
Dry electropolishing: DryLyte process for carbide machining impresses customers and research
, A.Altmann - Back to overview
The DryLyte process for electropolishing carbide tools is on the verge of a breakthrough. Numerous well-known customers from the tool industry already took the opportunity last year to have a test treatment carried out on a DLyte system. The response has been overwhelming. After the first test machining, around 90 percent of customers are convinced by the process, and after a second test machining, virtually all of them are.
But what is actually behind the DryLyte technology for machining carbide tools
The DryLyte process is an innovative and new technology for polishing, deburring and rounding metals. The material is not removed abrasively, but by ion exchange from the workpiece towards the process medium. The DryLyte process is also known as dry electropolishing. Compared to liquid electropolishing, material removal is more targeted and selective, and the finest workpiece geometries are retained. The process is particularly suitable for processing hard metals because it does not change the material structure or material microstructure. Common mechanical surface finishing processes are not effective when polishing tungsten carbide and cemented carbide as they are too hard and therefore the improvement in surface quality is accompanied by uncontrolled rounding of the edges. Chemical or electrochemical alternative surface finishing processes have the disadvantage that they cause the cobalt to be released spontaneously in a reaction commonly referred to as leaching and the structure collapses.
What challenges does the industry pose for tool processing
There are three main requirements on the market:
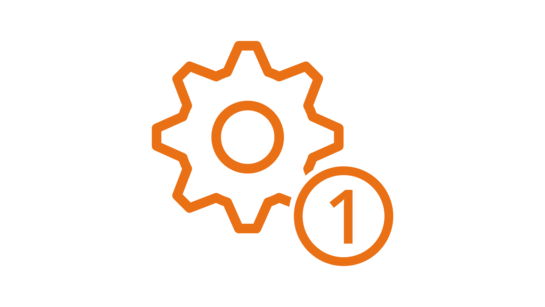
Defined cutting edge rounding in the ” range to achieve a homogeneous cutting edge and increase tool life .
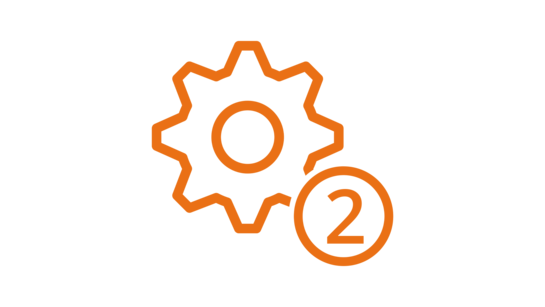
Significant reduction in surface roughness through polishing for loss-free power transmission when using the workpiece.
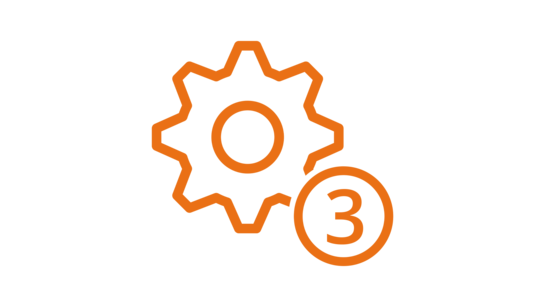
Polishing of the chip channels for more efficient chip removal during the machining process.
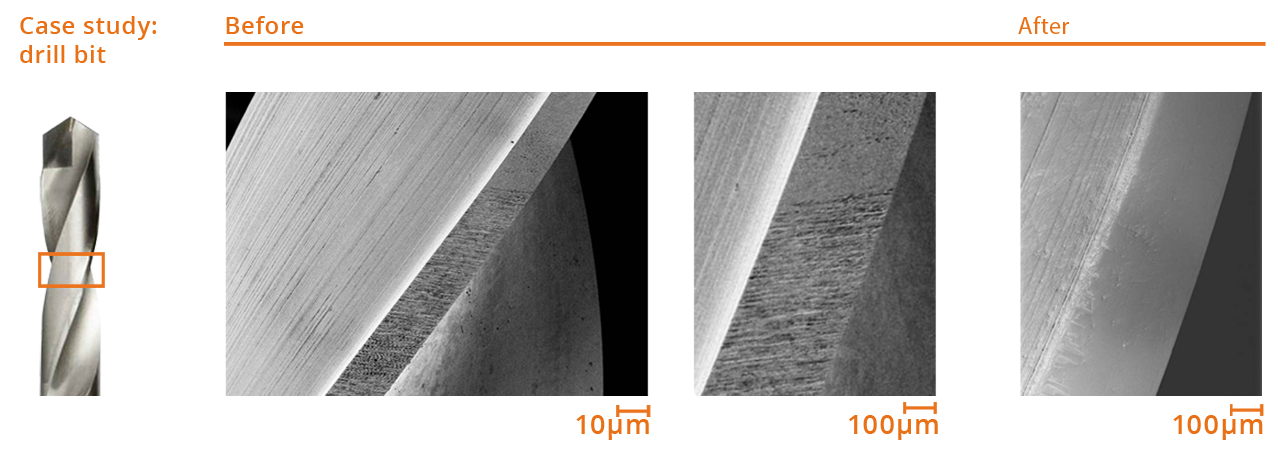
Cutting edge rounding is so important because every workpiece has different requirements. Some must remain very sharp, others can be rounded off very much. The corresponding specifications regarding the desired roughness value are made by the customer. Based on these specifications and the initial condition of the workpiece, both the electrolyte and the other process parameters such as processing time and processing speed are then defined in order to ensure a perfect flow of media and current through the entire workpiece and thus enable the best possible processing. The machining parameters then no longer need to be changed and guarantee long-term, consistently good and highly reproducible part machining.

Increasing tool life by around 20 percentIncreasing tool life by around 20 percent
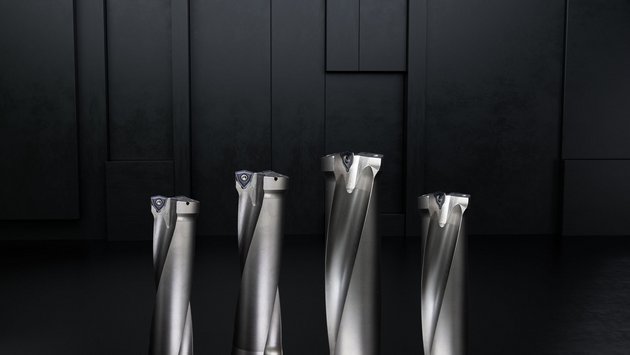
The majority of customers currently use a drag finishing process or alternative chemical processes for cutting edge machining. The DryLyte process is far superior to both in many respects, for example when it comes to the service life of the machined tools. Based on the data we collected during sample processing, which was also confirmed by subsequent tests at our customers, it is clear that tools processed using DryLyte technology have a tool life that is around 20 percent longer. In some cases, customers even report a tool life that is up to three times longer, but these are likely to be extreme values due to the machining process.
Customer feedback
Customers are not only impressed by the longer tool life. They also praise the improved milling quality with less burr formation and the perfect results for the most important factors of rounding and surface finish. According to customer feedback, these results have never before been achieved with any other process or machine. Customers also confirm that the machining process does not result in cobalt leaching. The surface chemistry and microstructures remain unchanged and the mechanical integrity remains constant.
Voices from research
The effectiveness of the DryLyte process, which was developed by the Spanish GPAINNOVA Group, was demonstrated in a study.
Based on the tests carried out and the results obtained, the following conclusions can be drawn:
-
DryLyte technology makes it possible to polish tungsten carbide-cobalt carbides, reduce roughness and remove post-processing defects such as pulverized tungsten carbide grains and/or smeared cobalt phases. In addition, no leaching effect on the metallic cobalt binder is observed.
-
A reduction in the pre-existing loop effects decreases linearly in the first 15 minutes. However, the surface integrity in terms of hardness and modulus of elasticity is still intact throughout the polishing times investigated here.
-
Nanoindentation tests show a clear correlation between microstructure and mechanical properties in terms of hardness and modulus of elasticity. By reducing the existing defects and increasing the dry electropolishing time, stable results are achieved.