
Spiegelglanz für hochwertige Schmiederäder in weniger als 40 Minuten
Einerseits ist es ein geringes Gewicht bei gleichzeitig hoher Stabilität und Belastbarkeit, andererseits die exklusive Optik, weshalb insbesondere OEM aus dem Premiumsegment ihre Fahrzeuge auf geschmiedeten Aluminiumrädern über die Straßen rollen lassen. Zu den optischen Merkmalen der Felgen zählt nicht nur ein ansprechendes Design, sondern erst eine makellose Hochglanz-Politur sorgt für einen perfekten Gesamteindruck. Dafür werden diese üblicherweise vor- und feingeschliffen sowie poliert. Erfolgen diese Prozesse in klassischer Vibrations-Gleitschlifftechnik oder gar in „unbezahlbarer“ Handarbeit, sind dafür Bearbeitungszeiten von mehreren Stunden erforderlich. Diesen enormen Zeitaufwand wollte ein renommierter Felgenhersteller auch bei der partiellen Bearbeitung bereits lackierter Bicolor-Felgen deutlich verringern und suchte eine Bearbeitungsalternative. Fündig wurde das Unternehmen mit der Tauchschleifanlage R 1/1 TSA-O/VS-So. Tauchschleifen wurde von Rösler für das reproduzierbare und schnelle Entgraten, Kantenverrunden, Schleifen und Polieren von komplex geformten, schweren und empfindlichen Werkstücken entwickelt.
Zweistufiger Prozess mit abgestimmten Verfahrensmitteln
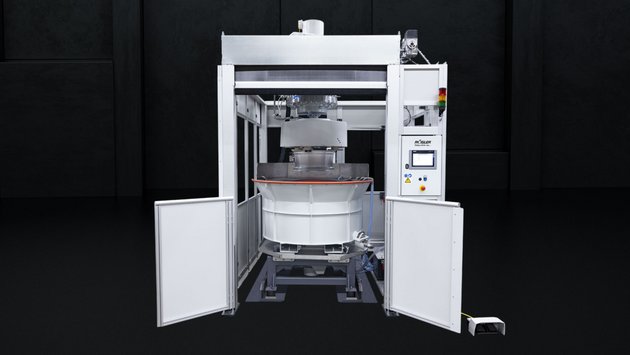
Besonders herausfordernd bei dieser Aufgabenstellung war die Prozessgestaltung – einerseits darf die Lackierung nicht beschädigt werden, andererseits muss auf den zu bearbeitenden Flächen ein brillanter Hochglanz erzielt werden. Die Felgen werden dafür mithilfe eines pneumatischen Spannsystems an der Arbeitsspindel der Tauchschleifanlage befestigt. Das Befestigungssystem wurde so ausgelegt, dass die Beladung sowohl manuell als auch automatisiert mit einem Roboter erfolgen kann. Die rotierende Spindel taucht das Rad in einen feststehenden Arbeitsbehälter ein. Das Vorschleifen erfolgt mit speziell von Rösler für diese Anwendung entwickelten und gefertigten, kegelförmigen Kunststoffschleifkörpern sowie einem abgestimmten Compound in einem Nassprozess. Während der Bearbeitung führt die Spindel zentrische, orbitale und reziproke Drehbewegungen durch, die auch kombiniert werden. Durch diese Bewegungsabläufe ist sichergestellt, dass selbst in feinsten Details der Räder reproduzierbar ein homogenes Schleifergebnis erzielt wird. Gerade die Reproduzierbarkeit der Oberflächenergebnisse ist eine zentrale Anforderung an einen großserientauglichen Prozess. Einen wesentlichen Beitrag dazu leisten auch der Vibrationsmotor am Arbeitsbehälter und die integrierte Unterkornaussiebung. Beides sorgt dafür, dass mit einem Schleifkörpergemisch in konstant guter Qualität gearbeitet wird. Nach einer Feinschleifbearbeitungszeit von rund sieben Minuten werden die Räder für das Hochglanz-Polieren in eine zweite Tauchschleifanlage umgesetzt, die mit einem Porzellanmedium befüllt ist. Die Bearbeitungszeit bei diesem Prozess liegt bei 25 bis 30 Minuten.
Ressourcenschonender Einsatz von Wasser und Compound
Für einen wasser- und compoundsparenden Betrieb der Anlagen wurde eine chemische Wasseraufbereitungsanlage integriert. Sie wird für die Aufbereitung der nur gering verunreinigten Flüssigkeit aus dem Feinschleif- und Polierprozess eingesetzt. Das vom Polierprozess anfallende und zwischengepufferte Prozesswasser wird für den Vorschleifprozess nochmals genutzt. Der für die Prozesse benötigte Compound wird bedarfsgerecht jedem Prozessschritt automatisch zudosiert und kann dadurch auch beim Vorschleifen ein zweites Mal genutzt werden.
Überzeugt ist das Unternehmen sowohl von der Technik als auch der Wirtschaftlichkeit der Tauchschleifanlagen. Dies wird nicht zuletzt daran deutlich, dass für die nächste Ausbaustufe der Felgenbearbeitung bereits weitere Anlagen bestellt wurden.