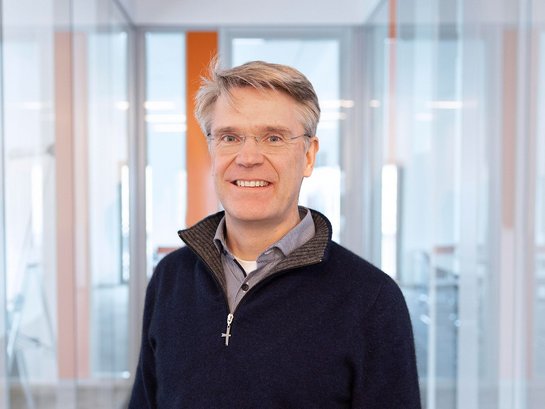
Mit dem Rösler Mindset in eine neue Normalität
Mit dem Rösler Mindset in eine neue Normalität
Spiegelglanz für hochwertige Schmiederäder in weniger als 40 Minuten
Kosten reduzieren und Produktivität erhöhen beim Kugelstrahlen
AM Solutions bringt AM-Post Processing Anlagen in Serie
Start des New Work-Konzeptes "Rösler Innowelt"
In den letzten Jahren mussten wir uns von vielen vermeintlichen Gewissheiten verabschieden – und suchen nun nach Orientierung und Stabilität. Der Weg zur „neuen Normalität“ in Wirtschaft, Technik und Politik erscheint ungewiss, aber wir müssen ihn gehen. Deswegen haben wir bei Rösler einfach mal gesucht, was Bestand hat und so verlässlich ist, dass wir daraus Zuversicht schöpfen können.
Und wir haben bei uns im Unternehmen vieles gefunden, das uns Orientierung bringt: Wir haben Technologien und Produkte, die sich über Jahre bewährt haben und auf die wir aufbauen können. Wir haben Stärken, die das Unternehmen auszeichnen und mit „finding a better way...“ haben wir einen Leitsatz, der unser Mindset beschreibt. Für mich bedeutet das konkret, dass wir auch in schwierigen Zeiten nach vorne schauen, kontinuierlich nach vorne arbeiten und zwar weiterhin auf Bewährtes setzen – aber das Bewährte mit Neuem und Innovativem kombinieren.
Ein gutes Beispiel dafür ist ein Projekt, welches wir für einen großen Kunden im Bereich Felgenbearbeitung realisiert haben. Man kann die ästhetischen Ergebnisse, welche in der Branche gefragt sind, mit bewährten Methoden erreichen – oder man kombiniert diese mit etwas Neuem und kommt dann zu einer speziellen Tauchschleifanlage. Dieser Denkansatz funktioniert auch bei der Oberflächenaufhärtung von Bauteilen. Wir erreichen diese über das Shot Peening oder Kugelstrahlen – eine Technik, die wir schon lange sehr erfolgreich im Markt etabliert haben. Jetzt haben wir das Verfahren aber noch besser, effektiver und ressourcensparender gemacht: Durch den Einsatz von Simulationstechnik, mithilfe derer sich die Bauteilgeometrie im Strahlprozess nachbilden lässt, sind wir in der Lage, die Prozessparameter bereits in der Konstruktionsphase sehr exakt zu bestimmen und müssen nichts dem Zufall überlassen.
Kontinuierlich nach vorne arbeiten wollen wir auch im Bereich Unternehmenskultur: Wir setzen auf neue Arbeitsformen und füllen diese in unserer „Rösler Innowelt“ mit Leben – einem Bürokonzept im Sinne von New Work und open/shared workspace. Damit stärken wir die interne Zusammenarbeit und können schneller, flexibler und agiler auf Kundenanforderungen reagieren – auch dank digitaler Werkzeuge und Kollaborationssoftware. Deren Einsatz bleibt natürlich nicht auf unsere Büros beschränkt, sondern hat durch die Zentralisierung der Produktion unserer Marke AM Solutions – 3D post processing technology auch Einzug in unsere Fertigung gehalten. Um dem Wandel in der Branche in Richtung Industrialisierung Rechnung zu tragen, beginnen wir dort mit der Serienproduktion von OEM-Maschinen und Post Processing Anlagen für die additive Fertigung.
All das wäre nicht denkbar ohne unser Rösler-Mindset: Bewährtes weiterdenken, mit Innovativem kombinieren, um auf diese Art und Weise jeden Tag ein bisschen Neues, jeden Tag ein bisschen Aufbruch zu wagen und damit aus dem alten Normal „finding a better way“ auch unser neues Normal zu machen, das auch in Zeiten des Wandels Gültigkeit hat. Damit schaffen wir für unsere Kunden rund um den Globus beste Voraussetzungen, um in den schwierigen Zeiten zu bestehen – und wir geben unseren Mitarbeitern die nötige Sicherheit, um die Herausforderungen der Gegenwart zuversichtlich anzunehmen.
Ich wünsche Ihnen eine anregende Lektüre unseres neuen Unternehmensnewsletters. Bleiben Sie zuversichtlich!
Ihr Dr. Till Merkel
Einerseits ist es ein geringes Gewicht bei gleichzeitig hoher Stabilität und Belastbarkeit, andererseits die exklusive Optik, weshalb insbesondere OEM aus dem Premiumsegment ihre Fahrzeuge auf geschmiedeten Aluminiumrädern über die Straßen rollen lassen. Zu den optischen Merkmalen der Felgen zählt nicht nur ein ansprechendes Design, sondern erst eine makellose Hochglanz-Politur sorgt für einen perfekten Gesamteindruck. Dafür werden diese üblicherweise vor- und feingeschliffen sowie poliert. Erfolgen diese Prozesse in klassischer Vibrations-Gleitschlifftechnik oder gar in „unbezahlbarer“ Handarbeit, sind dafür Bearbeitungszeiten von mehreren Stunden erforderlich. Diesen enormen Zeitaufwand wollte ein renommierter Felgenhersteller auch bei der partiellen Bearbeitung bereits lackierter Bicolor-Felgen deutlich verringern und suchte eine Bearbeitungsalternative. Fündig wurde das Unternehmen mit der Tauchschleifanlage R 1/1 TSA-O/VS-So. Tauchschleifen wurde von Rösler für das reproduzierbare und schnelle Entgraten, Kantenverrunden, Schleifen und Polieren von komplex geformten, schweren und empfindlichen Werkstücken entwickelt.
Zweistufiger Prozess mit abgestimmten Verfahrensmitteln
Besonders herausfordernd bei dieser Aufgabenstellung war die Prozessgestaltung – einerseits darf die Lackierung nicht beschädigt werden, andererseits muss auf den zu bearbeitenden Flächen ein brillanter Hochglanz erzielt werden. Die Felgen werden dafür mithilfe eines pneumatischen Spannsystems an der Arbeitsspindel der Tauchschleifanlage befestigt. Das Befestigungssystem wurde so ausgelegt, dass die Beladung sowohl manuell als auch automatisiert mit einem Roboter erfolgen kann. Die rotierende Spindel taucht das Rad in einen feststehenden Arbeitsbehälter ein. Das Vorschleifen erfolgt mit speziell von Rösler für diese Anwendung entwickelten und gefertigten, kegelförmigen Kunststoffschleifkörpern sowie einem abgestimmten Compound in einem Nassprozess. Während der Bearbeitung führt die Spindel zentrische, orbitale und reziproke Drehbewegungen durch, die auch kombiniert werden. Durch diese Bewegungsabläufe ist sichergestellt, dass selbst in feinsten Details der Räder reproduzierbar ein homogenes Schleifergebnis erzielt wird. Gerade die Reproduzierbarkeit der Oberflächenergebnisse ist eine zentrale Anforderung an einen großserientauglichen Prozess. Einen wesentlichen Beitrag dazu leisten auch der Vibrationsmotor am Arbeitsbehälter und die integrierte Unterkornaussiebung. Beides sorgt dafür, dass mit einem Schleifkörpergemisch in konstant guter Qualität gearbeitet wird.
Nach einer Feinschleifbearbeitungszeit von rund sieben Minuten werden die Räder für das Hochglanz-Polieren in eine zweite Tauchschleifanlage umgesetzt, die mit einem Porzellanmedium befüllt ist. Die Bearbeitungszeit bei diesem Prozess liegt bei 25 bis 30 Minuten.
Ressourcenschonender Einsatz von Wasser und Compound
Für einen wasser- und compoundsparenden Betrieb der Anlagen wurde eine chemische Wasseraufbereitungsanlage integriert. Sie wird für die Aufbereitung der nur gering verunreinigten Flüssigkeit aus dem Feinschleif- und Polierprozess eingesetzt. Das vom Polierprozess anfallende und zwischengepufferte Prozesswasser wird für den Vorschleifprozess nochmals genutzt. Der für die Prozesse benötigte Compound wird bedarfsgerecht jedem Prozessschritt automatisch zudosiert und kann dadurch auch beim Vorschleifen ein zweites Mal genutzt werden.
Überzeugt ist das Unternehmen sowohl von der Technik als auch der Wirtschaftlichkeit der Tauchschleifanlagen. Dies wird nicht zuletzt daran deutlich, dass für die nächste Ausbaustufe der Felgenbearbeitung bereits weitere Anlagen bestellt wurden.
Shot Peening, auch Verfestigungs- oder Kugelstrahlen genannt, ist in Branchen wie der Fahrzeugindustrie sowie Luft- und Raumfahrt ein unverzichtbares Verfahren. Es wird eingesetzt, um Druckeigenspannungen in das Bauteil einzubringen und damit die Dauerfestigkeit des Materials deutlich zu erhöhen. Es kommt beispielsweise bei Verzahnungs-, Lenkungs- und Getriebeteilen, Federn, Antriebs- und Kurbelwellen sowie Turbinenschaufeln zum Einsatz. Ein weiterer Vorteil ist, dass durch das Shot Peening das Bauteilgewicht bei gleicher mechanischer Belastbarkeit verringert werden kann, was insbesondere in der E-Mobilität eine größere Reichweite durch geringeren Stromverbrauch ermöglicht. In diesem Bereich erfordern veränderte Bauteilstrukturen und -geometrien häufig eine Anpassung des Prozesses. Hinzu kommen deutlich höhere Anforderungen an die Energie-, Ressourcen- und Kosteneffizienz und somit um die Steigerung der Produktivität. Bei der Umsetzung der notwendigen Maßnahmen unterstützt Rösler umfassend.
Energieverbrauch verringern durch Turbinen statt Druckluftdüsen
Um vorgegebene Druckeigenspannungswerte prozesssicher zu erreichen, erfolgt das Verdichtungsstrahlen klassischerweise mit Druckluft-Strahlanlagen, die einen hohen Energieeinsatz erfordern. Durch gezielte Weiterentwicklung bei Strahlturbinen lassen sich zahlreiche Anwendungen, für die bisher Druckluftdüsen erforderlich waren, inzwischen mit energiesparenden und effizienten Strahlturbinen reproduzierbar umsetzen. Wesentliche Kriterien dabei sind die Bauteildimensionen, die geforderten Oberflächeneigenschaften und das Strahlmittel. Auf Basis dieser Informationen führt Rösler sowohl Strahlbild- und Prozesssimulationen als auch reale Strahlversuche in seinen Customer Experience Center (CEC) durch. Da hier praktisch alle Anlagentypen für das Turbinen- und Druckluftstrahlen zur Verfügung stehen, erfolgen die Versuche unter produktionsnahen Bedingungen. Dabei wird basierend auf röntgendiffraktometrischen Auswertungen ermittelt, ob und mit welchen Strahlparametern sowie welchem Strahlmittel das geforderte Ergebnis erzielbar ist.
Durch eine gemeinsame Prozessoptimierung bei einem großen europäischen Automobilhersteller konnte bereits eine Energieeinsparung von 30 % und eine Steigerung der Strahlkapazität um 50 % erzielt werden. Aufgrund der positiven Erfahrung und der überzeugenden Ergebnisse sind bei diesem Kunden inzwischen vier mit Turbinen bestückte Shot Peening-Anlagen in Betrieb.
Geringerer Anlagenverschleiß und höhere Produktivität
Optimierungspotenzial steckt häufig auch in der Überprüfung der verwendeten Strahlparameter. Denn einmal ermittelt, werden diese im täglichen Betrieb meist nicht mehr hinterfragt – hoher Anlagenverschleiß und nicht genutztes Produktionspotenzial sind häufig die Folge.
Perfekt eingestellte Prozessparameter, inklusive der Auswahl des optimalen Strahlmittels, gewährleisten hohe Bauteilqualität, geringen Anlagenverschleiß und somit niedrigere Betriebskosten der Strahlanlage. Reichen diese Maßnahmen bei vorhandener Technik nicht aus, kann ein Retrofit die richtige Lösung sein. Dies beinhaltet unter anderem die Aufrüstung der Anlage mit leistungsfähigeren Komponenten, beispielsweise stärkeren Turbinen, ebenso wie die Konstruktion von Werkstückaufnahmen für neue beziehungsweise veränderte Bauteile, inklusive einer Anpassung des Strahlbilds.
In allen Fällen sorgen Versuche im CEC sowie Ergebnisanalysen mittels Röntgendiffraktometrie, Überdeckungstests und bei Bedarf Messungen der Oberflächenrauheit sowie lichtmikroskopische Untersuchungen dafür, dass das geforderte Strahlergebnis sichergestellt werden kann. Ganz generell spielt das eingesetzte Strahlmittel eine wichtige Rolle für die Ressourceneffizienz und Wirtschaftlichkeit des Prozesses. Ob es für die jeweilige Anwendung optimal ist, lässt sich durch eine Strahlmittelanalyse feststellen.
Nass- oder trocken Kugelstrahlen
Das Verdichtungsstrahlen mit Druckluftdüsen kann in einem Nass- oder Trockenprozess erfolgen. Für das trockene Strahlen spricht unter anderem, dass höhere Strahlintensitäten möglich sind, ebenso lassen sich Teilbereiche an Werkstücken gezielt bearbeiten. Darüber hinaus können sowohl der Prozess als auch das Strahlmittel sehr genau überwacht werden. Zu den Vorteilen des Nassstrahlens zählen geringere Strahlmitteleinschlüsse sowie eine niedrigere Oberflächenrauheit. Der „sanftere“ Prozess ermöglicht außerdem die Bearbeitung von sehr dünnen Werkstücken. Es gibt also gute Gründe für jedes dieser Verfahren, aber insbesondere aus Wirtschaftlichkeits- und Qualitätsgesichtspunkten muss die Technologie zur jeweiligen Aufgabenstellung passen. Da Rösler ein breites Spektrum an verschiedenen Anlagentypen und –verfahren hat, ist eine objektive Auswahl der am besten geeigneten Technologie gewährleistet.
Die verschiedenen Maßnahmen zur Prozessanpassung und -optimierung einschließlich der Versuchs- und Analysemöglichkeiten sind so ausgelegt, dass Shot Peening-Anlagen auch unter veränderten Produktionsbedingungen über ihren gesamten Lebenszyklus prozesssicher betrieben werden können. Dabei werden auch die aktuellen Anforderungen an Energie- und Ressourceneffizienz sowie Wirtschaftlichkeit erfüllt.
Mit der Gründung der Marke AM Solutions als Spezialist für die Nachbearbeitung von additiv gefertigten Werkstücken bewies die Rösler Oberflächentechnik GmbH im Jahr 2018 strategischen Weitblick: „Was vor fünf Jahren als Nischen- und Nebenprodukt der „normalen“ Oberflächenbearbeitung begonnen hat, ist heute zu einem selbstbewussten, dritten Standbein neben der Strahl- und Gleitschlifftechnik geworden und profitiert gleichermaßen von den rund 80 Jahren Erfahrung in der industriellen Oberflächenbearbeitung sowie den Strukturen der Mutter. Besonders spannend, aber auch hilfreich für das junge, dynamische und agile Start-Up ist die Einbettung innerhalb der gefestigten Strukturen eines großen und soliden Unternehmens“, so David Soldan, Head of AM Solutions.
Mit der wachsenden Zahl der Produkte und Anforderungen wuchs auch der Wunsch nach einer Zentralisierung der AM Solutions – 3D post processing technology-Produktion, die vorher in Gleitschliff- und Strahlanlagen aufgeteilt und an den jeweiligen Produktionsstandorten mit angedockt war.
Spätestens mit der Entscheidung, einen Großteil der Anlagen als standardisierte und praxiserprobte Serienprodukte anzubieten war klar, dass die Produktion von AM Solutions – 3D post processing technology eine eigene „Heimat“ bekommen muss. Die Idee eines hochmodernen Entwicklungs- und Produktionsbereiches mit identischen, produktspezifischen Montageplätzen war geboren. Dem Gedanken der vertikalen Integration entsprechend entstehen dort flexible und wendige Lösungen von der Idee bis zur Umsetzung aus einer Hand.
„Auf rund 1.000 Quadratmetern haben wir den Gedanken der integrierten Lieferkette baulich und gestalterisch umgesetzt: Der Fertigung vorangestellt ist ein gläserner Leitstand in modernem und ästhetischem Design mit Co-Working-Area und einem Meetingraum für Kundengespräche und interne Besprechungen“, so Stephan Böhnlein, Bereichsleiter Maschinenbau und Supply Chain Management bei Rösler. „Technisch ist der Leitstand mit sämtlichem Zubehör für ein möglichst agiles Arbeiten ausgestattet. Er bietet Arbeitsplätze für Engineering, Software und Prototyping. Damit können die Ingenieure ihre Entwicklungen direkt mit den Montageteams vor Ort besprechen und gemeinsam an Lösungen arbeiten.“
Die sechs neuen Produktionsplätze sind nach den Prinzipien des Lean-Management und unter besonderer Berücksichtigung der 5S-Regeln ausgestattet. Das heißt, das Material ist immer in der richtigen Menge am richtigen Ort zur richtigen Zeit verfügbar, sodass sich die Mitarbeiter auf ihre Haupttätigkeiten fokussieren können, wenig bis keine Verschwendung im Prozess haben und deutlich Zeit sparen. Die Produktionsprozesssteuerung erfolgt über das Kanban-System, ein Materialversorgungskonzept, welches auf einen möglichst kontinuierlichen Workflow bei optimierten Produktionskosten ausgelegt ist.
Die Verbesserungen im Produktionsprozess sind enorm: Die Durchlaufzeiten konnten deutlich reduziert werden – bei gleichbleibend hoher Produktqualität. Gleichzeitig konnten Logistikaufwände im Produktionsprozess reduziert und Kosten eingespart werden. Durch ein weitestgehend papierloses und transparentes Arbeiten mit einem direkten Überblick über die Terminsituation am Produktionsplatz kann AM Solutions – 3D post processing technology die Liefertreue für seine Kunden mit einem Erfüllungsgrad von mehr als 92 % extrem hochhalten und Produkte in sehr hohem Qualitätsstandard liefern. Gleichzeitig erlaubt die Einheit von Entwicklung und Produktion an einem Standort auch weiterhin ein flexibles und direktes Reagieren auf Kundenwünsche.
Mittelfristig sollen in dem neuen Produktionsbereich bis zu 300 Post Processing-Anlagen pro Jahr produziert werden. Dabei ist das Arbeitsplatzkonzept aber flexibel ausgelegt, sodass die Anzahl der produzierten Anlagen je nach Marktbedarf theoretisch auch verdoppelt werden kann.
„Durch die Umstellung unseres Produktionssystems hin zur Serienproduktion können wir unsere Anlagen viel schneller an den Kunden bringen. Gleichzeitig erlaubt uns die Verschmelzung von Entwicklung und Produktion vor Ort weiterhin ein agiles und flexibles Reagieren auf Kundenwünsche. Es zeugt schon von einer bemerkenswerten Flexibilität und Offenheit der Geschäftsführung in einem über 80 Jahre alten und klar strukturierten Unternehmen die Anforderungen eines kleinen Start-Up´s zuzulassen und zu fördern“, freut sich David Soldan, Head of AM Solutions über die Entwicklung. „Unser Ziel ist es nun, künftig innerhalb unserer neuen Produktionsstrukturen fünf bis sechs unserer Anlagen als Serienprodukte anzubieten.“
Sharing-Quote, Ankerbereich, Work-Café, Clean-Desk-Policy – von außen weitestgehend unbemerkt hat sich in den letzten Monaten viel getan am Hauptstandort der Rösler-Gruppe in Untermerzbach. Dort wurden und werden insgesamt vier Bürogebäude komplett entkernt, saniert und zu modernen Bürolandschaften umgebaut, in denen nach den Prinzipien des New Work gearbeitet wird.
Die ersten Mitarbeiter haben die neu gestalteten Büroräume bereits bezogen und sind begeistert von der neuen Arbeitswelt, die bei Rösler „Innowelt“ heißt. Abgeschlossen wird die Maßnahme voraussichtlich Mitte kommendes Jahr. Dann sind so gut wie alle Büroarbeitsplätze in Punkto Ausstattung, Attraktivität und Ergonomie auf dem neusten Stand und sicherlich einzigartig in der Region. Gleichzeitig schaffen wir es so, mehrere Abteilungen vom Standort Bad Staffelstein in Untermerzbach wirtschaftlich und nachhaltig zu integrieren, dabei aber ressourcenraubende Neubauten zu vermeiden.
Feste Arbeitsplätze weichen in der „Rösler Innowelt“ Ankerbereichen für die einzelnen Abteilungen, innerhalb derer die Mitarbeiter freie Platzwahl haben. Aufgrund der geltenden Homeoffice-Regelung befinden sich die Kollegen ohnedies nicht mehr jeden Tag im Büro. Am Ende jedes Arbeitstages räumen die Mitarbeiter ihren Schreibtisch komplett leer und verstauen ihre Arbeitsmaterialien, wie zum Beispiel Headset, Laptop sowie persönliche Gegenstände, sicher in personalisierten Lockern.
Auf jeder Etage befindet sich in zentraler Lage ein sogenanntes Work Café, bestehend aus einer Lounge und einem Küchenbereich, wo sich die Mitarbeiter ungezwungen über gemeinsame Projekte austauschen können. Zahlreiche Sitznischen und Besprechungsräume dienen als Rückzugsmöglichkeiten für vertrauliche Gespräche oder längere Telefonate. Durch diese baulichen Elemente, die für eine geschickte Unterbrechung der Bürolandschaft sorgen, entsteht trotz der offenen Gestaltung der „Rösler Innowelt“ niemals der Eindruck, man befände sich in einem Großraumbüro. Auch das Thema Lärmschutz wurde von der Geschäftsleitung sehr ernst genommen und mit viel Fingerspitzengefühl und technischer Raffinesse in die Bürolandschaft integriert, etwa durch bestimmte Deckenelemente oder den Einsatz von Stoff als Schallschlucker.
Besonders wichtig war es unserem geschäftsführenden Gesellschafter Stephan Rösler, dessen neues Büro übrigens in zentraler Position in die „Innowelt“ integriert wurde und während seiner Abwesenheit als Besprechungsraum genutzt werden darf, die Belegschaft bei der Umsetzung des neuen Bürokonzeptes miteinzubeziehen und Entscheidungen transparent zu machen. Über Kollegen, die sich freiwillig als Multiplikatoren an der Schnittstelle zur Geschäftsführung gemeldet hatten, konnte jeder Mitarbeiter seine Ideen und Vorschläge zur „Innowelt“ unkompliziert einbringen. Einmal pro Monat steht Stephan Rösler seinen Mitarbeitern im sogenannten Change Café zudem persönlich für Fragen und Anregungen rund um die „Innowelt“ zur Verfügung.
„Wir wollen für unsere Mitarbeiterinnen und Mitarbeiter modernste Arbeitsplätze mit Wohlfühlcharakter und somit beste Voraussetzungen für ein erfolgreiches Arbeitsumfeld schaffen, und uns so auch im Wettbewerb um Fachkräfte gut positionieren“, so Stephan Rösler. „Das Leuchtturmprojekt „Innowelt“ wird dabei einen entscheidenden Anteil haben. Ich danke schon jetzt allen Mitarbeitern, Dienstleistern und Zulieferern für die Unterstützung bei der Umsetzung und freue mich auf eine erfolgreiche Zusammenarbeit in der neu gestalteten Bürolandschaft.“
Die Umsetzung der „Innowelt“ begeistert aber nicht nur intern: Die Rösler Oberflächentechnik GmbH ist damit nun Referenzkunde bei der Unternehmensberatung ARCHONIC, die die Umgestaltung mit angestoßen und beratend begleitet hat. Damit dient das neue Bürokonzept künftig auch anderen Unternehmen als Vorbild und Muster bei der Umgestaltung ihrer eigenen Büros. Zudem hat die regionale Berichterstattung über die „Innowelt“ schon einen weiteren großen Arbeitgeber aus der Region davon überzeugt, eine solche Umgestaltung vorzunehmen.