
Surface Finishing for Die Castings, Part 2 – Enhancing Results with Optimizations
, Matthew Wesner - Zurück zur Übersicht
From deburring and smoothing to cleaning processes, surface finishing systems for die castings can often be optimized with automation, recycling, and consumable upgrades.
Whether your process involves mass finishing or shot blasting, many surface finishing operations for die castings can be augmented with modern technology and products to increase efficiency.
With more than 80 years of experience, Rösler has the experience to optimize your system and improve results by integrating automation, process liquid recycling, enhanced consumables, and more.
Automation
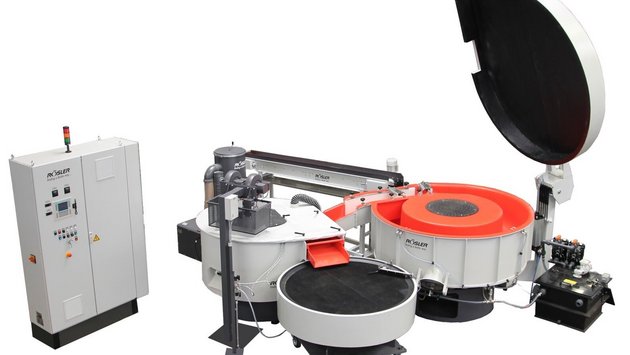
Beyond the reduced reliance on manual labor, automation presents manufacturers and processors with an ability to provide more consistent, repeatable results over manual finishing operations.
When it comes to smoothing and polishing, automation greatly increases the quantity of available processing as well.
Depending on the component or part size and machine process type, hundreds or even thousands of parts can be processed simultaneously. Automation also reduces idle times between processing batches by reducing loading and unloading times for batch processing or allowing a continuous feed of raw work pieces for constant processing.
Today, automation of any process equipment is an economic factor, including process control, handling, quality, inspection, repeatability, and reliability in integrated turnkey solutions.
Process Liquid Recycling
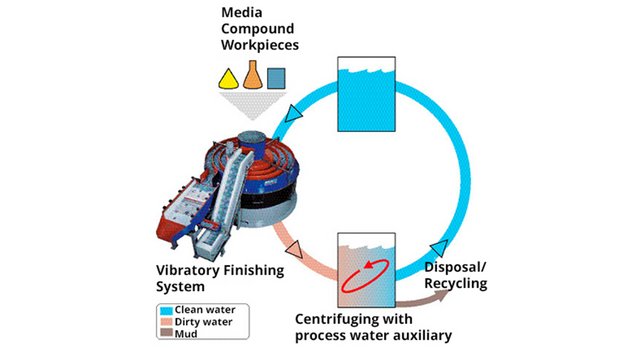
Vibratory finishing operations require the use of water and compounds.
Besides deburring and edge breaking the process offers a washing and cleaning effect. Modern recycling systems allow the reuse of the water/compound mix.
This reduces the water and compound consumption to a minimum, and with the addition of a wastewater centrifuge, the compound and water can be used repeatedly before final discharge.
In addition to the considerable cost savings on water and compound, the ability to reuse process water helps to keep the environment clean and reduces the costs of discharging excessive amounts of waste through a local authority.
Enhanced Consumables

Sometimes the finishing equipment itself is fine as is, yet an adjustment in the type of compounds and/or media used can optimize results.
For example, excessive foaming may occur during the finishing process, creating a buffer between work pieces and the media, thereby reducing the grinding effect. While the machine is still doing its job, the water and media interactions are reducing process efficiency.
The cause of foaming in mass finishing machines is often water hardness. By switching to a new, non-foaming plastic media known as N-media and utilizing a process water additive, the operation can regain its intended process stability and productivity.
Since the non-foaming media version is identical to standard plastic media in identical shapes, sizes, and grinding performances, it can be swapped in without finishing process modifications.
In fact, the non-foaming consumables used in conjunction with automation can successfully improve the cleanliness of die castings to a point where the work pieces no longer need to undergo an additional part washing step after the mass finishing process.