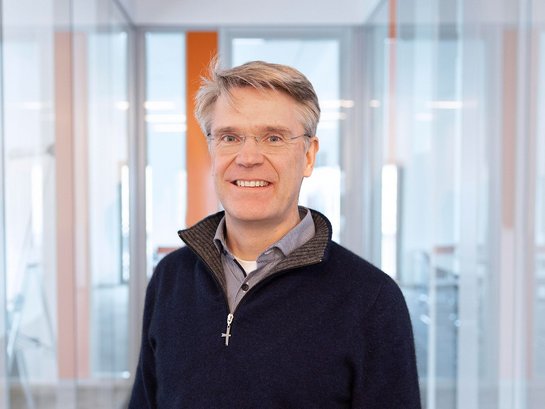
Stabilire nuovi standard con il mindset Rösler
Stabilire nuovi standard con il mindset Rösler
Finitura a specchio per ruote forgiate di alta gamma in meno di 40 minuti
Costi bassi e alte prestazioni per i processi di granigliatura
AM Solutions produrrà attrezzature standard di post-processing AM in volumi più elevati
La nascita di un nuovo concetto di lavoro: "Rösler Innowelt"
Negli anni passati abbiamo dovuto rinunciare a tante certezze. Oggi, ci stiamo confrontando con la ricerca di nuove vie per trovare un futuro stabile. Il percorso per la nuova normalità tecnologica, politica e di business è incerto e difficile, ma per assicurare un successo continuo, dobbiamo affrontare questa sfida a testa alta. Nel tentativo di adattare la nostra attività a un contesto di mercato in rapida evoluzione, possiamo fare affidamento sugli speciali punti di forza di Rösler che hanno reso la nostra azienda così vincente in passato. I nostri punti di forza sono le basi solide per costruire un futuro di successo per la nostra azienda.
Rösler ha molte caratteristiche forti che forniscono una solida base per affrontare qualsiasi nuova sfida. L’azienda produce tecnologie e prodotti che hanno un notevole potenziale di mercato. Inoltre, lo slogan “Finding a better way” è il principio guida che definisce il nostro pensiero. Personalmente ciò significa che anche nei momenti difficili guardiamo avanti e lavoriamo per il futuro. Abbiamo la fortuna di poter contare su prodotti e processi collaudati ma, allo stesso tempo, di poter sviluppare concetti innovativi.
Un buon esempio di combinazione di questi dimostrati e innovativi metodi sono i progetti di sabbiatura delle ruote che abbiamo completato per molti clienti. Una finitura per fini estetici può essere raggiunta con i metodi convenzionali, che possono essere ulteriormente sviluppati con nuove idee per rendere il processo ancora migliore. In questo progetto particolare, il risultato è stato uno speciale e innovativo sistema di finitura a tuffo. Questo approccio è adatto anche in campi di indurimento superficiale dei componenti metallici esposti a carichi elevati. I risultati richiesti si ottengono generalmente con la pallinatura, una tecnologia collaudata e consolidata da tempo.
Abbiamo sviluppato miglioramenti che rendono questa tecnologia ancora migliore, più efficace e più efficiente dal punto di vista dei costi: grazie uno speciale software possiamo simulare elettronicamente il processo di pallinatura su qualsiasi geometria del pezzo. Ciò ci permetterebbe di definire precisamente i parametri di processo già in fase di progettazione in modo da non lasciare nulla al caso.
Stiamo lavorando per approfondire la nostra cultura aziendale: a questo scopo stiamo cercando nuovi metodi di lavoro, implementandoli con il nostro “Rösler Innowelt” – un concetto di ufficio che segue i criteri del New Work con spazi di lavoro aperti e condivisi. Questo rafforzerà la nostra cooperazione e comunicazione interna. Assieme a speciali strumenti digitali e software, ci permetterà di reagire in modo più rapido e flessibile alle richieste dei clienti. Gli stessi strumenti digitali saranno utilizzati anche nella nostra produzione. In questa prima fase abbiamo centralizzato le operazioni di produzione per le attrezzature del nostro marchio AM Solutions - 3D Post Processing Technology. Per soddisfare i requisiti di industrializzazione dell'industria AM, in questo nuovo stabilimento stiamo costruendo apparecchiature standard OEM e di post-processing per la produzione additiva.
Tutto questo non sarebbe stato possibile senza il mindset di Rösler: costruire a partire da prodotti e processi collaudati e migliorarli con idee innovative. Ogni nuovo giorno ci permette di iniziare qualcosa di nuovo e di avventurarci in nuovi settori. Così, possiamo uscire dalla nostra vecchia "normalità" e, con il motto “Find a better way", riuscire a crearne una nuova che garantisca stabilità in tempi di rapidi cambiamenti. Con questo approccio aiutiamo i nostri clienti in tutto il mondo a superare i momenti difficili e ad affrontare con successo le nuove sfide del mercato. E i nostri dipendenti potranno lavorare in un ambiente stabile che permetterà loro di guardare al futuro con fiducia.
Spero che apprezziate la nostra newsletter aziendale. Abbiamo buone ragioni per essere ottimisti
Cordiali saluti
Dr. Till Merkel
Le ruote in alluminio forgiato non si caratterizzano solo per il loro peso ridotto, l'elevata stabilità e le eccellenti caratteristiche di resistenza al carico, ma anche per il loro aspetto esclusivo. Non sorprende quindi che i produttori di auto di lusso utilizzino principalmente ruote in alluminio forgiato nei loro veicoli. I punti di forza estetici delle ruote automobilistiche di alta gamma non sono solo il loro design accattivante, ma anche la loro immacolata lucidatura a specchio. Per ottenere una finitura così perfetta, le ruote devono essere sottoposte a un'operazione di levigatura/pre-lucidatura della superficie prima di poter essere lucidate. Il trattamento delle ruote con i classici metodi di finitura a vibrazione e la finitura con un costoso lavoro manuale richiedono diverse ore di lavorazione. Un produttore leader del settore voleva ridurre significativamente i tempi per la finitura parziale di ruote bicolor già verniciate e cercava una soluzione tecnica adeguata. Questa è stata trovata con la finitrice a tuffo R 1/1 TSA-O/VS-So di Rösler. Questa tecnologia è stata sviluppata da Rösler per la sbavatura, la raggiatura dei bordi, la levigatura/pre-lucidatura di componenti complessi, pesanti e delicati.
Processo a due fasi con supporti e composti appositamente adattati
Una delle operazioni di finitura per le ruote bicolor particolarmente sfidante - la vernice già applicata non deve essere danneggiata, allo stesso tempo le superfici da rifinire devono ricevere una lucidatura brillante e immacolata. Il procedimento funziona nel modo seguente: grazie a un sistema pneumatico di bloccaggio ogni singola ruota da trattare viene fissato al mandrino della macchina di finitura a tuffo. Il sistema di bloccaggio appositamente progettato consente il montaggio manuale e robotizzato delle ruote. Abbassando il mandrino rotante, la ruota viene immersa nella vasca di lavorazione riempita con speciali media di rettifica o lucidatura. Per le operazioni di levigatura/pre-lucidatura viene eseguita con media in plastica dalla forma conica, sviluppati appositamente. In questa fase, il processo è supportato dall'aggiunta continua di acqua e di un adeguato compound. Durante il processo, il mandrino esegue una rotazione centrale e orbitale. I diversi movimenti possono anche essere combinati. Il movimento della ruota che ne deriva garantisce una finitura superficiale omogenea, anche sui dettagli di design più complessi. La ripetibilità e l'uniformità dei risultati ottenuti erano un requisito fondamentale per rendere il processo di finitura a tuffo adatto alla produzione in serie. Questo risultato è stato ottenuto grazie a speciali caratteristiche tecniche, come il motore vibrante collegato alla vasca di lavorazione e un sistema di classificazione dei supporti sottodimensionati integrato. Entrambi assicurano una miscela di media stabile che, a sua volta, garantisce una qualità di finitura costantemente buona.
L’operazione di levigatura, seguita da un quella per di pre-lucidatura , è un ciclo di circa 6 minuti. Per un’elevata brillantatura delle ruote, queste vengono poi inserite in una seconda finitrice a tuffo riempita di media di lucidatura in porcellana. L'operazione di lucidatura richiede un tempo di lavorazione di 25-30 minuti.
Risparmio di risorse nell'uso di acqua e composti
Per la pulizia dell'acqua di processo contaminata è stato installato un sistema di trattamento chimico dell'acqua, progettato specificamente per ridurre al minimo il consumo di acqua e compound. Il sistema viene utilizzato principalmente per pulire l'acqua di processo proveniente dal processo di levigatura/pre-lucidatura. L'acqua di processo, solo leggermente contaminata, proveniente dal processo di lucidatura viene raccolta in un serbatoio e riutilizzata per le fasi successive. I compound necessari per ogni fase del processo vengono rintrodotti automaticamente. Il riutilizzo dell'acqua di processo della fase di lucidatura per la fase di abbassamento di rugosità/levigatura contribuisce a ridurre il consumo complessivo di compound.
Il cliente non è rimasto solo impressionato dalle caratteristiche tecniche ma anche dall’efficienza dei costi della tecnologia delle macchine a tuffo. Non sorprende quindi che abbia già ordinato altre finitrici a tuffo per la prossima fase di espansione della linea di lavorazione delle ruote.
La pallinatura, ossia “il martellamento” dei pezzi, con media di granigliatura precisamente definiti, è una operazione indispensabile nelle industrie dell’automotive e dell’aerospace. Inducendo un incrudimento superficiale sui pezzi, l'operazione di pallinatura migliora sostanzialmente la loro resistenza a lungo termine ai carichi di trazione e flessione. Il processo viene scelto per il trattamento della parte dentata di componenti dello sterzo e della trasmissione, ma anche per molle, alberi motore e di trasmissione e tutti i tipi di pale di turbine. Un vantaggio significativo dell'operazione di pallinatura è che il peso del componente può essere ridotto senza influire sulle sue capacità di carico. Ciò è particolarmente vantaggioso per i veicoli elettrici, perché ne aumenta l'autonomia operativa e ne riduce il consumo energetico. A causa del cambiamento delle strutture e delle forme dei pezzi, la mobilità elettrica richiede spesso la modifica dei processi di produzione. Inoltre, i clienti chiedono un'efficienza energetica, delle risorse e dei costi nettamente superiore. In altre parole, miglioramenti significativi in termini di produttività e sostenibilità. Rösler è in grado di fornire un supporto completo per questi progetti di ottimizzazione.
Abbassamento dei consumi di energia grazie alle turbine al posto dei sistemi di aria compressa
I sistemi di granigliatura ad aria compressa sono sempre stati i sistemi di pallinatura pre-dominanti per ottenere valori di tensione residua costanti. Tuttavia, un aspetto negativo di questo metodo è che richiede molta energia. Oggi, i miglioramenti delle tecnologie delle turbine consentono una pallinatura di precisione in alte qualità e di un grande numero di componenti, con una buona efficienza dei costi. Per molte applicazioni di pallinatura non sono più necessari costosi sistemi di granigliatura ad aria compressa. I fattori più importanti da considerare nelle operazioni di pallinatura, sono la forma e le dimensioni del pezzo, i risultati attesi e il tipo di graniglia. Sulla base di questi fattori, Rösler esegue simulazioni al computer del modello di sabbiatura e dell'intero processo. Successivamente, avranno luogo ulteriori prove effettive di pallinatura eseguite nel nostro Customer Experience Center (CEC). Poiché il CEC è dotato di un'ampia gamma di sistemi di granigliatura a turbina e ad aria compressa, le prove possono essere condotte in condizioni di produzione reali. Grazie a un diffrattometro a raggi X interno, le prove di pallinatura possono essere valutate rapidamente, determinando quali parametri di processo e quali graniglie porteranno i risultati richiesti.
Un progetto di ottimizzazione congiunto tra un'importante casa automobilistica europea e Rösler ha portato a un risparmio energetico del 30% e a un aumento del 50% dell’efficacia di granigliatura. Sulla base dei convincenti risultati del progetto, il cliente ha acquistato quattro pallinatrici dotate di turbine.
Minore usura delle turbine e maggiore produttività
A volte una revisione dei parametri di granigliatura esistenti può contribuire a migliorare significativamente l'intero processo di pallinatura. Una volta stabiliti, i parametri di processo spesso non vengono più messi in discussione. Questa negligenza può portare a un'elevata usura delle attrezzature e a un potenziale di miglioramento del processo non adeguatamente sfruttato.
Parametri di processo perfettamente calibrati, compresa la selezione ottimale dei materiali, garantiscono un'elevata qualità di pallinatura, una minore usura delle apparecchiature e bassi costi operativi. Se la revisione dei parametri di granigliatura di una macchina esistente non è sufficiente, la soluzione giusta può essere un retrofit. Ciò include, tra l'altro, l'aggiornamento della macchina con componenti più produttivi, come turbine più potenti o lo sviluppo di attrezzature per pezzi nuovi o modificati. L'ottimizzazione del modello di granigliatura deve sempre far parte delle considerazioni.
In tutti i casi, le prove di pallinatura nel CEC, insieme alla valutazione dei risultati mediante diffrazione di raggi X e alle prove speciali di copertura della pallinatura e, se necessario, alla rugosità della superficie e alle misurazioni mediante microscopio ottico, garantiranno il raggiungimento delle specifiche di pallinatura richieste. Molto importante per l'efficienza delle risorse e dei costi è la selezione del giusto media di granigliatura. Un'analisi della graniglia aiuterà sempre a determinare se quest’ultima sia adatta.
Pallinatura a secco o a umido?
La pallinatura ad aria compressa può essere eseguita come processo a umido o a secco. I vantaggi del metodo di pallinatura a secco sono una maggiore intensità di granigliatura e la possibilità di sabbiare in modo mirato aree superficiali specifiche. Inoltre, l'intero processo e i media di granigliatura possono essere controllati con precisione. La tecnologia di sabbiatura a umido, invece, impedisce alla graniglia di incastrarsi nei pezzi, producendo una minore rugosità superficiale. Poiché la granigliatura a umido è più delicata di quella a secco, è il metodo ideale per trattare pezzi delicati con pareti sottili senza deformarli. Entrambi i metodi di pallinatura presentano dei vantaggi. Tuttavia, il metodo scelto deve essere perfettamente adatto alla rispettiva applicazione, soprattutto per quanto riguarda l'efficienza dei costi e la qualità dei risultati della pallinatura. Rösler offre un'ampia gamma di diversi tipi di macchine. Ciò consente una selezione totalmente obiettiva delle apparecchiature, garantendo ai clienti la migliore soluzione possibile per le loro specifiche esigenze.
Tutte le fasi di modifica e ottimizzazione del processo, comprese le prove di lavorazione e la valutazione del processo, possono essere modificate in modo che l'apparecchiatura di pallinatura possa essere rapidamente adattata alle mutevoli condizioni di produzione. Questo assicura risultati di pallinatura assolutamente costanti e di alta qualità per tutta la durata di vita dell'apparecchiatura. Inoltre, garantisce che tutti i requisiti di efficienza energetica, delle risorse e dei costi siano pienamente soddisfatti.
Dalla creazione nel 2018 del brand AM Solutions come specialista del post-processing di componenti stampati in 3D, Rösler Oberflächentechnik GmbH ha dimostrata notevole lungimiranza strategica. David Soldan, responsabile di AM Solutions ha detto “Quello che era iniziato come un prodotto ausiliario di nicchia all'interno delle nostre "normali" attività di raffinazione delle superfici, è cresciuto rapidamente, diventando una terza sezione aziendale redditizia, alla pari con le divisioni di finitura in massa e granigliatura. Uno dei motivi di questo notevole successo è che AM Solutions può avvalersi di 80 anni di esperienza nel campo del trattamento industriale delle superfici e delle capacità di risoluzione dei problemi della casa madre. Particolarmente utile per questa start-operation dinamica e agile è la sua integrazione nelle procedure organizzative di una grande azienda consolidata".
Con la veloce crescita della linea produttiva e delle richieste dei clienti è diventato sempre più difficile produrre in modo efficiente le tecnologie di post-processing negli impianti di produzione per la finitura di massa e la granigliatura. Per questo motivo l‘azienda ha deciso di centralizzare la produzione di AM Solution - 3D post-processing technology. Una volta presa la decisione di offrire la maggior parte delle macchine di post-processing come equipaggiamento standard collaudato, è diventato ovvio che la produzione di AM Solutions - 3D post-processing technology avere una propria "casa". Ciò ha permesso la creazione di una moderna area di sviluppo e produzione con sezioni di assemblaggio dedicate. Nell'ambito dell'integrazione verticale, la nuova area di produzione consente lo sviluppo e l'implementazione di soluzioni di post-processing innovative e flessibili, dalla progettazione alla realizzazione pratica, il tutto da un unico fornitore!
"Su circa 1.000 mq2 abbiamo implementato fisicamente e organizzativamente il concetto di catena di fornitura integrata. L'area di produzione è completata da un centro di controllo moderno ed esteticamente gradevole, con pareti in vetro, che comprende un'area di co-working e una sala conferenze per i colloqui con i clienti e le riunioni interne", commenta Stephan Böhnlein, responsabile della produzione di attrezzature e della gestione della catena di fornitura di Rösler. "Il centro di controllo è dotato di tutti gli strumenti tecnici necessari per un ambiente di produzione flessibile. Contiene postazioni di lavoro per l'ingegneria, lo sviluppo del software e la prototipazione. Ciò consente agli ingegneri di discutere i loro progetti con i team di assemblaggio presso il sito di produzione, così da poter risolvere rapidamente i problemi tecnici".
Le sei nuove stazioni di assemblaggio sono state progettate tenendo conto dei principi della gestione snella e sono pienamente conformi alle regole 5S. Ciò significa che le giuste quantità di materiale sono sempre al posto giusto quando è necessario. I dipendenti possono concentrarsi sulle loro funzioni principali, producendo pochi o nessuno spreco, ottenendo un significativo risparmio di tempo di produzione. Il controllo della produzione è organizzato attraverso il sistema Kanban, un concetto di approvvigionamento dei materiali progettato per un flusso di lavoro continuo e per ottimizzare i costi di produzione.
I miglioramenti dell'intero processo produttivo sono sostanziali: i tempi di assemblaggio sono stati notevolmente ridotti senza compromettere la qualità del prodotto. Allo stesso tempo, è stato possibile snellire i trasporti interni, riducendone i costi. Un sistema di lavoro elettronico, praticamente privo di carta, fornisce una rapida panoramica dello stato di produzione. Ciò consente ad AM Solutions – 3D post-processing Technology di mantenere un tasso di consegna puntuale di oltre il 92% e di fornire ai propri clienti prodotti di alta qualità. Inoltre, la vicinanza tra lo sviluppo delle attrezzature e la produzione consente di rispondere in modo rapido e flessibile alle richieste dei clienti.
Si prevede che, in un futuro non troppo lontano, nella nuova area di produzione verranno prodotte fino a 300 macchine di post-processing all'anno. L'intero concetto di posto di lavoro è altamente flessibile, in modo che il numero di macchine prodotte possa essere praticamente raddoppiato, se il mercato lo richiede.
David Soldan, responsabile di AM Solutions, è soddisfatto del nuovo sistema di produzione: "Passando dalla produzione di macchine standard a volumi più elevati, possiamo fornire le nostre attrezzature ai nostri clienti molto più velocemente. Tuttavia, la vicinanza fisica tra lo sviluppo del prodotto e la produzione, ci permette di soddisfare rapidamente le richieste speciali dei clienti. Accettare le esigenze di una piccola start-up in un'azienda consolidata che ha più di 80 anni è la prova di una notevole flessibilità e apertura da parte del top management di Rösler". Soldan conclude: "Nell'ambito del nostro nuovo sistema di produzione prevediamo di offrire cinque o sei macchine di post-trattamento come prodotti standard".
Condivisione dei preventivi, aree di ancoraggio, work cofè, politica delle scrivanie pulite: negli ultimi mesi, presso la sede principale del gruppo Rösler a Untermerzbach, si è verificato un importante cambiamento del sistema d'ufficio. Quattro interi edifici di uffici sono stati completamente spogliati, rinnovati e modificati in moderni uffici secondo i principi del “New Work”.
I primi colleghi sono già stati trasferiti di recente nelle loro nuove aree di lavoro organizzate e sono entusiasti del nuovo ambiente di lavoro che in Rösler chiamiamo “Innowelt”. L’intero progetto sarà completato entro metà dell’anno. A quel punto, praticamente tutti gli uffici saranno stati modernizzati per quanto riguarda le attrezzature, l'estetica e l'ergonomia. Si tratta di una vera e propria tendenza per l'intera regione. Uno dei nostri obiettivi principali era di riuscire a integrare alcuni dipartimenti della locations di Bad Steffelstein in quella di Untermerzbach in modo efficiente e sostenibile, evitando costose nuove costruzioni.
Grazie a “Rösler Innowelt” le postazioni di lavoro permanenti in vari dipartimenti sono sostituite da aree così dette di “ancoraggio” che permettono ai dipendenti di spostarsi da una postazione all’altra. Infatti, a causa delle regole prevalenti sull'home office, molti colleghi non lavorano più in azienda tutti i giorni. Alla fine di ogni giornata di lavoro, i colleghi liberano completamente la loro scrivania e ripongono i loro strumenti d'ufficio, come cuffie, computer portatili e oggetti personali, in appositi armadietti.
Nella locations centrale, ciascun piano ospita il così detto “caffè di lavoro” che consiste in un salotto e un angolo cottura. Qui i dipendenti possono discutere assieme i progetti in un’atmosfera rilassante. In numerosi e piccoli compartimenti e conference room, i colleghi possono avere meeting o telefonate confidenziali. Questi elementi creano una piacevole segmentazione degli uffici e assicurano che il concetto aperto del "Rösler Innowelt" non crei l'impressione di un monotono ufficio open space. Sono state prese anche delle misure di riduzione del rumore in considerazione dalla direzione e integrate nell’ambiente di lavoro in modo discreto e innovativo. Ad esempio con i moderni pannelli per controsoffitti o l'uso del tessuto come materiale fonoassorbente.
Il nostro amministratore delegato, Stephan Rösler, desiderava integrare il suo nuovo ufficio nell'"Innowelt" in una posizione centrale. Durante la sua assenza l'ufficio può essere utilizzato come sala riunioni. I dipendenti sono stati coinvolti nella fase di pianificazione e implementazione e tutte le decisioni sono state spiegate nel dettaglio. Attraverso i colleghi che fungevano volontariamente da interfaccia con la direzione, ogni dipendente poteva presentare in modo non burocratico le proprie idee e proposte relative al concetto "Innowelt". Una volta al mese Stephan Rösler è a disposizione nel cosiddetto “change café” per rispondere alle domande e discutere i suggerimenti dei dipendenti su "Innowelt".
Stephan Rösler spiega “Vogliamo creare un moderno ambiente di lavoro per i nostri dipendenti che trasmetta una buona impressione e, quindi, che generi le condizioni per un ambiente di lavoro produttivo. Allo stesso tempo, ciò renderebbe l’azienda più attraente per dipendenti qualificati. Il progetto veramente pionieristico "Innowelt" sarà un fattore sostanziale per raggiungere questi obiettivi. Già ora voglio ringraziare tutti i dipendenti, i subappaltatori e i fornitori per il loro supporto nella realizzazione del progetto. Mi auguro un’armoniosa atmosfera lavorativa di successo nei nuovi uffici di ultima generazione”.
Nel progetto “Innowelt” non ha solo degli effetti positivi internamente. La Rösler Oberflächentechnik GmbH è oggi un cliente di riferimento della società di consulenza aziendale ARCHONIC che ha iniziato il progetto e ha assistito all’implementazione. Pertanto, il nuovo concetto di ufficio fornirà le linee guida per tutte quelle aziende che vogliono riorganizzare i loro spazi lavorativi. D’altronde, la diffusione di "Innowelt" sulla stampa regionale ha già convinto un'altra grande azienda della regione a intraprendere una tale riorganizzazione.