
Rösler is continuously searching for ways to improve the finishing technologies utilized within the medical industry. One of the most valuable solutions offered is the R 6/1000 SF Drag Finishing System which provides perfect mass finishing to orthopedic implants with its exact drag finishing technique.
How it Works

Drag finishing technology is ideal for treating high-value, delicate work pieces with complex shapes, for example, endoprosthetic components. Individually attached to special work piece holders, the work pieces are mounted to rotary workstations/spindles and “dragged” through a stationary processing bowl filled with grinding or polishing media. This allows a highly precise, targeted finishing operation. Compared to conventional vibratory systems, drag finishers produce up to 40 times higher processing intensity.
Machine Specifications
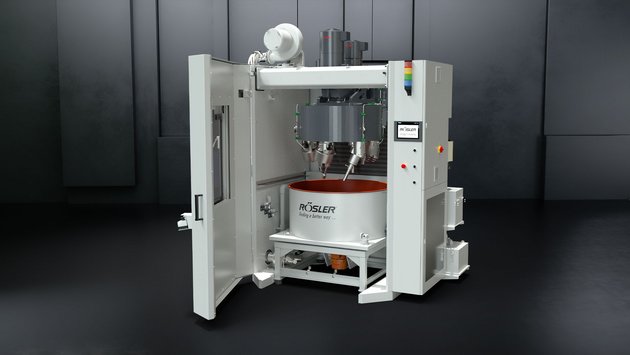
The R 6/1000 SF is ideal for high-quality, delicate, and complex work pieces. It can also handle large and heavy components. Each machine is equipped with four multi-purpose work stations, allowing for batch processing in a single work bowl with a diameter of 43 in (1080 mm). The machine’s overall size is 7.5 ft long, 7.9 ft wide, and 11.5 ft high (2.3 x 2.4 x 3.5 m).
Intelligent process controls enable the R 6/1000 SF to produce consistent results from batch to batch as well as automation and integration into production cells. The system can also be configured to combine processing steps, such as pre-grinding, fine grinding, and polishing.
Process-Steps for Implants
Smith+Nephew relies on Rösler equipment

The R6/1000 SF drag finishing system is used worldwide in medical technology - for example at Smith+Nephew, one of the 20 companies with the highest turnover in the industry with around 18,000 employees in over 100 countries. In its new, high-tech plant in Penang, Malaysia, S+N relies on two production cells, each with three R 6/1000 SF drag finishers from Rösler, to process knee implants made of cobalt-chrome alloy.
The drag finishers consist of a processing bowl with a diameter of 1,000 mm and a carousel with six rotary spindles. These are equipped with specially designed work piece fixtures, to which the femur components are mounted. The design of the fixtures allows clamping of the work pieces in a position that allows the finishing of precisely defined surface areas. Thanks to an optimised workpiece holder, 18 parts can be machined at the same time - resulting in around 50 percent higher productivity. The systems are operated with media classification systems. They work in combination with two fully automatic Z 1000 centrifuges for process water treatment and the Rösler Smart Solutions digitalisation software. This innovative monitoring solution enables the monitoring, recording and evaluation of up to 14 individually selectable process parameters and provides recommendations for action if these values deviate from the target. RSS also facilitates the seamless recording of process data and is helpful as proof of process quality and stability in quality audits and for documentation purposes.