
Dry electropolishing is a completely new and innovative process for the surface treatment of metals. It enables fast, automatable, and cost-effective surface finishing that achieves a quality equivalent to manual polishing. At the same time, it reduces the environmental impact because the chemicals required for processing are bound in solids.
The DryLyte process from our partner GPAINNOVA
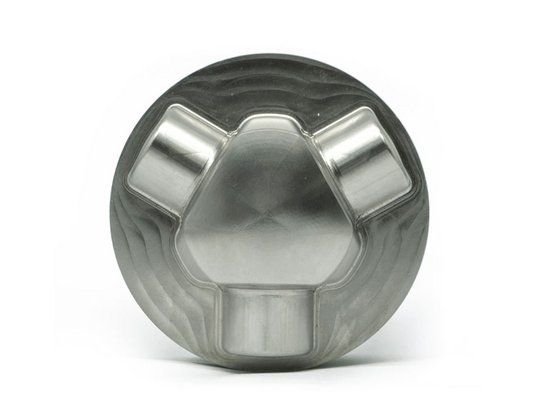
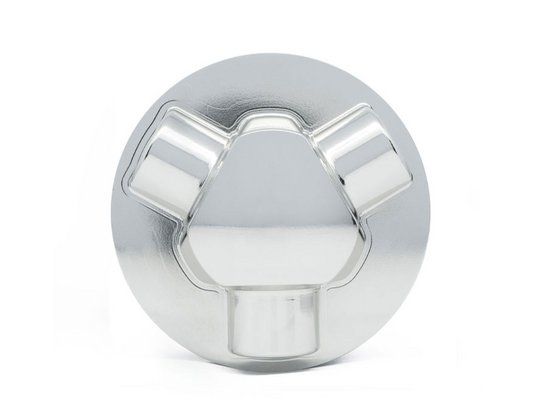
The DryLyte process was developed by the Spanish technology company GPAINNOVA. Rösler OberflÀchentechnik GmbH is a partner of GPAINNOVA and is exclusively responsible for the distribution of DLyte systems throughout Germany.
The decisive difference to liquid electropolishing: The electrolyte required for the machining process is stored in a solid granulate. Accordingly, no liquid acids are required, which means that the process scores over conventional electropolishing systems: dry electropolishing is less harmful to the environment than the liquid version, which is why less stringent guidelines apply to system operation, for example regarding employee protection and disposal of the process media.
A special feature of dry electropolishing is that the workpiece contours are very well preserved despite the high surface quality. Compared to liquid electropolishing, the amount of electrolyte required for operation is lower due to the carrier material, which is why the system technology represents a resource-saving and environmentally friendly surface treatment.
The DryLyte process was initially developed for the dental industry for processing model castings and crowns made of cobalt-chrome. It is now used in numerous industries in which particularly high demands are placed on surface quality. These range from the production of luxury goods to toolmaking. This is because increasingly demanding quality standards on the market make a perfect surface finishing necessary for a variety of products for aesthetic and mechanical-physical reasons.
The DryLyte process often replaces manual polishing and thus offers relief in times of a shortage of skilled labour. The reproducibility of the polishing results is also a clear advantage.
Examples of applications can be found at an Italian manufacturer who no longer needs to have belt buckles from a well-known luxury brand laboriously machined by hand, but also at a US manufacturer of ship propellers who was previously only able to achieve perfect surfaces on its turbines and propellers with the help of manual machining.
How it works
The DryLyte process is an electrochemical process for deburring, smoothing and polishing metal. Its mode of action is not based on the mechanical abrasion of the surface but is achieved by means of ion exchange. For this purpose, parts to be processed are attached to workpiece spindles and immersed in the processing container, which is filled with an electrolyte medium. This medium consists of polymer granulate, which absorbs the electrolyte and acts as a carrier. During processing, the polishing current flows from the container jacket over the surfaces of the granulate particles to the workpiece. Electrochemical reactions take place at the contact points between the workpiece and the granulate. The geometry and the dry properties of the granulate ensure that only the roughness peaks of the surface structure of the workpiece are electrochemically influenced or removed. This is because material is only removed at these contact points between the granulate and the component surface - in contrast to liquid electropolishing, where the workpiece is completely surrounded by the process fluid.
The more selective approach of the DryLyte process achieves a rapid increase in the contact area of the surface compared to conventional electropolishing. By only removing the roughness peaks, less material is removed overall.
Facts, figures, and data
Dry electropolishing reduces roughness by over 80 per cent and avoids undesirable effects such as orange peel or pitting. It guarantees precise and homogeneous surface results without micro-scratches or cracks, even with the most intricate geometries, because it preserves the tolerances and original workpiece shapes, and no mechanical forces are exerted on the workpiece during processing.
In terms of its electrochemical properties, the DryLyte process is also suitable for machining carbide and is a popular process in tool and mould making. Here, DryLyte can contribute to greater material strength by increasing the service life of the tool through controlled, minimal edge processing and polishing of the tool surface without cobalt leaching.
Compared to liquid electropolishing, the dry process increases corrosion resistance by up to four times. Another advantage of DryLyte technology is the comparatively short process times. Depending on the application, initial roughness and desired result, they range from a few minutes to 1.5 hours.
-
Liquid electropolishing
- All surfaces contact liquid
- General oxidation
- Low discrimination -
Dry elecropolishing
+ Spheres contact on roughness peaks
+ Localized oxidation
+ Selective removal of metal
+ Geometry preservation
+ Improved corrosion resistance
Ecological aspect

In dry electropolishing, the removed material is completely absorbed by the electrolyte process agent. When the process medium is saturated and needs to be replaced, this is indicated by software integrated into the processing system. During its lifetime, the electrolyte medium accumulates with the removed workpiece material. Once it is saturated, the process medium can be disposed of comparatively easily using standard services. As it is a solid, there is no risk of contaminating wastewater. The DryLyte process also produces no harmful vapours or dust, as is the case with conventional electropolishing and manual grinding and polishing. Special protective equipment for personnel is therefore not required.
The most important advantages of the DryLyte process at a glance
- Precise surface processing - made possible by the accuracy of the material removal, ideally suited for sensitive parts.
- Versatile - smoothing, deburring, polishing and AM post-processing in one process.
- Reduced footprint - DLyte systems have a high output and save space compared to conventional systems.
- Cost reduction - According to the development company GPAINNOVA, the process leads to a reduction in production costs of over 60%.
- No emissions - As neither dust nor toxic vapours are produced, personnel are not exposed and do not need protective clothing.
- Consistent processing results - the process agent works reliably and without any loss of quality right up to the lifetime limit.
- High processing speed - between a few minutes and up to 1.5 hours, depending on the initial roughness and the desired result.