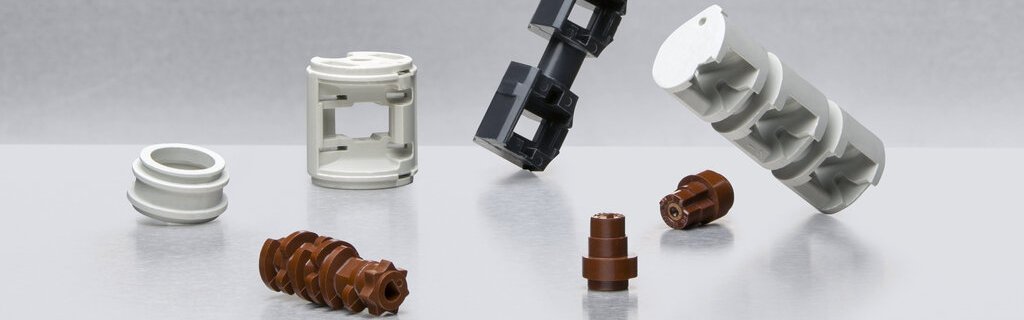
Plastic Deflashing, Part 1 – Plastic Component Advantages & Types
, RoslerUSA - Zurück zur Übersicht
Plastic's transformative impact is increasingly replacing metal in manufacturing. Learn how the characteristics of polymer-based materials will continue this trend.
Plastic Deflashing, Part 1 – Plastic Component Advantages & Types
For centuries metal and wood were the primary raw materials used for industrial products. With the invention of plastic, this production situation and possibilities changed dramatically.
While the world’s first synthetic plastic, Bakelite, was invented in 1907, the large-scale use of industrial plastics only took off in the 1950s. At that point, approximately 10 million tons of plastic were produced annually.
Annual plastic production has grown to 400 million tons today. With the increased use of additive manufacturing, global plastic production is expected to increase to 1.1 billion tons by 2050.
Rosler has worked with a variety of materials to provide surface finishing expertise, equipment, and consumables over the last 80 years. For molded plastic work pieces, deflashing is the most common form of surface finishing.
Understanding plastic, its capabilities, and required processing helps us be the best partner for your surface finishing needs.
Plastic Versus Metal
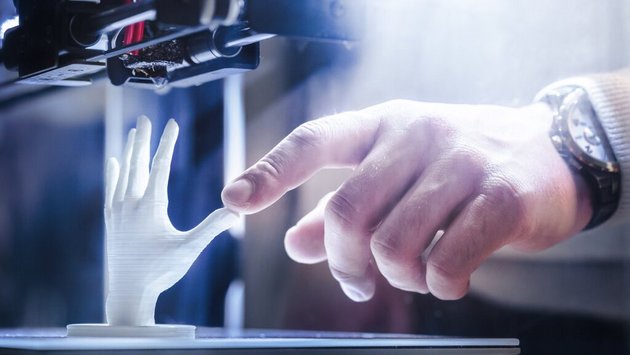
Many industrial components can be made from metal or plastic, for example, impellers. Both materials offer their own technical advantages and shortcomings.
For example, plastic components are generally lightweight. They are easier to form and are highly malleable. This means that plastic allows the creation of highly complex shapes. Plastic components are also highly resistant to chemical reactions such as oxidation and corrosion. Finally, they are easier to machine than metal components.
Major shortcomings of plastic components to date have been their limited resistance to heat and that they have a somewhat weaker structure than metal.
On the other hand, metal has a higher tensile strength than plastic and has better heat resistance. On the downside, it is more difficult to create complex shapes with metal. And metal components are generally more expensive than plastic.
With the transformation from combustion engines to electric vehicles, the utilization of heat-resistant metal parts will decline in favor of plastic components. However, the heat resistance of plastic is constantly improving.
Today, there are high-performance polymers capable of withstanding a permanent service temperature of up to 570 F. As other drawbacks of plastic are similarly abated, the use of plastic will further grow at the expense of metal.
Making Plastic Components
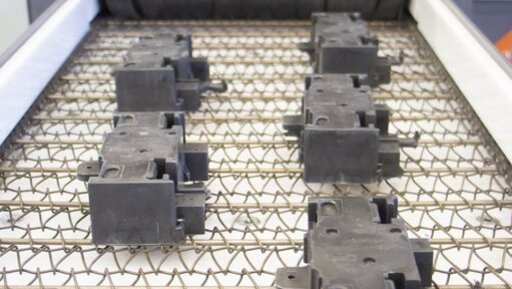
Raw materials for plastics are natural gas, oil, or plants. Through a sophisticated refinement process, these materials are transformed into what are known as polymers.
The polymers are fed into an extruder, where they are melted and pressed through a die. As the plastic cools, it forms a long tube, which is then cut into small pellets. In turn, these pellets are molded into auto parts, medical devices, water bottles, food packaging, etc.
The molding process takes place in an injection molding machine, where the pellets are poured into a hopper and melted by the application of heat. The now-liquified material is then forced through a nozzle and delivered to a mold where it receives its final shape.
A mold always consists of two halves. There are single-cavity molds for shaping a single component as well as multi-cavity molds allowing the simultaneous shaping of several parts.
With the increased use of additive manufacturing, the production of plastic components got another boost. Evolving technology allows for the creation of even more complex component shapes than injection molding. Additive manufacturing also provides economically viable manufacturing technology for volume production.
Types of Plastics

With regard to their physical characteristics, such as hardness, breaking strength, formability, elasticity, temperature restrictions, and resistance to chemicals, plastic materials are classified into three main categories, including duroplastics, thermoplastics, and elastomers.
Duroplastics
Also called thermosets, duroplastics have a relatively high hardness. They cannot be deformed or melted after hardening. When being manufactured, duroplastic components undergo a chemical hardening process. These types of plactics can resists high temperatures.
The first duroplastic material was Bakelite. It is still used for brake pads and other automotive and electrical components. Other duroplast materials use polyester resins, polyurethane resins, phenolic plastics, etc.
Typical duroplastic products include electrical hardware, parts for household goods, pistol grips, toothbrush holders, toilet seats, and fan housings.
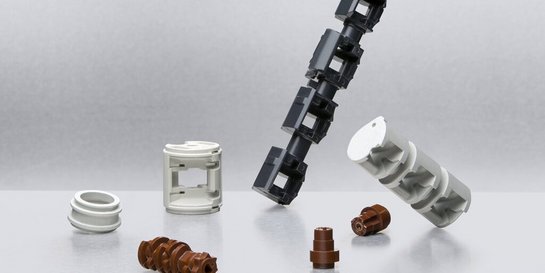
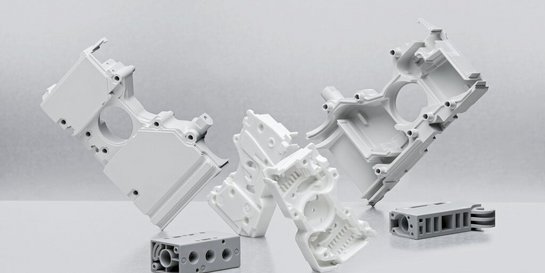
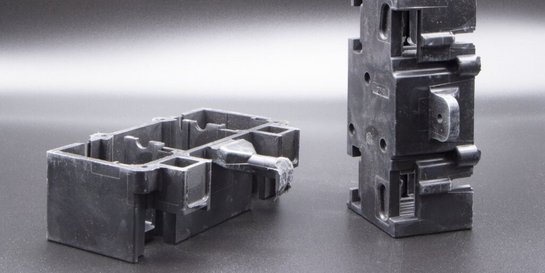
Thermoplastics
By far the most used materials are thermoplastics or plastomers. Thermoplastics have a medium hardness. Due to their relatively low melting point, they can be reshaped by applying heat yet maintain their shape after cooling.
Thermoplast materials include polyethylene, polypropylene, PVC, and polycarbonate.
Thermoplastics are generally divided into industrial, engineered, and high-performance plastics. The latter are filled with reinforcing materials like glass or carbon fibers or glass beads. This increases their hardness, rigidity, impact resistance, and heat resistance.
Typical thermoplastic products include airline and automotive parts, toys, eyeglass frames, storage bins, water bottles, and PVC pipes.
Elastomers
Highly elastic in nature, elastomers have a low hardness. Under pressure or when they are stretched, elastomers will change their shape but will immediately return to their original shape. Rubber bands are a good example of these characteristics.
Elastomer materials include polyurethane (PUR), rubber, and silicone.
Typical elastomer products include baking molds, window and door seals, polyurethane wear protection, O-rings, miscellaneous rubber components, and rubber boots.
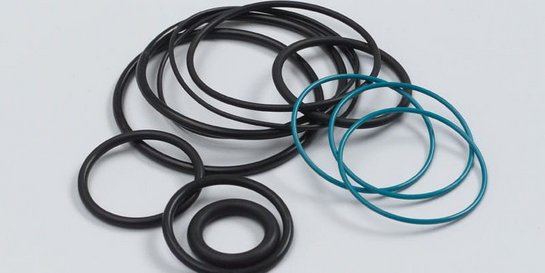
Comparatively, the major differences between duroplastics, high-performance thermoplastics, and elastomers are their respective hardness and elasticity.
Duroplastics offer the highest hardest but the lowest elasticity, while elastomers offer the opposite; low hardness and high elasticity. High-performance thermoplastics offer the median range of both hardness and elasticity.
The Rosler Way
By performing highly informative processing tests and drawing on decades of experience, Rosler finds the ideal solution for the wide-ranging plastic processing and deflashing needs. Along with developing specific machining processes, we can also provide the proper auxiliary equipment and consumables.
Our experience and the ability to design, service, and maintain machines as well as provide the consumables and accessories required to get the finish you require make Rosler a well-rounded, single source for surface finishing expertise. We are confident in our ability to develop surface preparation and finishing technologies to meet any modern foundry operation.
Contact us to discuss your deflashing needs or to request a free processing trial in one of our Customer Experience Centers.
The Plastic Deflashing series will continue with:
- Part 2 – Formation of Flashes & Removal Methods.
- Part 3 – Turbine Versus Air Blasting.
- Part 4 – Shot Blasting Machine Features.
- Part 5 – Machine Selection & Options.
- Part 6 – Automation & Digitization.
- Part 7 – Consumables.