Rösler Russia
Borovaya Str. 7, bldg. 4, office 107
111020 Moscow - Russia
+7 495 247 55 80
+7 495 247 55 80
rosler-ru@rosler.com
Rösler OberflÀchentechnik GmbH has been active in the Russian and CIS markets for over 40 years and has worked successfully with over 100 customers from all areas of industry.
Since our Rösler Russland site opened in Moscow in 2009, we have been able to serve our customers even more efficiently and we are available to support you with any questions. We offer a comprehensive service, from advice and sales through to commissioning machines, servicing and support. At our test center in Moscow, we develop customized processes and provide process testing and subcontracting services. In our warehouse, we stock an extensive range of replacement and consumable parts as well as consumables for all machines.
Our customers in every sector have an experienced, highly skilled and motivated team at their side. We support you with project development and are here to help with any questions or problems.
Our service for you directly on site
-
After Sales & Service / Spare parts
-
Customer Experience Center
-
Automation
-
Subcontracting
Finding a better way ...

After Sales & Service / Spare parts
Our service experts offer professional visits and service agreements, which we tailor to your machine and rate of usage. We are also happy to provide suggestions for improving your processes and tips on maintaining, repairing and overhauling your machines. Our TuneUp service also offers you the opportunity to upgrade your current machines.
With a large stock of spare parts and consumables in our logistics center, we can guarantee availability of parts and quick delivery.
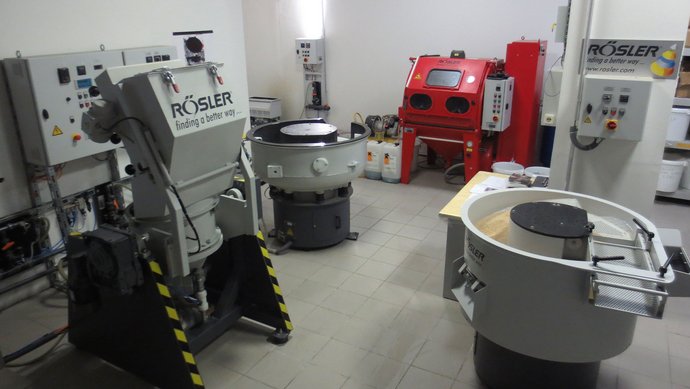
Customer Experience Center (CEC)
Our CEC is equipped with mass finishing systems, shot blasting machines, centrifuges for process water treatment and post-processing machines for 3D parts. We are able to determine the best process for finishing parts and treating process water. In addition, we can assess and demonstrate these results through our in-house measurement laboratory.
The R&D department is fully integrated in our businesses processes and can support special developments, helping to promote innovation and continuous improvement.

Automation
One of our main activities is the manufacturing of automated systems, and our highest priority is fulfilling our customersâ project requirements.
Our engineering department works with the latest drawing tools and tests the viability of every project to demonstrate possible solutions to the customer with regard to parts handling, linking machines and the proposed software.

Subcontracting
Our site features a workshop that is specially set up for carrying out subcontracting services. With our own full range of machines for vibratory grinding, shot blasting, air blasting and AM solutions, we can offer services in our usual top quality to support you with short-term additional production requirements, pre-series production or the outsourcing of production runs without the need to invest in a machine.