
Structural Steel FAQ, Part 4 – Evaluating the Presence of Dust
, RoslerUSA - Back to overview
Measuring dust on steel prior to processing helps determine surface cleaning and preparation needs. Proper preparation before painting and coating improves adhesion and lifespan.
The Dangers of Dust
Blast-cleaned structural steel surfaces must be completely free of dust to ensure proper coating and painting.
Residual dust will reduce the adhesion of subsequently applied coatings and, by absorbing moisture, may promote the corrosion of the blast‐cleaned steel surfaces. The potential accumulation of dust is especially critical on horizontal surfaces, the interior of pipes, and in structural cavities.
Special inspections must be carried out to ensure that such areas are adequately cleaned and free from dust before painting.

Standards of Assessment
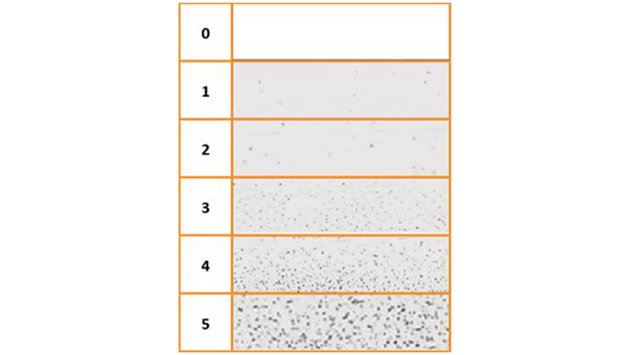
The most common standard of assessment for dust is ISO 8502–3:2017. Also known as the pressure‐sensitive tape method, this ISO standard describes a procedure to test shot-blasted steel surfaces for dust and provides a reference description and photo with six dust ratings for comparison.
On a scale of 0 to 5, the observation of dust particles and diameter are rated as follows:
- 0 – No particles visible under 10x magnification
- 1 – Particles are visible under 10x magnification but not with normal or corrected vision, usually particles less than 50 μm in diameter
- 2 – Particles are just visible with normal or corrected vision, usually particles between 50 and 100 μm in diameter
- 3 – Particles are clearly visible with normal or corrected vision, particles up to 0.5 mm in diameter
- 4 – Particles are clearly visible, between 0.5 and 2.5 mm in diameter
- 5 – Particles are clearly visible, larger than 2.5 mm in diameter
Testing for Dust
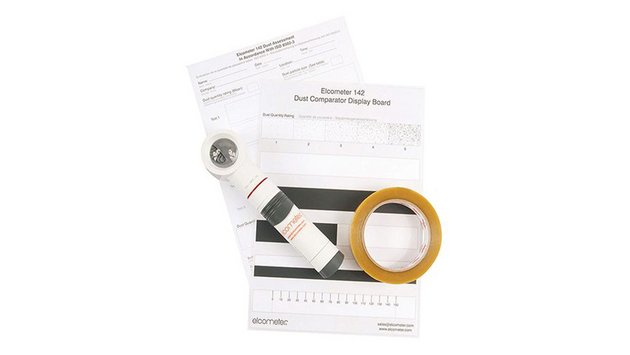
This sample test kits include a 10x magnifier, adhesive tape to ISO 8502‐3 specification, comparator display board/operating instructions, a dust assessment plate, and 25 test record sheets.
Proper procedure is required to accurately test for ISO 8502-3 using the kit.
- Remove a piece of tape about 200 mm (8”) long.
- Place the sticky side of the tape onto the test surface; rub along the length of the tape using constant pressure several times.
- Pull the tape away from the test surface, then compare the dust on the tape with the comparator display board and record the estimated dust rating number.
- Repeat the test at least three times on the surface being investigated.
Minimum Requirements

The dust test per ISO 8502‐3 is subjective and does not allow the precise determination of dust on a blast cleaned surface, but the rating can be a very useful approximation when carried out by experienced operators.
Painting schedules usually call for shot blasted surfaces prior to painting to be free of dust. A generally accepted rule stipulates that the particle quantity and particle size do not exceed rating 2 of ISO 8502‐3.
Removing Residual Dust
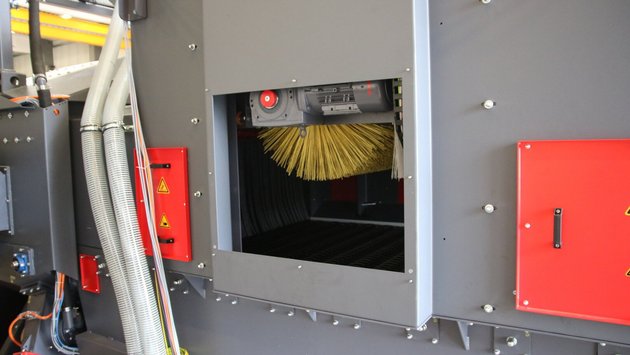
To remove residual blast media and dust from the work pieces, shot blasted steel components are usually passed through a blow‐off station. These stations are frequently combined with a brush‐off system.