
Trockenes Elektropolieren: DryLyte-Verfahren zur Hartmetallbearbeitung begeistert Kunden und Forschung
, A.Altmann - Zurück zur Übersicht
Das DryLyte-Verfahren zum Elektropolieren von Hartmetallwerkzeugen steht kurz vor dem Durchbruch. Zahlreiche, namhafte Kunden aus der Werkzeugbranche haben bereits im letzten Jahr ihre Chance genutzt und eine Testbearbeitung auf einer DLyte-Anlage durchführen lassen. Die Resonanz darauf ist überwältigend. Nach der ersten Testbearbeitung sind rund 90 Prozent der Kunden von dem Verfahren überzeugt, nach einer zweiten Testbearbeitung sind es quasi alle.
Doch was steckt eigentlich hinter der DryLyte-Technologie für die Bearbeitung von Hartmetallwerkzeugen?
Beim DryLyte-Verfahren handelt es sich um eine innovative und neuartige Technik zum Polieren, Entgraten und Verrunden von Metallen. Dabei erfolgt der Materialabtrag nicht abrasiv, sondern durch Ionenaustausch vom Werkstück in Richtung Verfahrensmittel. Das DryLyte-Verfahren wird auch trockenes Elektropolieren genannt. Im Vergleich zum flüssigen Elektropolieren erfolgt der Materialabtrag zielgerichteter und mehr selektiv, und die feinsten Werkstückgeometrien bleiben erhalten. Das Verfahren eignet sich besonders gut für die Bearbeitung von Hartmetallen, weil es die Materialstruktur und das Materialgefüge nicht verändert. Gängige mechanische Oberflächenveredelungsverfahren sind beim Polieren von Wolframcarbid und Sintercarbid nicht effektiv, da sie zu hart sind und daher die Verbesserung der Oberflächenqualität mit einer unkontrollierten Verrundung der Kanten einhergeht. Chemische oder elektrochemische Alternativverfahren zur Oberflächenbearbeitung haben den Nachteil, dass sie dazu führen, dass das Kobalt spontan in einer Reaktion freigesetzt wird, die man gemeinhin als Auswaschung oder Auslaugung bezeichnet und die Struktur zusammenbricht.
Welche Herausforderungen stellt die Branche an die Werkzeugbearbeitung?
Am Markt gibt es drei Hauptanforderungen:
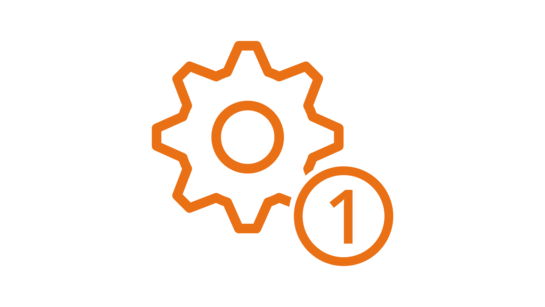
Definierte Schneidkantenverrundung im µ-Bereich, um eine homogene Schneidkante zu erreichen und die Standzeiten der Werkzeuge zu erhöhen.
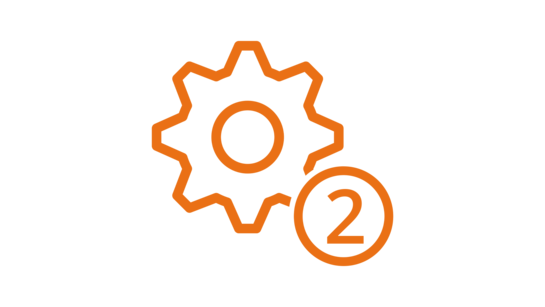
Starke Reduzierung der Oberflächenrauheit durch Polieren für eine verlustfreie Kraftübertragung beim Einsatz des Werkstücks.
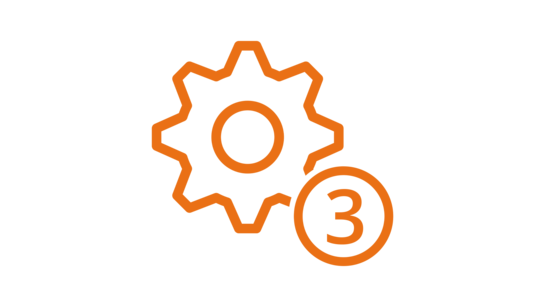
Polieren der Spankanäle für eine effizientere Spanabfuhr während des Bearbeitungsprozesses.
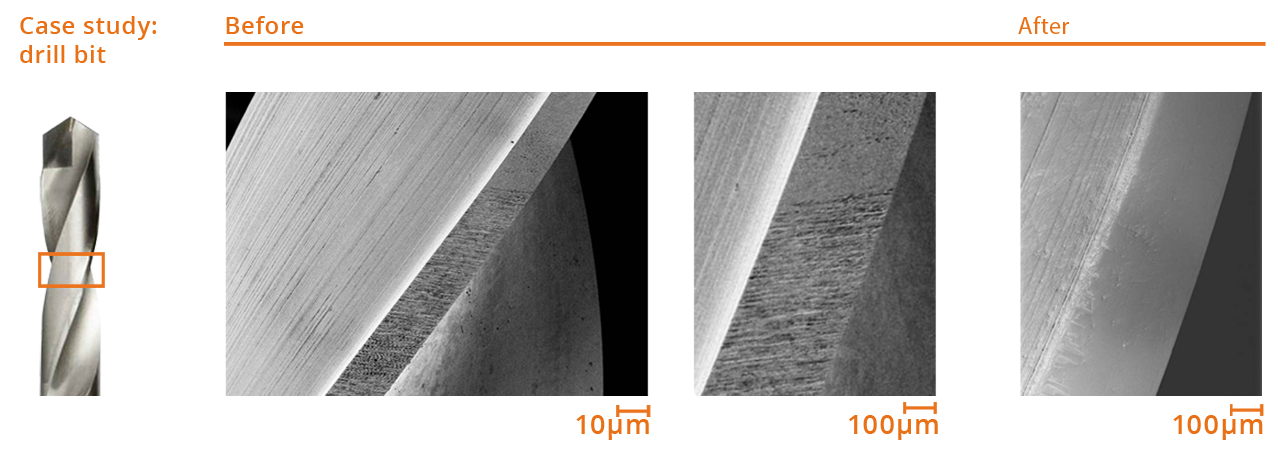
Die Schneidkantenverrundung ist deshalb so wichtig, weil jedes Werkstück andere Anforderungen hat. Manche müssen sehr scharf bleiben, andere können sehr stark abgerundet werden. Die entsprechenden Vorgaben hinsichtlich des angestrebten Rauheitswertes werden vom Kunden gemacht. Basierend auf diesen Vorgaben und dem Ausgangszustand des Werkstücks werden dann sowohl das Elektrolyt als auch die weiteren Prozessparameter wie Bearbeitungsdauer und Bearbeitungsgeschwindigkeit definiert, um einen perfekten Medien- und Stromdurchfluss durch das gesamte Werkstück zu gewährleisten und somit die bestmögliche Bearbeitung zu ermöglichen. Anschließend müssen die Bearbeitungsparameter dann nicht mehr verändert werden und garantieren eine langfristige, konstant gute und in höchstem Maße reproduzierbare Teilebearbeitung.

Erhöhung der Standzeit um rund 20 Prozent
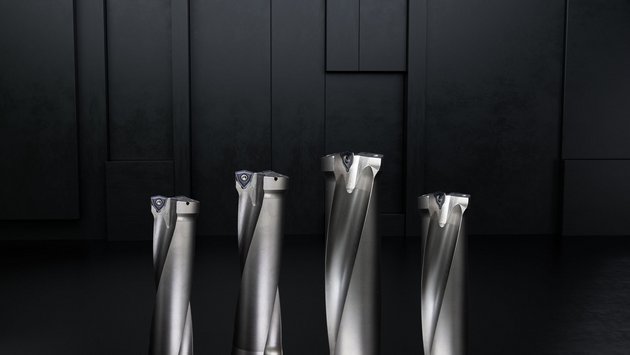
Aktuell verwendet ein Großteil der Kunden für die Schneidkantenbearbeitung ein Schleppschleifverfahren oder alternative chemische Verfahren. Beiden ist das DryLyte-Verfahren in vielerlei Hinsicht weit überlegen, etwa wenn es um die Standzeit der bearbeiteten Werkzeuge geht. Auf Basis der von uns bei Musterbearbeitungen erhobenen Daten, die auch die anschließenden Tests bei unseren Kunden bestätigt haben, geht hervor, dass Werkzeuge, welche mit der DryLyte-Technologie bearbeitet wurden, eine um rund 20 Prozent höhere Standzeit aufweisen. Vereinzelt berichten Kunden sogar von einer bis zu drei Mal höheren Standzeit, dabei dürfte es sich aber um Extremwerte handeln, welche durch den Bearbeitungsprozess bedingt sind.
Kundenfeedback
Nicht nur die längere Standzeit begeistert die Kunden. Diese loben unter anderem auch die bessere Fräsqualität mit weniger Gratbildung und die perfekten Ergebnisse bei den wichtigsten Faktoren Rundung und Oberfläche. Diese Ergebnisse wurden laut Kundenfeedback so noch nie mit einem anderen Verfahren oder einer anderen Maschine erreicht. Außerdem bestätigen die Kunden, dass es durch den Bearbeitungsprozess zu keinem Kobalt Leaching kommt. Die oberflächliche Chemie und die Mikrostrukturen bleiben unverändert, die mechanische Integrität bleibt konstant.
Stimmen aus der Forschung
In einer Studie konnte die Wirksamkeit des DryLyte-Verfahrens, welches vom spanischen GPAINNOVA-Konzern entwickelt wurde, nachgewiesen werden.
Auf der Grundlage der durchgeführten Untersuchungen und der erzielten Ergebnisse können die folgenden Schlussfolgerungen gezogen werden:
- Die DryLyte-Technologie ermöglicht es, Wolframcarbid-Cobalt-Hartmetalle zu polieren, die Rauheit zu reduzieren und Nachbearbeitungsfehler wie pulverisierte Wolframcarbid-Körner und/oder verschmierte Kobalt-Phasen zu entfernen. Darüber hinaus wird kein Auslaugungseffekt auf den metallischen Kobalt-Binder beobachtet.
- Eine Verringerung der bereits vorhandenen Schleifeffekte nimmt in den ersten 15 Minuten linear ab. Die Oberflächenintegrität in Bezug auf Härte und Elastizitätsmodul ist jedoch während der gesamten hier untersuchten Polierzeiten noch intakt.
- Nanoindentationstests zeigen eine klare Korrelation zwischen Mikrostruktur und mechanischen Eigenschaften in Bezug auf Härte und Elastizitätsmodul. Durch Verringerung der vorhandenen Defekte und Erhöhung der Trockenelektropolierzeit werden stabile Ergebnisse erzielt.