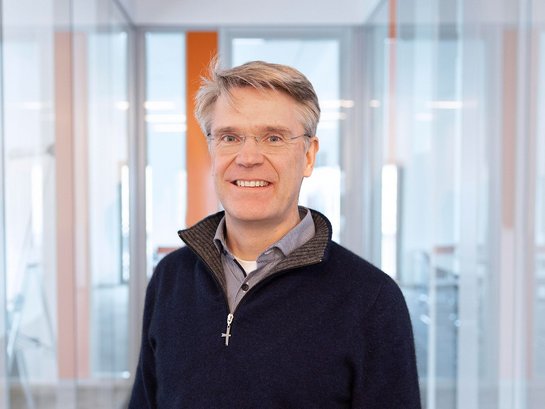
L'état d'esprit Rösler définit de nouvelles normes
L'état d'esprit Rösler définit de nouvelles normes
Finition miroir de jantes forgées haut de gamme en moins de 40 minutes
Réduction des coûts et augmentation de la productivité du grenaillage de précontrainte
AM Solutions va produire en série des machines standards de post-traitement de pièces 3D
Lancement du New Work concept "Rösler Innowelt".
Ces dernières années, nous avons dû revoir de nombreux paramètres, considérés jusqu'alors comme acquis. Aujourd'hui, nous devons trouver de nouveaux moyens pour garantir un avenir stable. Une voie vers une nouvelle "normalité" dans les affaires, la technologie et la politique est incertaine et difficile, mais pour assurer notre succès, nous devons relever ce défi de front. Dans nos efforts pour adapter notre activité à l'évolution rapide du marché, nous pouvons nous appuyer sur les atouts spécifiques de Rösler qui ont fait le succès de notre entreprise par le passé. Ces forces constituent une excellente base pour créer un avenir fructueux pour l'entreprise.
Rösler possède de nombreuses forces qui constituent une base solide pour faire face à tout nouveau défi : L'entreprise dispose de technologies et de produits éprouvés avec un excellent potentiel de marché. En outre, l'entreprise possède de nombreuses forces intrinsèques et, avec le slogan "Finding a better way", nous avons une ligne directrice, qui définit notre état d'esprit. Pour moi, cela signifie que même dans les moments difficiles, nous regardons vers l'avant et travaillons pour l'avenir. Nous avons la chance de pouvoir nous appuyer sur des produits et des processus éprouvés, tout en ayant la capacité de développer des concepts innovants.
Un bon exemple de cette combinaison de méthodes éprouvées et innovantes est un projet de traitement sur jantes que nous avons réalisé pour un grand client. Les méthodes traditionnelles permettent d'obtenir les résultats de finition visuels requis, mais elles peuvent aussi être complétées par de nouvelles idées pour améliorer encore le processus de traitement. Dans ce projet particulier, la solution a été un système spécial et innovant de Tribofinition mono-broche. Cette approche fonctionne également sur des pièces métalliques exposées à des charges élevées. Les résultats requis sont généralement obtenus par grenaillage de précontrainte, une technologie éprouvée depuis longtemps. Aujourd'hui, nous avons mis au point des améliorations qui rendent cette technologie encore meilleure, plus efficace et plus rentable : Grâce à un logiciel spécial, nous pouvons simuler numériquement le processus de grenaillage de précontrainte sur n'importe quelle géométrie de pièce donnée. Cela nous permet de définir précisément les paramètres du processus dès la phase de conception, de sorte que rien ne soit laissé au hasard.
Nous nous efforçons également d'améliorer notre culture d'entreprise : À cette fin, nous recherchons de nouvelles méthodes de travail et les mettons en œuvre avec notre "Rösler Innowelt" - un concept de bureau conforme à l'idée du New Work, avec un espace de travail ouvert et partagé. Cela renforcera notre coopération et notre communication internes. Associé à des outils numériques spéciaux et à des logiciels de gestion, il nous permettra de réagir plus rapidement et avec plus de souplesse aux demandes des clients. Les mêmes outils numériques seront également utilisés dans notre production. Dans un premier temps, nous avons centralisé les opérations de fabrication des équipements de notre marque AM Solutions - 3D post processing technology. Pour répondre aux exigences d'industrialisation de la fabrication additive, nous construisons en série dans cette nouvelle unité de production des équipements de post-traitement pour pièces issues de la fabrication additive.
Tout cela ne serait pas possible sans notre état d'esprit Rösler : Se baser sur des produits et des processus éprouvés et les améliorer avec des idées innovantes. Chaque jour nous permet de commencer quelque chose de nouveau et de nous aventurer dans de nouveaux domaines. Nous pouvons ainsi sortir de notre ancienne "normalité" et, avec "finding a better way", créer une nouvelle "normalité" qui garantit la stabilité en période de changement rapide. Grâce à cette approche, nous aidons nos clients du monde entier à surmonter les périodes difficiles et à relever avec succès les nouveaux défis du marché. Et nos collaborateurs pourront travailler dans un environnement stable qui leur permettra d'envisager l'avenir avec confiance.
J'espère que vous prendrez plaisir à lire notre nouveau bulletin d'information. Nous avons de bonnes raisons d'être optimistes !
Bien cordialement.
Dr. Till Merkel
Les jantes en aluminium forgé se caractérisent non seulement par leur faible poids, leur grande stabilité et leurs excellentes caractéristiques de résistance à la charge, mais aussi par leur aspect visuel exclusif. Il n'est donc pas surprenant que les constructeurs de voitures de luxe utilisent principalement des jantes en aluminium forgé dans leurs véhicules. Les caractéristiques visuelles des jantes automobiles haut de gamme ne sont pas seulement leur design attractif, mais aussi leur surface brillante et immaculée. Pour obtenir une finition aussi parfaite, les jantes doivent subir une opération de préparation et de lissage de surface avant d'être polies. Le traitement manuel des jantes ou avec des méthodes de Tribofinition classiques sont coûteux et nécessitent plusieurs heures de traitement. Un grand fabricant de jantes souhaitait réduire de manière significative le temps nécessaire au traitement partiel de jantes bicolores déjà peintes et recherchait une solution technique adaptée. Cette solution a été trouvée avec la machine Tribofinition mono-broche Rösler R 1/1 TSA-O/VS-So. La technologie de traitement par broche a été développée par Rösler pour l'ébavurage, le rayonnage, la finition et le polissage de pièces complexes, lourdes et délicates.
Processus en deux étapes avec des médias et des composés spécialement adaptés
L'opération de traitement pour la finition des jantes bicolores était particulièrement difficile : la peinture déjà appliquée ne devait pas être endommagée et, dans le même temps, les surfaces à traiter devaient recevoir un fini brillant immaculé. Le processus se déroule comme suit : Grâce à un système de serrage pneumatique, une seule jante est fixée à la broche de la machine de traitement par immersion. Le système de serrage spécialement conçu permet le montage manuel ou robotisé des jantes. En abaissant la broche rotative, la jante est immergée dans la cuve de traitement remplie d'un média de Tribofinition ou de polissage spécial. Pour l'opération de polissage, on utilise un média plastique en forme de cône spécialement conçu pour cette application de finition particulière. Le processus est soutenu par l'ajout continu d'eau et d'un composé approprié. Au cours du processus, la broche effectue une rotation centrique, orbitale ou réciproque. Les différents mouvements de rotation peuvent également être combinés. Le mouvement qui en résulte permet d'obtenir des finitions de surface cohérentes et homogènes, même sur les détails les plus complexes des jantes. La répétabilité et l'homogénéité des résultats obtenus étaient des conditions essentielles pour que le processus de finition par immersion soit adapté à la production en série. Cela est possible grâce à des caractéristiques techniques spéciales telles que le moteur vibrant intégré à la cuve de traitement et un système intégré de classification des médias usés. Ces deux éléments assurent un mélange stable des médias, ce qui garantit une qualité de finition constante.
L'opération d'ébauche est suivie d'un cycle de meulage fin d'environ sept minutes. Pour le polissage haute brillance, les jantes sont ensuite immergées dans une seconde cuve remplie de médias de polissage en porcelaine. L'opération de polissage nécessite un temps de traitement de 25 à 30 minutes.
Économie des ressources en eau et en composés
Pour le recyclage des eaux usées, un système de traitement chimique de l'eau, spécialement conçu pour minimiser la consommation a été installé. Il est principalement utilisé pour traiter les effluents issus de l'opération de finition. L'eau de traitement légèrement contaminée provenant du processus de polissage est collectée dans un réservoir tampon et recyclée pour l'étape de finition. Les composés nécessaires à chaque étape du processus sont automatiquement distribués. La réutilisation de l'eau de traitement de l'étape de polissage pour la phase de finition permet également de réduire la consommation globale de composés.
Le client a été impressionné non seulement par les caractéristiques techniques, mais aussi par la rentabilité de la technologie de ce traitement par immersion. Il n'est donc pas surprenant qu'il ait déjà commandé des installations supplémentaires pour la prochaine phase d'expansion de sa ligne de production de jantes.
Le grenaillage de précontrainte, c'est-à-dire le "martelage" de pièces à l'aide de grenailles définies spécifiquement, est une opération indispensable dans des secteurs tels que l'automobile et l'aéronautique. En induisant une contrainte de compression résiduelle dans les pièces, l'opération de grenaillage de précontrainte améliore considérablement leur résistance à long terme aux charges de traction et de flexion. Le procédé est utilisé pour traiter les engrenages, les pièces de direction et de transmission, ainsi que les ressorts, les arbres de transmission et les vilebrequins, tous les types d'aubes de turbine et de nombreuses pièces d'aéromoteurs. Un avantage significatif de l'opération de grenaillage de précontrainte est que le poids de la pièce peut être réduit sans affecter ses capacités de charge mécanique. Cette opération est particulièrement bénéfique pour les véhicules électriques, car elle permet d'augmenter leur autonomie et de réduire leur consommation d'énergie. En raison de l'évolution des structures et des formes des pièces, l'E-mobilité nécessite souvent la modification des processus de fabrication. En outre, les clients exigent un rendement énergétique, une optimisation des ressources et une rentabilité nettement plus élevés. En d'autres termes, des améliorations significatives de la productivité et de la durabilité. Rösler peut fournir une assistance complète pour de tels projets d'optimisation.
Réduction de la consommation d'énergie grâce à l'utilisation de turbines en lieu et place de systèmes à air comprimé
Les systèmes de grenaillage à air comprimé ont été les principaux outils de grenaillage de précontrainte permettant d'atteindre systématiquement les valeurs de contrainte de compression résiduelle demandées. L'inconvénient de la méthode à air comprimé est qu'elle nécessite beaucoup d'énergie. Aujourd'hui, des améliorations techniques innovantes de la technologie des turbines permettent un grenaillage de précision et de haute qualité d'une large gamme de pièces, à l'aide de turbines à haut rendement énergétique et très productives. Pour de nombreuses applications de grenaillage, il n'est plus nécessaire d'utiliser des systèmes coûteux à air comprimé. Les facteurs les plus importants à prendre en compte dans les opérations de grenaillage sont la forme et la taille de la pièce, les résultats de grenaillage souhaités et le média de grenaillage. Sur la base de ces facteurs, Rösler effectue des simulations numériques du modèle de grenaillage et de l'ensemble du processus. Les simulations sont suivies d'essais de grenaillage réels dans notre Customer Experience Center (CEC). Le CEC étant équipé d'une large gamme de turbines et de systèmes de grenaillage à air comprimé, les essais de grenaillage de précontrainte peuvent être réalisés dans des conditions de production réelles. Grâce à un diffractomètre à rayons X interne, les essais de grenaillage peuvent être rapidement évalués afin de déterminer les paramètres du processus et les moyens de grenaillage qui permettront d'obtenir les résultats souhaités.
Un projet d'optimisation commun entre un grand constructeur automobile européen et Rösler a permis de réaliser des économies d'énergie de 30 % et d'augmenter la capacité de grenaillage de 50 %. Sur la base de ces résultats convaincants, ce même client a acquis entre-temps quatre grenailleuses équipées de turbines.
Moins d'usure des équipements et plus de productivité
Parfois, une révision des paramètres de grenaillage existants peut contribuer à améliorer considérablement l'ensemble du processus de grenaillage. Une fois établis, les paramètres du processus ne sont souvent plus remis en question. Une telle négligence peut entraîner une usure importante de l'équipement et une altération du potentiel d'amélioration du processus.
Des paramètres de processus parfaitement calibrés, y compris la sélection optimale des médias, garantissent des qualités de traitement élevées, une usure moindre de l'équipement et des coûts d'exploitation réduits. Si une révision des paramètres de grenaillage d'une machine existante n'est pas suffisante, une modernisation peut être la bonne solution. Il s'agit notamment de mettre à niveau la machine avec des composants plus productifs, tels que des turbines plus puissantes, ou de développer des montages de pièces pour des pièces nouvelles ou modifiées. L'optimisation du schéma de soufflage doit toujours faire partie des paramètres à prendre en compte.
Dans tous les cas, les essais de grenaillage de précontrainte réalisés dans le CEC, ainsi que le contrôle des résultats par diffraction des rayons X, les tests spéciaux de la surface traitée et, si nécessaire, l'évaluation de la rugosité de la surface et les mesures microscopiques légères, permettront de garantir que les spécifications de grenaillage requises sont respectées. Le choix du bon média de grenaillage est très important pour optimiser les ressources et les coûts du processus. Une analyse du média utilisé permet toujours de déterminer s'il est adapté à l'application concernée.
Grenaillage humide ou sec ?
Le grenaillage de précontrainte à l'aide de buses à air comprimé peut être effectué par voie humide ou sèche. Les avantages de la méthode de grenaillage à sec sont une plus grande intensité de traitement et le ciblage de zones spécifiques. En outre, l'ensemble du processus et les médias de grenaillage peuvent être contrôlés avec précision. La technologie de grenaillage par voie humide empêche le média de s'incruster dans les pièces et permet d'obtenir une rugosité de surface plus faible. Le grenaillage humide étant plus doux que le grenaillage à sec, c'est la méthode idéale pour traiter les pièces délicates à parois minces, sans altérer leur forme initiale. Chacune de ces deux méthodes de grenaillage a ses avantages. Par conséquent, la technologie choisie doit être parfaitement adaptée à l'application concernée, notamment en termes de rentabilité et de qualité des résultats de traitement. Rösler propose un large éventail de types de machines. Cela permet une sélection totalement objective de l'équipement et garantit que les clients obtiennent la meilleure solution possible pour leurs besoins spécifiques.
Toutes les étapes concernant la modification et l'optimisation du processus, y compris les essais de traitement et l'évaluation du processus, peuvent être modifiées afin d'adapter rapidement l'équipement de grenaillage de précontrainte à des conditions de production évolutives. Cela permet d'obtenir des résultats de grenaillage absolument constants et de haute qualité pendant toute la durée de vie de l'équipement. Et cela garantit également que toutes les exigences en matière d'efficacité énergétique, de ressources et de coûts sont pleinement satisfaites.
En créant en 2018 la marque AM Solutions, spécialisée dans le post-traitement des pièces imprimées en 3D, Rösler Oberflächentechnik GmbH a fait preuve d'une remarquable clairvoyance stratégique. David Soldan, Responsable de l’activité AM Solutions, explique : "Ce qui a débuté comme un produit de niche en complément de nos activités "classiques" de traitement de surface s'est transformé en une troisième activité commerciale viable et à croissance rapide, sur un pied d'égalité avec les activités de Tribofinition et de Grenaillage/ Sablage. L'une des raisons de ce succès remarquable est qu'AM Solutions peut profiter des 80 années d'expérience dans le domaine du traitement de surface industriel et des capacités d’expertise de la société mère. L'intégration dans les procédures organisationnelles d'une grande entreprise bien établie a été particulièrement utile à cette jeune start-up dynamique et agile.
Avec l'expansion croissante de la gamme d'équipements et les demandes des clients, il est devenu plus difficile de produire efficacement au sein des unités de fabrication respectives des équipements de Tribofinition et de Grenaillage. C'est pourquoi l'entreprise a décidé de centraliser et spécialiser la production de AM Solutions - 3D post-processing technology. Dès lors qu'il a été décidé de proposer la majorité des machines de post-traitement en tant qu'équipement standard, il est devenu évident que la production des équipements de la marque devait disposer de sa propre "entité". Cela a permis la création d'une zone de développement et de production moderne avec des ateliers d'assemblage dédiées. Dans le cadre de l'intégration verticale, la nouvelle aire de production permet le développement et la mise en œuvre de solutions de post-traitement innovantes et flexibles - depuis les prototypes jusqu'à leur mise en œuvre pratique - le tout auprès d'un seul et même fournisseur !
"Sur environ 1 000 mètres carrés, nous avons mis en œuvre, sur le plan physique et organisationnel, le concept d'une chaîne d'approvisionnement intégrée : La zone de production est complétée par un bureau technique moderne et esthétique avec des cloisons en verre qui comprend un espace de travail et une salle de réunion pour les discussions avec les clients et les réunions internes", commente Stephan Böhnlein, Responsable de la Production des machines et de la supply chain chez Rösler. "Le bureau technique est équipé de tous les outils nécessaires à un environnement de production flexible. Il contient des postes de travail pour l'ingénierie, le développement de logiciels et le prototypage. Cela permet aux ingénieurs de discuter de leurs conceptions avec les équipes d'assemblage sur le site de production et de résoudre rapidement les difficultés techniques."
Les six nouvelles unités d'assemblage ont été conçues en prenant en compte les principes du Lean Management et sont entièrement conformes aux règles des 5S. Cela signifie que les bonnes quantités de matériel sont toujours au bon endroit au moment où elles sont utiles. Les collaborateurs de l'entreprise peuvent se concentrer sur leurs fonctions principales, ne produisent que peu ou pas de gaspillage et réalisent des économies significatives en termes de temps de production. Le contrôle de la production est organisé par le système Kanban, un concept d'approvisionnement en matériel conçu pour un flux de travail continu et des coûts de production optimisés.
Les améliorations apportées à l'ensemble du processus de production sont considérables : Les temps d'assemblage ont été considérablement réduits sans pour autant compromettre la qualité du produit. Dans le même temps, le transport interne dans le processus de production a pu être rationalisé et ses coûts réduits. Une méthode de travail digitalisée, pratiquement sans papier, permet un aperçu rapide de l'état de la production. Il permet à AM Solutions - 3D post processing technology de maintenir un taux de livraison à temps de plus de 92 % et de fournir à ses clients des produits de haute qualité. En outre, la proximité de la cellule de développement des équipements et de la production permet de répondre rapidement et avec souplesse aux demandes des clients.
Il est prévu que, dans un avenir assez proche, jusqu'à 300 machines de post-traitement soient produites par an dans la nouvelle zone de production. L'ensemble de la zone est très flexible et extensible, de sorte que le nombre de machines produites puissent être pratiquement doublé si le marché l'exige.
David Soldan, Responsable de l’activité AM Solutions, est satisfait de la nouvelle organisation de la production : "En faisant passer notre production de machines standards à des volumes plus importants, nous pouvons fournir nos équipements beaucoup plus rapidement à nos clients. Et la proximité physique entre le développement et la production des produits nous permet toujours de répondre rapidement aux demandes spéciales de nos clients. Accepter les exigences d'une petite start-up dans une entreprise bien établie de plus de 80 ans est la preuve d'une flexibilité et d'une ouverture d'esprit remarquables de la part de la Direction de Rösler". M. Soldan conclut : "Dans le cadre de notre nouvelle organisation de production, nous prévoyons de proposer cinq à six machines de post-traitement en fabrication de série".
Affichage de citations motivantes, zones partagées, espace café, règlement d'utilisation des bureaux - des changements majeurs relatifs aux conditions de travail se sont progressivement mis en place au cours des derniers mois au siège du groupe Rösler à Untermerzbach. Les quatre bâtiments dédiés aux bureaux du site ont été entièrement démantelés, rénovés et transformés en espaces modernes et organisés selon les principes du "New Work".
Les premiers collaborateurs ont pris possession des lieux et sont enthousiasmés par leur nouvel environnement de travail nommé "Innowelt" chez Rösler. L'ensemble du projet sera achevé au milieu de l'année prochaine. À cette date, pratiquement tous les bureaux auront été modernisés tant au niveau de leurs équipements, que de leur aspect visuel et de leur ergonomie. Il s'agit d'un projet véritablement novateur pour toute la région. L'un des principaux objectifs était d'intégrer plusieurs départements du site de Bad Staffelstein au siège d'Untermerzbach de manière rentable et durable et d'éviter ainsi la construction de nouveaux bâtiments coûteux.
Dans le "Rösler Innowelt", les postes de travail permanents des différents départements sont remplacés par des zones dites "partagées" qui permettent aux employés de passer d'un poste de travail à l'autre. En raison des règles en vigueur en matière de télétravail, de nombreux collaborateurs ne travaillent plus sur site quotidiennement. À la fin de chaque journée de travail, les employés libèrent complètement leur bureau et placent leurs outils de travail tels que leurs écouteurs, leur ordinateur portable et leurs objets personnels dans des casiers prévus à cet effet.
Chaque étage dispose d'une zone centrale composée d'un salon et d'une cuisine. Les employés peuvent y discuter de projets communs dans une atmosphère détendue. Dans de nombreux petits espaces et salles de conférence, ils peuvent passer des appels téléphoniques en toute confidentialité et se réunir pour discuter. Ces particularités créent une segmentation bienvenue du paysage des bureaux et garantissent que le concept ouvert du "Rösler Innowelt" ne donne pas l'impression d'un open space monotone. Des mesures de réduction du bruit ont également été prises en compte par la Direction et intégrées dans le concept, de manière discrète et innovante. Par exemple, par le biais de plafonds modernes ou par l'utilisation de tissu comme matériau d'absorption acoustique.
Notre Président Directeur Général, Stephan Rösler, tenait à intégrer son nouveau bureau dans l'"Innowelt", à un endroit central. Pendant son absence, le bureau peut être utilisé comme salle de réunion. Les employés ont été associés à la phase d'étude et de mise en œuvre, et toutes les décisions ont été expliquées en détail. Par l'intermédiaire de collègues qui ont volontairement joué le rôle d'interface avec la Direction, chaque employé a pu présenter de manière non formelle ses idées et ses propositions au concept "Innowelt". Une fois par mois, Stephan Rösler est disponible dans la zone "café" pour répondre aux questions et discuter des suggestions des employés concernant "Innowelt".
Stephan Rösler explique : "Nous voulons créer un environnement de travail moderne pour nos collaborateurs, qui procure une impression de bien-être et crée ainsi des conditions travail productives. En même temps, cela rendra l'entreprise plus attrayante pour le personnel. Le projet "Innowelt", qui fait véritablement figure de pionnier, contribuera grandement à la réalisation de ces objectifs. Je tiens d'ores et déjà à remercier tous les employés, les sous-traitants et les fournisseurs pour le soutien qu'ils ont apporté à la mise en œuvre de ce projet. Et je me réjouis de l'atmosphère de travail harmonieuse et fructueuse qui régnera dans les bureaux nouvellement organisés".
Le projet "Innowelt" n'a pas que des effets positifs en interne : La société Rösler Oberflächentechnik GmbH est désormais un client de référence de la société de conseil en gestion ARCHONIC, qui a lancé le projet et contribué à sa mise en œuvre. Le nouveau concept de bureau servira donc de ligne directrice à d'autres entreprises pour la réorganisation de leurs propres bureaux. De plus, la couverture de "Innowelt" dans la presse régionale a déjà convaincu une autre grande entreprise de la région d'entreprendre une telle réorganisation.