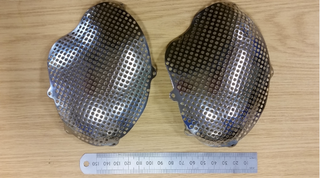
Patient-Specific Implants Call for Equally Customized Processing
, sramaker - ZurĂŒck zur Ăbersicht
Advancements in medical technology now allow for the development of Patient-Specific Implants (PSI). Specialized computer programs analyze x-rays, ultrasound, and MRI images to create surgical guides, tools, and implants tailored to the patientâs unique anatomy.
While still emerging, many medical industry suppliers have received FDA approval for PSI use. Like traditional implants, these implants must be carefully finished once created to ensure the work piece meets stringent medical safety standards while promoting patient comfort and long wear life.
The benefits of PSI use include shorter surgery times, better surgical outcomes, and cost savings.
True to its âapply innovationâ tagline, Renishawâs Medical and Healthcare Division has found great success in additively manufacturing PSI. Using CT scan-to-CAD software, one of the companyâs most innovative advances is creating cranial plates using titanium powder.
When determining how to finish the implants to precise medical requirements and surgical demands, Renishaw trusted Rosler for help with mass finishing.
The Challenge
Renishaw cranial plates after polishing
Original commissioning neurosurgeon BartolomĂ© Oliver required the surface of Renishawâs cranial PSI to be satin-like in order to best match the patient's cranial contours. Renishaw Applications Engineer Andy Wescott's job then became creating a repeatable and streamlined process to apply a satin and highly polished finish to the top of the cranial plates from their as-built condition.
"Traditionally, post-processing these parts to a low surface roughness value was very manual and time-consuming," Wescott said. "The post-process time for a large cranial plate was up to five hours. We needed to reduce that time and the amount of manual input because if an operator working on a part loses concentration for one second, they could burn a hole in your part.
âThat makes one expensive bit of scrap."
Finding a Better WayâŠ
Since metal additively printed parts are now of such quality, they can be treated like any other metal part. And Rosler knows a thing or two about surface finishing metal parts, having been in the post-processing game with its mass finishing and shot blasting divisions for more than 80 years.
A more mechanized solution presented itself in the form of Roslerâs High-Energy Centrifugal Disc Finishing Machine FKS04.
Now, after a cranial plate comes out of the Renishaw AM250 machine, it undergoes only a small amount of manual operation to remove supports from printing and slightly improve the surface using a carbide burr and flap wheel.
It is then placed into Roslerâs FKS where it automatically goes through a three-step process to produce the impeccably smooth finish, reducing manual operating time to under an hour.
The clever part, which ensures repeatability on each and every part, comes from a little bit of Renishaw engineering know-how.
"We designed a tool to hold our parts in a particular orientation inside the tumbling bowl,â Wescott said. âRather than just throwing parts into three media types and coming out with a sort of fixed part, our parts require precision. Certain features require protection from the tumbling media, so we've invented a tooling method that keeps parts face down in the media and only applies the surface finish where needed."
The Rosler Way
Although there isnât a one-size-fits-all solution for finishing, the collaboration between Renishaw and Rosler demonstrates that post-processing doesnât have to be a grueling experience. Much like the additive manufacturing process itself, your finishing technique depends on your unique application. Contact Rosler today for help in finding a better way to meet your finishing needs.