisher en surf-finisher, tot geautomatiseerde gekoppelde (interlinked) systemen.
Na uw keuze voor een van onze installaties gaat uw reis door de productenwereld van Rösler gewoon verder. Want met onze allround Rösler-service leveren wij u ook alle componenten, randoplossingen en diensten optimaal en individueel afgestemd op uw eisen.
Onze service omvat onder meer:
- Keuze uit ca. 15.000 zelf ontwikkelde/geproduceerde procesmedia
- Afgestemde randapparatuur, zoals duurzame droogoplossingen, grondstoffen besparende centrifugetechnologie en ook industriële reinigingssystemen.
- Digitale proceswaterbewaking voor stabielere en zuinigere processen
- Deskundig advies en uitgebreide tests in onze wereldwijde Customer Experience Centers
- Servicecontracten op maat
- Wereldwijde ondersteuning door onze eigen service- en procestechnici bij u in de buurt
- Training en bijscholing van uw vakmensen in onze Rösler Academy
- De modernste productiefaciliteiten met een uniek verticaal productiebereik.
Wij bieden u alle procesingrediënten, niet alleen uit één bron, maar uit onze eigen bron. Dit maakt ons uniek en u succesvol!
Deskundig maatwerk – wij ontwikkelen uw proces speciaal voor u

LOm een vergelijking met de kookkunst te gebruiken: alleen gebruik van de juiste ingrediënten maakt iemand nog geen meester-kok. Alleen in combinatie met de juiste ervaring en de juiste dosering van de afzonderlijke ingrediënten ontstaat een optimaal resultaat. Zo is het ook in de glijslijptechniek.
Wij van Rösler putten uit de rijke ervaring die we in de afgelopen 90 jaar in de glijslijptechniek hebben opgedaan – en daarvan kunt u de vruchten plukken. Onze proces-knowhow blijven wij voortdurend doorontwikkelen in honderdduizenden tests voor de meest uiteenlopende branches in onze wereldwijde Customer Experience Centers. Trouw aan ons bedrijfsmotto “finding a better way” willen wij voor u doorslaggevende concurrentievoordelen genereren op het gebied van kwaliteit en efficiëntie. Of het nu gaat om een standaardproces, een speciale oplossing of sterk geautomatiseerde productiecellen. Dankzij onze wereldwijd unieke dinestenportefeuille zijn uw oppervlakken bij ons in de beste handen.
Dynamisch, duurzaam, economisch – uw meerwaarde dankzij Rösler
Talrijke glijslijpprocessen en -systemen die tegenwoordig wereldwijd worden toegepast - zijn bij ons aangepast aan de specifieke eisen van de klant.
Veel hightech industrieën vertrouwen voor de nabewerking van complexe, hoogwaardige precisiecomponenten op de Rösler Surf-Finisher. Met zijn zesassige knikarmrobot maakt deze procesbetrouwbare, economisch rendabele en reproduceerbare nabewerking mogelijk van werkstukken die voorheen in sommige gevallen zelfs nog met de hand moesten worden bewerkt.
Het ecologisch verantwoord gebruik van proceswater wordt steeds belangrijker vanuit het oogpunt van zorgvuldig en respectvol omgaan met hulpbronnen. Door onze permanente ontwikkeling in machinetechniek en procesmedia (chips, compounds en proceswaterreiniger) kan tegenwoordig bijna elk glijslijpproces aan een Rösler proceswater recyclingsysteem gekoppeld worden. Het, tijdens het glijslijpen geproduceerde proceswater wordt vervolgens volledig gerecycleerd met behulp van recirculatiesystemen. Dit proces kan met het digitale proceswatermanagement van ons nieuwe merk Rösler Smart Solutions vanaf elke locatie 24 uur per dag worden bewaakt en biedt u indien nodig snel en eenvoudig optimale aanbevelingen voor maatregelen.
Met onze RT Euro-DH ronddroger hebben wij een nieuwe stap gezet naar meer duurzaamheid in het glijslijpproces. Deze nieuwste versie is voorzien van nieuw ontwikkelde verwarmingselementen die energiebesparingen tot 40 procent mogelijk maken, zodat u uw glijslijpoplossing op een milieuvriendelijke en duurzame manier compleet kunt maken.
Wat moet u weten over glijslijpen?
Overzicht van veel gestelde vragen.
Glijslijpen, trowaliseren of vibrerend slijpen zijn drie verschillende benamingen voor één en hetzelfde proces: de mechanische oppervlaktebewerking van werkstukken met behulp van slijpmedia (vaak ook stenen of chips genoemd) en meestal een vloeibare toevoeging (water en compound) in een vibrerende installatie. Een soortgelijke methode is het trommelen, waarbij het materiaal echter zonder trillingen en alleen door een draaiende beweging wordt verwijderd.
Bij glijslijpen wordt materiaal door abrasie en wrijving van het oppervlak verwijderd om het te ontbramen, glad te maken, te polijsten of ook te reinigen.
Het proces wordt in vrijwel alle industriële sectoren toegepast. Hoewel het ook kan worden gebruikt voor het bewerken van grotere afzonderlijke onderdelen (velgen of zelfs scheepsschroeven), komt het volledige potentieel van glijslijpen vooral tot zijn recht wanneer een reproduceerbare, kostenefficiënte en eenvoudig te regelen bewerking van grote werkstukken vereist is.
Bij glijslijpen worden de werkstukken samen met de kunststof of keramische slijpmedia in een ronde of trogvormige bak geplaatst. Deze wordt met behulp van een motor in trilling gebracht. Hierdoor ontstaat een relatieve beweging tussen het werkstuk en de slijpmedia, waardoor materiaal van het oppervlak van het werkstuk wordt verwijderd. Door toevoeging van compounds, meestal vloeibare bewerkingsadditieven op chemische basis, kunnen extra effecten worden bereikt, zoals corrosiebescherming, reiniging of ontvetting.
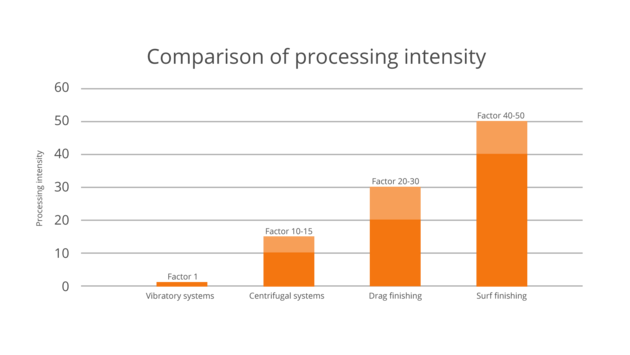
De klassieke glijslijpinstallatie voor de massaproductie van ongevoelige onderdelen is de rondvibrator, die in verschillende maten en uitvoeringen verkrijgbaar is. Hierin kunnen bijna alle materialen en werkstukken worden bewerkt die niet te groot en niet te kwetsbaar zijn. Voor lange of omvangrijke onderdelen is bewerking in rechte vibratoren een goede oplossing. Speciale processen zoals glijslijpen in centrifugale installaties en sleep- en surf-finishers kunnen de effectiviteit van het bewerkingsproces enorm vergroten en zelfs de hardste materialen in korte tijd bewerken. Het door Rösler geoptimaliseerde surf-finishing-proces bijvoorbeeld is de krachtigste vorm van glijslijpen – en tot wel 50 keer zo effectief als de bewerking in een gewone glijslijpinstallatie. Tegelijkertijd maken deze vormen van contactloos glijslijpen de bewerking van zeer kwetsbare onderdelen mogelijk, bijvoorbeeld voor medische technologie of voor de luchtvaart.
-
Ontbramen
Veel gebruikers gebruiken glijslijpen in de eerste plaats voor het ontbramen, dus voor het verwijderen van storende randen, kanten en bramen uit het voorgaande productieproces. Hierbij wordt vooral duidelijk dat trowaliseren of glijslijpen in eerste instantie een proces is dat nodig is voor de verdere verwerking van de onderdelen. In combinatie met de juiste procesmiddelen kunnen vrijwel alle materialen met behulp van het glijslijpen worden ontbraamd, zelfs kunststof, hout of rubber. -
Polijsten
Het polijsten is een van de belangrijkste toepassingsgebieden van de glijslijptechniek en heeft zowel esthetische als functionele redenen, bijvoorbeeld wanneer wrijving moet worden verminderd. Het gaat hierbij om een extreem nauwelijks slijpend bewerkingsproces waarbij het oppervlak van het werkstuk zo glad mogelijk moet worden gemaakt. Extreem fijne oppervlakken worden bereikt met verschillende slijpmiddelen en pasta's of polijstmiddelen, vaak in meerdere stappen. -
Reinigen
Verwijderen van vuil, oxidelagen of resten van het oppervlak van het werkstuk. Ook dit proces is vaak een voorwaarde voor verdere verwerking van de onderdelen en is vast verankerd in het productieproces. Bijvoorbeeld wanneer werkstukken met behulp van oliën en vetten in een dieptrekproces zijn vervaardigd en vervolgens voor verdere verwerking moeten worden gereinigd. Ook voor het reinigen van bestek in grootkeukens of voor het reinigen van munten worden glijslijpinstallaties gebruikt. -
Randen afronden
Ook voor het afronden van randen is glijslijpen een effectieve bewerkingsoplossing. Scherpe randen zijn, net als bramen, het gevolg van het voorgaande productieproces. Het afronden heeft veel positieve effecten: het biedt bescherming voor de verdere verwerkingsmachines, vermindert het risico op letsel bij de verdere verwerking en zorgt bijvoorbeeld voor een langere levensduur en een gelijkmatige coating.
De glijslijptechniek wordt in alle industriële sectoren toegepast. Deze wordt onder andere gebruikt:
- In de automobielindustrie voor het ontbramen en polijsten van transmissieonderdelen, zuigerveren en kogellager delen en voor het verbeteren van de oppervlaktekwaliteit van zichtdelen en velgen.
- In de lucht- en ruimtevaart voor het gladmaken en ontbramen van turbineschoepen en andere hoog precisie delen.
- In de medische technologie voor het polijsten van implantaten (bijv. heup- en kniegewrichten en tandprothesen) en chirurgische instrumenten.
- In de machinebouw voor de oppervlakteafwerking van gereedschappen, kogellager delen en machine-componenten.
- In de sieradenindustrie voor het polijsten en gladmaken van sieraden van edelmetalen.
- In de elektronica-industrie voor de oppervlaktebehandeling van contactdelen en behuizingen.