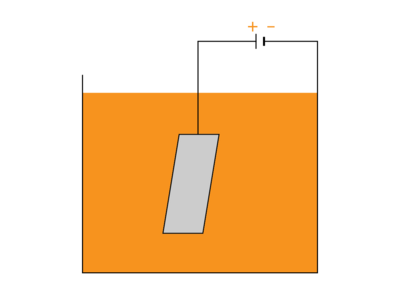
Liquid electropolishing
- The liquid electrolyte touches all surface areas
- Oxidation occurs on all contact areas (also in the valleys of the surface roughness profile)
- Comparatively less selective finishing of the surface
The dry electropolishing method, developed by the Spanish tech company GPAINNOVA, is an innovative technology for finishing the surface of metal components. It refines the surface considerably better than manual grinding and polishing operations - just in one single step! Compared to other processes, such as liquid electropolishing, it has numerous advantages. For example, work pieces treated with the dry electropolishing method have a highly homogeneous surface without any micro scratches or indentations. DryLyte allows extremely tight dimensional tolerances and generates mirror finishes. In addition, the process is much less detrimental to the environment than liquid electropolishing. Moreover, operating the machines and handling the consumables is very easy.
The DryLyte technology is utilized in the GPAINNOVA DLyte equipment that is exclusively sold in Germany by Rösler. The machines can be fully automated and easily integrated into complex manufacturing lines.
DryLyte is a patented technology for surface grinding, polishing, deburring and edge radiusing of metal components. The dry electropolishing method does not remove material from the work pieces through mechanical abrasion but through an ion exchange between the metal components and an electrolyte embedded in polymer granules.
The surface of the work pieces has a positive electrical charge, whereas the electrolyte is negatively charged. The electrical flow in the processing bowl and the motion of the work pieces against the electrolyte granules causes a gentle and highly controlled removal of material from the work pieces. The material removal is limited to the roughness peaks of the work piece surface. The DryLyte system does not cause unwanted rounding of edges and, because the polymer granules are extremely small, they reach tight surface areas, which cannot be accessed by mechanical grinding. Dry electropolishing achieves the same smoothing effects as liquid electropolishing but removes considerably less material.
Compared to conventional electropolishing the DryLyte technology utilizes a selective finishing approach. This results in fast removal of roughness peaks and increases the relative material ratio (Rmr). But that is not the only advantage of the DryLyte system:
- The liquid electrolyte touches all surface areas
- Oxidation occurs on all contact areas (also in the valleys of the surface roughness profile)
- Comparatively less selective finishing of the surface
+ The polymer granules remove only the roughness peaks
+ Precisely targeted oxidation
+ Selective removal of metal
+ DryLyte maintains the most intricate work piece geometries
+ The corrosion resistance of the work pieces is maintained
DryLyte generates homogeneous finishing results on the entire work piece surface and removes micro scratches.
DryLyte ensures compliance with tight dimensional tolerances by maintaining the original work piece shape, including the edges. This guarantees extremely precise finishing results.
DryLyte reduces not only the surface roughness by more than 80% but also prevents unwanted side effects. Liquid electropolishing reduces the surface roughness at most by 50%, before it creates side effects like an orange peel finish or pitting.
Removes metal evenly on the entire work piece surface, all the way to the roughness valleys.
The DryLyte technology guarantees consistent finishing results, batch after batch, throughout the service life of the electrolyte medium. Physical wear, as happens with abrasive media, does not take place.
It allows an even distribution of the lubricating film, improves the load bearing characteristics of the bearing and minimizes friction loss between the bearing components.
Reduces the wear rate of numerous materials, lowers the risk of breakage, improves the fatigue life and improves the surface characteristics on metal components. It removes embedded free iron particles, surface contaminations, discoloration due to heat and oxide scale.
For the surface finishing process only polymer granules containing acid are utilized. The media is made from high-quality ingredients. This ensures compliance with the strictest cost-benefit standards regarding biocompatibility and toxicity.
This is the only finishing technology that reduces surface roughness and improves the corrosion resistance on metal components. At the same time, it reduces the number of required treatment steps in the manufacturing process.
The use of cemented carbides made from tungsten or sintered carbide in the tool making industry has been steadily increasing. In the past these materials were frequently considered to be too prone to breakage and too brittle for volume production. Thanks to extensive new developments, carbides have become a high-value material group that can be used for numerous applications. However, surface finishing of hard metals is still difficult: Standard mechanical surface refinement methods, for example, for polishing, are not effective on tungsten carbide, because this material is too hard. And the desired surface improvement is only achieved at the expense of uncontrolled rounding of the work piece edges. Chemical or electro-chemical alternatives are not feasible either, because they cause leaching of the material.
The new, innovative DryLyte technology of our partner GPAINNOVA offers the perfect solution: It gently smoothens and polishes carbide without affecting the structural integrity of the work pieces. This ensures that the original physical characteristics of the respective material are maintained. At the same time, an impressive finishing quality is achieved in surprisingly short cycle times. This results in improved productivity and efficiency of industrial manufacturing processes.
We are the globally exclusive partner of GPAINNOVA for the sales of DLyte Carbide systems and cooperate closely to further improve the processes and the equipment in the field of carbide surface finishing with dry electropolishing.
The experts in our Customer Experience Centers (CECâs) can offer you a broad range of experience and know-how in the field of hard metal surface finishing with the DryLyte technology. Why donât you send us your work pieces for a processing trial? We guarantee the proven Rösler all-round service for all applications of the DryLyte technology.
The DryLyte technology produces more precise and homogeneous finishing results than conventional grinding methods, which in the tool industry frequently still consist of manual operations. The material removal takes place with an electro-chemical process that is defined by the number of contacts of the medium (polymer granules) with the work piece surface and the applied electrical voltage.
Another significant advantage of the DryLyte technology: The system prevents any âchelatingâ of the upper metal layers at the grain boundaries. This guarantees the overall stability and durability of the processed work pieces.