
Orthopedic Implants, Part 7 - Processing Technology Evolves with Industry Advancements
, A.Altmann - Back to overview
Due to their precision, efficiency, and economy, mass finishing and shot blasting are an indispensable part of the finishing process for a wide variety of orthopedic implants in different manufacturing stages.
These flexible machines and the Rosler process technology can handle general cleaning; deburring; surface smoothing after casting, forging, stamping, machining, and heat treatment; surface preparation for polishing or coating operations; and to create the final finish on all kinds of implants and medical devices.
With an experienced partner such as Rösler, these processes are also capable of adapting to emerging trends with proper testing and processing trials.
Evolving Technology & Outlook
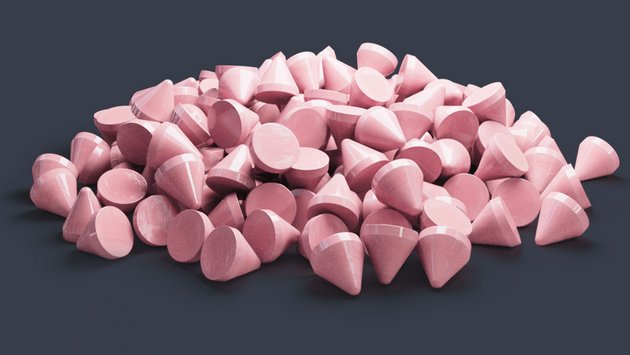
Orthopedic implant OEM’s & sub-contractors are at the cutting edge of medical technology. New materials and manufacturing techniques and technologies are constantly evaluated to improve the performance and longevity of the implants and reduce the manufacturing cost. Two examples are the increased use of ceramics as base material or coating and additive manufacturing.
These new materials present new challenges for finishing equipment because of the material properties and/or starting conditions. Suppliers of mass finishing and shot blasting equipment and consumables have met these challenges head-on by modifying existing equipment designs or developing brand-new machinery. However, the biggest progress has been made in the field of mass finishing media.
There is now media on the market that allows to achieve a high-gloss finish on components made from cobalt-chrome or titanium, after CNC grinding and milling. These media even allow mirror polishing of ceramic work pieces. Likewise, 3D printed components can be finished from initial surface readings of >2,000 micro inches (30 μm) down to less than 2 micro inch (> 0,05 µm !!).
Testing & Trials
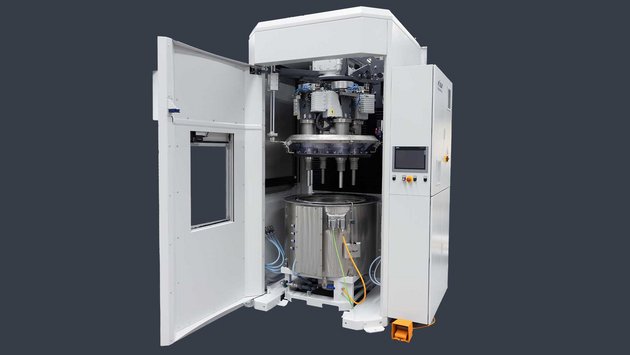
In many cases, the optimum manufacturing process includes multiple production steps. Working with experts from the device manufacturer and the finishing system supplier will ensure that the entire production process is considered when finding the optimum solution. It might be possible to reduce the cycle time in a previous higher-cost production step to a lower-cost finishing step without jeopardizing the final product.
At Rösler, we understand the rigorous requirements for orthopedic implants and are well suited to help you achieve your goals through a better finishing process and an integrative approach.
Our systems and processes are tailor-made, both to the respective processing requirements as well as to their optimal placement in the production sequence. Rösler Group test centers around the globe are equipped with the latest in systems engineering.