
Plastic deflashing part 4 - System characteristics and features for optimal machining results
, A.Altmann - Back to overview
Vibrating screening machine for removing broken off burrs from the blasting system
Depending on the extent to which the raw parts are affected by burrs, sprues and overflows, it is advisable to carry out rough pre-deburring, e.g. using a rotating screen drum or shearing, before feeding them into the blasting system.
Burr fragments, sprues etc. that are not promptly removed from the blast media lead to increased system wear and can also cause blockages in the blast media circulation.
Blasting systems must be equipped with an effective blast media cleaning system to ensure good and economical deflashing results in the long term. This usually also includes a powerful vibrating screening unit.
Air flow separator - an effective system for fine blast media cleaning
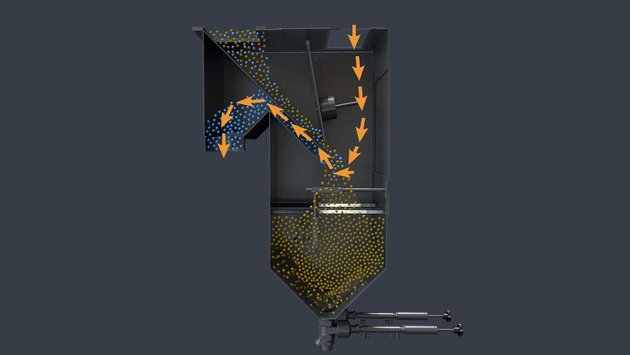
After the burrs have been blasted off the workpieces, the blast media introduced by the turbines and blasting nozzles is contaminated with burr parts, particles of the filling material (e.g. glass fibres, carbon fibres, mineral powder), blast media attrition and dust, but also blast media grains that have become too small. All these impurities must be reliably removed before the blast media can be fed back into the respective blasting unit. Bigger impurities are discharged via the vibrating screening machine described above. However, in order to ensure a constant blast media operating mixture, the finer impurities must also be permanently removed from the system.
Also for plastics deflashing with blasting technology this is implemented in most blasting systems - with the exception of small (manual) blasting cabinets - using so-called cascade air flow separators. In such a cascade air flow separator, the contaminated blast media trickles as a thin curtain towards the blast media storage hopper.
An air flow is generated via the connected filter unit, which penetrates the blast media curtain. The air flow picks up the finer impurities which still are in the blast media and carries them out of the blasting machine towards the filter unit. The cleaned blast media remains in the blasting system, ready for the next pass through the blasting turbine and/or the blasting nozzle.
Antistatic dosing system, blow-off device and dust separator:

Avoidance of dust and blast media deposits and adhesions on the blasted workpieces
The discharge of dust and blast media grains adhering to the workpieces poses a not insignificant problem for the subsequent handling and functionality of plastic workpieces. Such adhesions can be caused, for example, by âscoopingâ workpiece areas, jamming, but also by electrostatic effects.
In order to prevent the almost âglutinousâ effect of static electricity, it is necessary to spray a special antistatic agent aerosol-like into the blasting chamber at regular intervals. This is done using a sophisticated dosing system. The absolute quantity is precisely mapped by the timing functions of the PLC control system via the frequency and duration of the spray pulses. The refilling of the corresponding storage hopper with a reproducibly constant mixing ratio of active agent concentrate and water can also be automated via the PLC control system.

In addition, plastic deflashing systems also have a blow-off system. After the actual blasting process, compressed air nozzles or electric blowers are adjusted to ensure that dust and blast agent residues are removed from the surface of the workpieces before they leave the machine.
Dust is also inevitably produced when blasting plastic workpieces. Ideally, this dust should be removed from the blasting system as soon as possible before it can sediment inside the machine and on the workpieces. This is achieved via the dust separator adapted to the respective blasting system and application.
In addition to the above-mentioned blast chamber exhaustion and cascade air flow separator, the filter unit is a key element here. These filters are specially equipped for the separation of plastic dust.
The filter unit, usually a dry cartridge filter, initiates the exhaustion of dust-laden air from the blasting system. Highly efficient filter elements inside the filter remove the dust from this air. The residual dust content in the air is so small that the cleaned air can remain in the production hall and does not have to be discharged outside.
Refilling the used blast media through automatic blast media replenisher
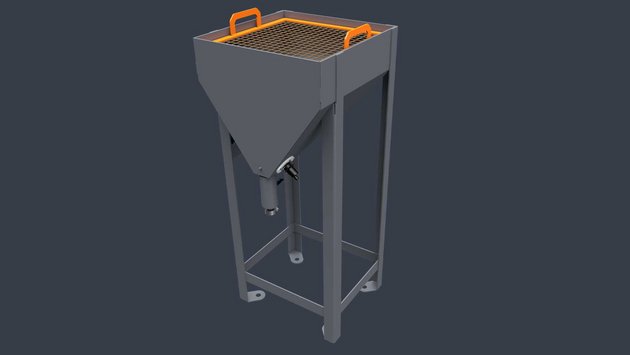
An essential precondition for consistently good deflashing results is a stable blast media operating mixture.
Blast media is a consumable. Abrasion reduces the size of the blast media grains and thus also their blasting effect.
Blast media that has become too small is discharged from the blasting system via the blast media cleaning system (cascade air flow separator, screening device, blasting chamber exhaustion and filter). To compensate for this discharge, new blast media must be refilled regularly.
This is usually done with an automatic blast media replenishment system. Whenever a sensor in the storage hopper signals that the blast media level is too low, the refill system opens a valve. As a result, new blast media flows into the blasting system in small portions from a separate storage hopper.
This ensures that there is always a sufficient volume of blast media in circulation in the blasting system and that the grain size composition of the operating mixture remains constant. And this in turn ensures a permanently stable deflashing result on the workpieces.