
Plastic Deflashing, Part 2 – Formation of Flashes & Removal Methods
, Matthew Wesner - 回到概览
Plastic deflashing is crucial for component safety and function. To remove this excess plastic after the molding process, mass finishing and shot blasting offer efficiency.
Similar to metal pieces, components made from plastic must also undergo a post-production treatment before they can be utilized or further processed in downstream manufacturing operations. An extremely important post-processing step for plastic pieces is deflashing.
This process is frequently combined with the removal of sprues and, if multi-cavity molds are used, the removal of runners and gates between molds.
Rosler understands the need for fast and efficient processing. Our ability to deliver precise deflashing stems in part, from our understanding of how flash and sprues are formed and the various removal methods.
Formation Causes
Flash forms during the molding process when material leaks between the edges of the two mold halves. The edges where the two molds meet are known as the parting line.
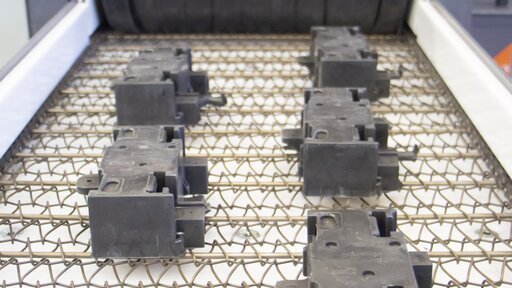
The source of leaks along the parting line may occur as a result of:
- Wear from consistent mold use. Over time, the mating surfaces may not perfectly fit one another anymore.
- Lacking a precise fit for very complex pieces. If the fit of mating surfaces is not precise enough, small gaps may form.
- Thermal and mechanical stresses in the molds. During the injection process, these stresses can cause small gaps between mating surfaces.
- Poor maintenance and mold inspections, causing material leakage.
Importance of Deflashing
Plastic components must be deflashed as a pre-treatment measure before they can be used or further processed in subsequent manufacturing or assembly operations.
If this indispensable step is skipped, residual plastic material may:
- Break off during assembly or operation of a component and render it unusable.
- Cause serious problems with automatic assembly operations.
- Impair the appearance of visible, decorative components.
- Impede component functionality.
- Risk injuring handling personnel or the eventual user.
Methods of Removal
While deflashing molded plastic components is required across the board, the method of removing extra plastic flash varies.
For every deflashing task, two important factors must be considered. First, is production volume. Are only a few pieces produced or is high-volume production required?
Secondly, what type of plastic is used to form the components? Is the material hard with low plasticity, or is it relatively soft and has high plasticity?
Considering how many pieces need processing as well as the characteristics of the specific plastic will help select the most appropriate processing method.
Users can choose from different deflashing systems, including:
- Manual deflashing – In the case of low-volume production, for example, when only prototypes are produced, deflashing with knives and scrapers may be the best option. For larger volumes though, manual operations are time-consuming and not cost-effective.
- Cryogenic deflashing – In this method, parts are cooled to a temperature of -40 °F (-40 °C) using liquid nitrogen. The sub-freezing temperature causes thin flash areas to become brittle. Through intensive tumbling or a combination of tumbling and blasting, brittle flash breaks off while leaving the part intact. This method is useful in processing softer plastics with relatively high plasticity, such as elastomer and standard thermoplastic products including tires, silicone baking molds, and polyurethane components.
- Dry ice blasting – CO2 pellets with a temperature of –100 °F (-79 °C) are accelerated and propelled against plastic components. This method is primarily used for surface cleaning, but in the case of very thin flash, it can also be used to deflash elastomers and some thermoplastics.

Mass Finishing & Deflashing
In mass finishing, intensive mechanical rubbing between abrasive media and the work pieces removes flashes, but it doesn’t stop there. It also grinds off the excess material from the parting line for a perfect finish; sometimes mass finishing even creates a polished surface finish.
Mass finishing is equally suitable for aggressive, highly intensive deflashing and deburring as well as gentle surface smoothing and polishing of delicate components.
The application lends itself to use with all kinds of plastics. For elastomers with typically high plasticity, mass finishing is an excellent alternative to cryogenic deflashing and dry ice blasting. Common applications include deflashing rubber components like O-rings and deburring, surface smoothing, and polishing eyeglass frames, buttons, and plastic handles.
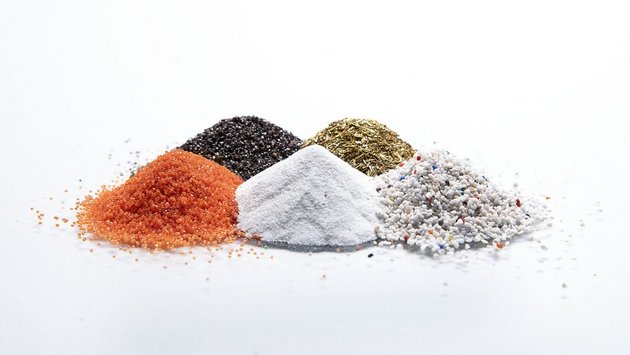
Shot Blasting & Deflashing
By bombarding work pieces with media at speeds of >300 ft (90 m) per second, shot blasting’s impact energy breaks flashes off without affecting the integrity of the component body.
Plastic pellets composed of polycarbonate, polyamide, or polystyrene or organic media like walnut shells range in size from 0.008 to 0.06 in (0.2 to 1.5 mm).
Applications for shot blasting include relatively hard plastic components with low plasticity, such as duroplastics and high-performance thermoplastics with high fill rate or re-enforcing materials like glass fiber. Commonly shot blasted pieces include many kinds of electrical hardware and automotive components, handles, and frames for electronic components.
For large volumes of duroplastics and high-performance thermoplastics, shot blasting technology is the most productive, cost-efficient, and reliable deflashing technology.
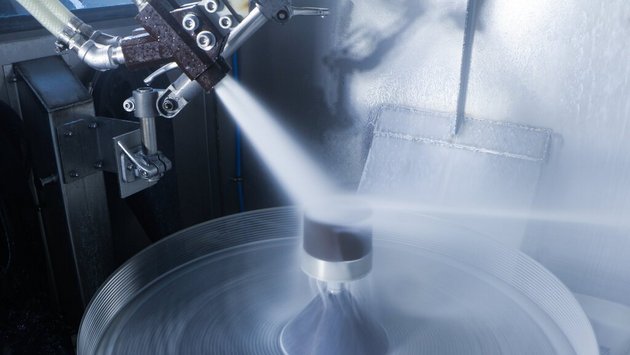
Mold Maintenance
In addition to processing the components created by plastic molding, mass finishing and shot blasting can also help keep injection molding systems in good working conditions. Mass finishing and shot blasting (primarily wet blasting) can be utilized to clean injection molding machine components including augers, injection nozzles, and the actual injection molds.
The Rosler Way
Deflashing, like most surface finishing applications, is not one-size-fits-all. Whether you're undertaking a totally new process or looking to improve the output of an existing operation, Rosler can help.
Contact us to discuss your deflashing needs or to request a free processing trial in one of our Customer Experience Centers.
The Plastic Deflashing series began with Plastic Component Advantages & Types.
It will continue with:
- Part 3 – Turbine Versus Air Blasting.
- Part 4 – Shot Blasting Machine Features.
- Part 5 – Machine Selection & Options.
- Part 6 – Automation & Digitization.
- Part 7 – Consumables.