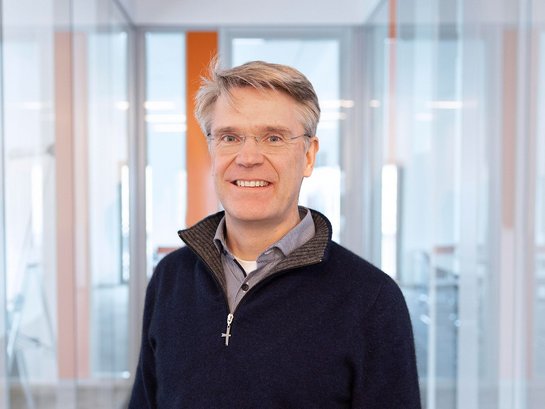
Establecer nuevos estándares con la mentalidad Rösler
Establecer nuevos estándares con la mentalidad Rösler
Acabado Mirro para llantas forjadas de alta gama en menos de 40 minutos
Menores costes y mayor productividad en los procesos de shot peening
AM Solutions producirá más equipos estándar de posprocesado AM
Arrancamos con el nuevo concepto de trabajo "Rösler Innowelt"
En los últimos años hemos tenido que renunciar a muchas cosas que considerábamos seguras. Hoy nos enfrentamos a la tarea de encontrar nuevas formas de asegurar un futuro estable. El camino hacia una nueva "normalidad" en los negocios, la tecnologÃa y la polÃtica es incierto y difÃcil, pero para asegurar nuestro éxito, debemos afrontar este reto sin rodeos. En nuestros esfuerzos por adaptar nuestro negocio a los rápidos cambios del entorno de mercado, podemos confiar en las fortalezas especiales de Rösler que hicieron que nuestra empresa tuviera tanto éxito en el pasado. Estos puntos fuertes son una base excelente para crear un futuro de éxito para la empresa.
Rösler tiene muchas caracterÃsticas fuertes que proporcionan una base sólida para hacer frente a cualquier nuevo desafÃo: La empresa dispone de tecnologÃas y productos probados con un excelente potencial de mercado. Además, la empresa tiene numerosos puntos fuertes inherentes, y con el lema "finding a better way" tenemos un principio rector que define nuestra mentalidad.
Para mà esto significa que incluso en tiempos difÃciles miramos hacia delante y trabajamos para el futuro. Tenemos la suerte de poder confiar en productos y procesos de eficacia probada, pero al mismo tiempo somos capaces de desarrollar conceptos innovadores.
Un buen ejemplo de esta combinación de métodos probados e innovadores es un proyecto de acabado de ruedas que realizamos para un gran cliente. Los resultados de acabado estético requeridos pueden conseguirse con métodos convencionales, pero también pueden mejorarse con nuevas ideas para que el proceso de acabado sea aún mejor.
En este proyecto concreto, el resultado fue un innovador sistema especial de acabado por inmersión. Este enfoque también funciona en el campo del endurecimiento superficial de componentes metálicos expuestos a grandes cargas. Los resultados requeridos se consiguen generalmente con el granallado, una tecnologÃa probada que se estableció hace mucho tiempo. Pero ahora hemos desarrollado mejoras que hacen que esta tecnologÃa sea aún mejor, más eficaz y más rentable: Con un software de simulación especial podemos simular electrónicamente el proceso de granallado en cualquier geometrÃa de pieza de trabajo. Esto nos permite definir con precisión los parámetros del proceso ya durante la fase de diseño, de modo que no se deja nada al azar.
También nos esforzamos por seguir mejorando nuestra cultura corporativa: Para ello estamos buscando nuevos métodos de trabajo y los estamos implantando con nuestro "Rösler Innowelt", un concepto de oficina que sigue la idea del Nuevo Trabajo con espacios de trabajo abiertos/compartidos.
Esto reforzará nuestra cooperación y comunicación internas. Combinado con herramientas digitales especiales y software de cooperación, nos permitirá reaccionar con mayor rapidez y flexibilidad a las peticiones de los clientes. Las mismas herramientas digitales se utilizarán también en nuestra producción. En un primer paso hemos centralizado la operación de fabricación de los equipos de nuestra marca AM Solutions - 3D Post Processing Technology. Para cumplir los requisitos de industrialización en la industria AM, en estas nuevas instalaciones estamos construyendo equipos estándar OEM y de postprocesado para la fabricación aditiva.
Todo esto no serÃa posible sin nuestra mentalidad Rösler: Construir sobre productos y procesos probados y mejorarlos con ideas innovadoras. Cada nuevo dÃa nos permite empezar algo nuevo y aventurarnos en nuevas áreas. De esta forma podemos salir de nuestra antigua "normalidad" y con "encontrar una forma mejor" crear una nueva "normalidad" que garantice la estabilidad en tiempos de rápidos cambios. Con este planteamiento ayudamos a nuestros clientes de todo el mundo a superar tiempos difÃciles y afrontar con éxito los nuevos retos del mercado. Y nuestros empleados podrán trabajar en un entorno estable que les permita mirar al futuro con confianza.
Espero que disfrutes con la lectura.
Saludos,
Dr. Till Merkel
Las llantas de aluminio forjado no sólo se caracterizan por su bajo peso, gran estabilidad y excelentes caracterÃsticas de soporte de carga, sino también por su exclusivo aspecto estético. Por ello, no es de extrañar que los fabricantes de automóviles de lujo utilicen principalmente llantas de aluminio forjado en sus vehÃculos. Los aspectos más destacados de las llantas de automóviles de gama alta no son sólo su atractivo diseño, sino también su inmaculado pulido de alto brillo. Para conseguir un acabado tan perfecto, las llantas deben someterse a una operación de rectificado y alisado de la superficie antes de poder pulirlas. Tratar las llantas con los métodos clásicos de acabado por vibración o acabarlas con un costoso trabajo manual requiere varias horas de procesado. Un importante fabricante querÃa reducir considerablemente el tiempo necesario para el acabado parcial de llantas bicolores ya pintadas y buscaba una solución técnica adecuada. La encontró con la Rösler Plunge Finisher R 1/1 TSA-O/VS-So de Rösler. La tecnologÃa de acabado por inmersión fue desarrollada por Rösler para el consistente y rápido desbarbado, radiado de bordes, rectificado de superficies y pulido de componentes complejos, pesados y delicados.
Proceso en dos fases con abrasivos y compuestos especialmente adaptados
La tarea de acabado de las llantas bicolor era especialmente difÃcil: la pintura ya aplicada no debÃa dañarse y, al mismo tiempo, las zonas de la superficie que debÃan acabarse debÃan recibir un pulido inmaculado de alto brillo. El proceso se desarrolla de la siguiente manera: Con un sistema de sujeción neumático, se fija una sola rueda inacabada al husillo de la máquina de acabado por inmersión. El sistema de sujeción especialmente diseñado permite el montaje manual o robotizado de las muelas. Al bajar el husillo giratorio, la llanta se sumerge en el recipiente de procesamiento lleno de abrasivos de esmerilado o pulido especiales. Para la operación de esmerilado fino se utilizan bolas de plástico cónicas especialmente desarrolladas para esta aplicación de acabado. El proceso se ve apoyado por la adición continua de agua y un compuesto de acabado adecuado. Durante el proceso, el husillo realiza una rotación central, orbital o recÃproca.
Los distintos movimientos de rotación también pueden combinarse. El movimiento resultante de la rueda garantiza la obtención de acabados superficiales uniformes y homogéneos, incluso en los detalles de diseño más complejos de las ruedas. La repetibilidad y consistencia de los resultados obtenidos era un requisito clave para que el proceso de acabado por inmersión fuera adecuado para la producción en serie. Esto se consigue gracias a caracterÃsticas técnicas especiales, como el motor vibratorio acoplado a la cuba de procesado y un sistema integrado de clasificación de bolas de tamaño insuficiente. Ambos garantizan una mezcla estable del material, lo que a su vez asegura una buena calidad de acabado.
A la operación de corte le sigue un ciclo de esmerilado fino de unos siete minutos. Para el pulido de alto brillo, las llantas se colocan en una segunda máquina de acabado de inmersión llena de bolas de pulido de porcelana. La operación de pulido requiere un tiempo de procesado de 25 a 30 minutos.
Ahorro de agua y compuestos
Para la limpieza del agua de proceso contaminada se instaló un sistema de tratamiento quÃmico del agua, diseñado especÃficamente para minimizar el consumo de agua y compuestos. Se utiliza principalmente para limpiar el agua de proceso de la operación de la retirada de material. El agua de proceso del proceso de pulido, que sólo está ligeramente contaminada, se recoge en un depósito intermedio y se reutiliza para la fase de rebajado/molienda fina. Los compuestos necesarios para cada etapa del proceso se inyectan automáticamente. La reutilización del agua de proceso de la fase de pulido para la fase de rebajado/afinado también contribuye a reducir el consumo total de compuestos.
El cliente no sólo quedó impresionado por las caracterÃsticas técnicas, sino también por la rentabilidad de la tecnologÃa de acabado por inmersión. Por ello, no es de extrañar que ya haya encargado más máquinas de acabado por inmersión para la próxima fase de ampliación de la lÃnea de procesado de llantas.
El shot peening, el "martilleo" de piezas con medios de granallado definidos con precisión, es una operación indispensable en industrias como la automovilÃstica y la aeroespacial. Al inducir una tensión residual de compresión en las piezas, la operación de shot peening mejora sustancialmente su resistencia a largo plazo frente a cargas de tracción y flexión. El proceso se utiliza para tratar componentes dentados, de dirección y transmisión, asà como muelles, cigüeñales y todo tipo de álabes de turbina. Una ventaja significativa de la operación de shot peening es que se puede reducir el peso del componente sin afectar a su capacidad de carga mecánica. Esto es especialmente beneficioso en los vehÃculos eléctricos, ya que aumenta su autonomÃa y reduce su consumo de energÃa. Debido a los cambios en las estructuras y formas de las piezas, la movilidad eléctrica requiere con frecuencia la modificación de los procesos de fabricación. Además, los clientes exigen una mayor eficiencia energética, de recursos y de costes. En otras palabras, mejoras significativas en productividad y sostenibilidad. Rösler puede proporcionar un apoyo integral para este tipo de proyectos de optimización.
Menor consumo de energÃa utilizando turbinas en lugar de sistemas de granallado por aire comprimido
Los sistemas de granallado con aire comprimido han sido las herramientas de shot peening predominantes para alcanzar de forma consistente los valores de tensión de compresión residual especificados. Una desventaja del método de aire comprimido es que requiere mucha energÃa. Hoy en dÃa, las innovadoras mejoras técnicas de la tecnologÃa de turbinas permiten el shot peening preciso y de alta calidad de una amplia gama de componentes con turbinas energéticamente eficientes y altamente productivas. Para muchas aplicaciones de granallado ya no son necesarios los costosos sistemas de chorro de aire comprimido. Los factores más importantes a tener en cuenta en las operaciones de granallado son la forma y el tamaño de la pieza, los resultados de granallado requeridos y los medios de granallado. Basándose en estos factores, Rösler realiza simulaciones por ordenador del patrón de granallado y de todo el proceso. Las simulaciones van seguidas de ensayos reales de granallado en nuestro Centro de Experiencia del Cliente (CEC). Dado que el CEC está equipado con una amplia gama de turbinas y sistemas de granallado por aire comprimido, las pruebas de granallado pueden realizarse en condiciones reales de producción. Con un difractómetro de rayos X propio, las pruebas de granallado pueden evaluarse rápidamente para determinar qué parámetros del proceso y qué medios de granallado generarán los resultados requeridos.
Un proyecto conjunto de optimización entre un importante fabricante de automóviles europeo y Rösler dio como resultado un ahorro energético del 30% y un aumento del 50% de la capacidad de granallado. Basándose en los convincentes resultados del proyecto, entretanto este cliente adquirió cuatro granalladoras equipadas con turbinas.
Menor desgaste del equipo y mayor productividad
A veces, una revisión de los parámetros de granallado existentes puede ayudar a mejorar significativamente todo el proceso de granallado. Una vez establecidos, es frecuente que los parámetros del proceso dejen de cuestionarse. Este descuido puede provocar un elevado desgaste del equipo y desaprovechar el potencial de mejora del proceso.
Unos parámetros del proceso perfectamente calibrados, incluida la selección óptima del abrasivo, garantizan una alta calidad del granallado, un menor desgaste del equipo y unos costes operativos reducidos. Si una revisión de los parámetros de granallado en una máquina existente no es suficiente, una reconversión puede ser la solución adecuada. Esto incluye, entre otras cosas, la actualización de la máquina con componentes más productivos, como turbinas más potentes, o el desarrollo de dispositivos para piezas nuevas o modificadas. La optimización del patrón de granallado siempre debe formar parte de las consideraciones.
En todos los casos, las pruebas de granallado en el CEC, junto con la evaluación de los resultados mediante difracción de rayos X, pruebas especiales de la cobertura de granallado y, si es necesario, rugosidad de la superficie y mediciones microscópicas de luz, garantizarán que se alcancen las especificaciones de granallado requeridas. La selección de la granalla adecuada es muy importante para la eficiencia de recursos y costes del proceso. Un análisis de la granalla siempre ayudará a determinar si la granalla actual es la adecuada para la aplicación en cuestión.
¿Granallado en húmedo o en seco?
El shot peening con pistolas de chorro de aire comprimido puede realizarse en seco o en húmedo. Las ventajas del método de granallado en seco son una mayor intensidad de granallado y el granallado selectivo de zonas especÃficas de la superficie. Además, todo el proceso y el abrasivo pueden controlarse con precisión. La tecnologÃa de granallado en húmedo evita que los abrasivos se incrusten en las piezas y reduce la rugosidad de la superficie. Como el chorreado en húmedo es más suave que el chorreado en seco, es el método ideal para tratar piezas delicadas con paredes finas sin deformarlas. Cada uno de los dos métodos de granallado tiene sus ventajas. Por lo tanto, el método elegido debe ajustarse perfectamente a la aplicación correspondiente, especialmente en lo que respecta a la rentabilidad y la calidad de los resultados del granallado. Rösler ofrece una amplia gama de diferentes tipos de máquinas. Esto permite una selección de equipos totalmente objetiva y garantiza que los clientes obtengan la mejor solución posible para sus requisitos especÃficos.
Todos los pasos relativos a la alteración y optimización del proceso, incluyendo las pruebas de procesado y la evaluación del proceso, pueden modificarse para que el equipo de shot peening pueda adaptarse rápidamente a las cambiantes condiciones de producción. Esto garantiza unos resultados de granallado absolutamente constantes y de alta calidad durante toda la vida útil del equipo. Y garantiza que se cumplan plenamente todos los requisitos de eficiencia energética, de recursos y de costes.
Al crear la marca AM Solutions como especialista en posprocesado de componentes impresos en 3D en 2018, Rösler Oberflächentechnik GmbH hizo gala de una notable previsión estratégica. David Soldan, responsable de AM Solutions, explica: "Lo que comenzó como un producto auxiliar de nicho dentro de nuestras actividades "normales" de tratamiento de superficies, se ha convertido en una tercera sección de negocio viable y de rápido crecimiento en igualdad de condiciones con las divisiones de acabado en masa y granallado. Una de las razones de este notable éxito es que AM Solutions puede aprovechar los 80 años de experiencia en el campo del tratamiento industrial de superficies y la capacidad de resolución de problemas de la empresa matriz. Especialmente útil para esta dinámica y ágil puesta en marcha es su integración en los procedimientos organizativos de una gran empresa bien establecida."
Con la creciente expansión de la lÃnea de productos y las demandas de los clientes, se hizo más difÃcil producir eficientemente los equipos de postprocesado en las respectivas instalaciones de fabricación de equipos de acabado en masa y granallado.
Por este motivo, la empresa decidió centralizar la producción de
AM Solutions - 3D post processing technology. Una vez tomada la decisión de ofrecer la mayorÃa de las máquinas de posprocesado como equipos estándar de eficacia probada, se hizo evidente que la producción de AM Solutions debÃa tener su propio "hogar". Esto permitió la creación de una moderna área de desarrollo y producción con secciones de montaje dedicadas. En el marco de la integración vertical, la nueva área de producción permite el desarrollo y la implementación de soluciones de postprocesado innovadoras y flexibles, desde los conceptos de diseño hasta su implementación práctica, todo de la mano de un único proveedor.
"En unos 1.000 metros cuadrados hemos implantado fÃsica y organizativamente el concepto de cadena de suministro integrada: La zona de producción se complementa con un centro de control moderno y estéticamente agradable con paredes de cristal que incluye una zona de co-working y una sala de conferencias para conversaciones con clientes y reuniones internas", comenta Stephan Böhnlein, responsable de producción de equipos y gestión de la cadena de suministro de Rösler. "El centro de control está equipado con todos los accesorios técnicos necesarios para un entorno de producción flexible. Contiene estaciones de trabajo para ingenierÃa, desarrollo de software y creación de prototipos. Esto permite a los ingenieros discutir sus diseños con los equipos de montaje en el centro de producción y resolver rápidamente los problemas técnicos."
Las seis nuevas estaciones de montaje se diseñaron teniendo en cuenta los principios de la gestión ajustada y cumplen plenamente las reglas de las 5S. Esto significa que las cantidades correctas de material están siempre en el lugar adecuado en el momento en que se necesitan. Los empleados pueden centrarse en sus funciones principales, producir poco o ningún desperdicio y conseguir un ahorro significativo en el tiempo de producción. El control de la producción se organiza mediante el sistema Kanban, un concepto de suministro de material diseñado para un flujo de trabajo continuo y unos costes de producción optimizados.
Las mejoras de todo el proceso de producción son sustanciales: Los tiempos de montaje se redujeron considerablemente sin poner en peligro la calidad del producto. Al mismo tiempo, se pudo racionalizar el transporte interno en el proceso de producción y reducir los costes de transporte. Un sistema de trabajo electrónico, prácticamente sin papel, proporciona una rápida visión general del estado de la producción. Permite a AM Solutions - 3D post processing technology mantener una tasa de entregas a tiempo superior al 92 % y suministrar a sus clientes productos de alta calidad. Además, la proximidad entre el desarrollo de equipos y la producción permite dar una respuesta rápida y flexible a las peticiones de los clientes.
Está previsto que en un futuro no muy lejano se produzcan hasta 300 máquinas de postprocesado al año en la nueva zona de producción. Todo el concepto de puesto de trabajo es muy flexible, de modo que el número de máquinas producidas puede prácticamente duplicarse, si el mercado exige tal aumento.
David Soldan, responsable de AM Solutions, está satisfecho con el nuevo sistema de producción: "Al pasar nuestra producción de máquinas estándar a volúmenes más elevados, podemos suministrar nuestros equipos mucho más rápidamente a nuestros clientes. Pero la proximidad fÃsica entre el desarrollo de productos y la producción sigue permitiéndonos satisfacer rápidamente las peticiones especiales de los clientes. Aceptar los requisitos de una pequeña empresa de nueva creación en una empresa consolidada con más de 80 años de antigüedad es una prueba de la notable flexibilidad y apertura de la alta dirección de Rösler". Soldan concluye: "En el marco de nuestro nuevo sistema de producción tenemos previsto ofrecer entre cinco y seis máquinas de postprocesado como productos estándar".
Compartir citas, zonas de anclaje, cafeterÃa de trabajo, polÃtica de escritorios limpios: en los últimos meses se ha producido silenciosamente un importante cambio del sistema de oficinas en la sede central del grupo Rösler en Untermerzbach. Los cuatro edificios de oficinas de este emplazamiento están siendo completamente desmantelados, renovados y modificados para convertirlos en modernas estancias de oficinas organizadas según los principios del Nuevo Trabajo.
Los primeros compañeros ya se han trasladado a sus oficinas recién organizadas y están entusiasmados con su nuevo entorno, denominado "Innowelt" en Rösler. Todo el proyecto estará terminado a mediados del año que viene. En ese momento, prácticamente todas las oficinas se habrán modernizado en cuanto a equipamiento, atractivo visual y ergonomÃa. Se trata de un proyecto que marcará tendencia en toda la región. Uno de los principales objetivos era integrar varios departamentos de la sede de Bad Staffelstein en la de Untermerzbach de forma rentable y sostenible, y evitar costosas nuevas construcciones.
En el "Rösler Innowelt", los puestos de trabajo fijos de los distintos departamentos se sustituyen por las llamadas "zonas de anclaje", que permiten a los empleados cambiar de un puesto de trabajo a otro. Debido a las normas vigentes sobre el trabajo desde casa, muchos compañeros ya no trabajan en la empresa todos los dÃas. Al final de cada jornada laboral, los empleados recogen sus mesas y depositan sus útiles de oficina, como auriculares, ordenadores portátiles y objetos personales, en taquillas especÃficas.
En un lugar central de cada planta se encuentra la llamada cafeterÃa de trabajo, que consta de un salón y una zona de cocina. Allà los empleados pueden discutir proyectos comunes en un ambiente relajado. En numerosos compartimentos pequeños y salas de conferencias, los compañeros pueden hacer llamadas telefónicas confidenciales y reunirse para hablar. Estos detalles del edificio crean una agradable segmentación del entorno y garantizan que el concepto abierto del "Rösler Innowelt" no dé la impresión de una oficina monótona de planta abierta. La dirección también tuvo en cuenta las medidas de reducción del ruido y las integró en el paisaje de oficinas de forma discreta e innovadora. Por ejemplo, con modernos paneles en el techo o el uso de telas como material fonoabsorbente.
Nuestro director general, Stephan Rösler, deseaba integrar su nuevo despacho en el "Innowelt" en un lugar céntrico. Durante su ausencia, el despacho puede utilizarse como sala de reuniones. Se hizo partÃcipes a los empleados en la fase de planificación y ejecución, y se les explicaron detalladamente todas las decisiones. A través de compañeros que actuaban voluntariamente como interfaz con la dirección, cada empleado podÃa presentar sin burocracia sus ideas y propuestas al concepto "Innowelt". Una vez al mes, Stephan Rösler está disponible en el llamado café del cambio para responder a las preguntas y debatir las sugerencias de los empleados sobre "Innowelt".
Stephan Rösler explica: "Queremos crear un entorno de trabajo moderno para nuestros empleados, que transmita una impresión de bienestar y, por tanto, genere las condiciones para un ambiente de trabajo productivo. Al mismo tiempo, esto hará que la empresa resulte más atractiva para los empleados cualificados". El proyecto "Innowelt", verdaderamente pionero, será un factor sustancial para alcanzar estos objetivos. Desde ahora quiero agradecer a todos los empleados, subcontratistas y proveedores su apoyo en la ejecución del proyecto. Y espero que el ambiente de trabajo en las oficinas recién organizadas sea satisfactorio y armonioso".
El proyecto "Innowelt" no sólo tiene efectos positivos a nivel interno: Rösler Oberflächentechnik GmbH es ahora un cliente de referencia de la empresa de consultorÃa de gestión ARCHONIC, que inició el proyecto y colaboró en su ejecución. Por tanto, el nuevo concepto de oficina servirá de pauta a otras empresas para reorganizar sus propias oficinas. Además, la cobertura de "Innowelt" en la prensa regional ya ha convencido a otra gran empresa de la región para emprender una reorganización de este tipo.