
Plastic deflashing Part 3 - Advantages and limitations of turbine and injection blasting
There are two main blasting processes available for deflashing plastic components, primarily made of thermoset and special thermoplastic materials: Turbine blasting, which is extremely effective over a large area, and highly efficient punctiform acting injection blasting.
Both processes are also used in conventional blasting systems for metal processing. In contrast, plastic deflashing is a much gentler processing method, particularly due to the selection of non-abrasive blasting media.
Which blasting process is selected for plastic deflashing depends on various factors. These include the production volume and the question of whether bulk material processing is possible or whether the parts are of a type that requires individual part processing. Another criterion is the question of whether the parts are to be partially or completely blasted and which blast media grain size and blast media speed are required.
Turbine blasting
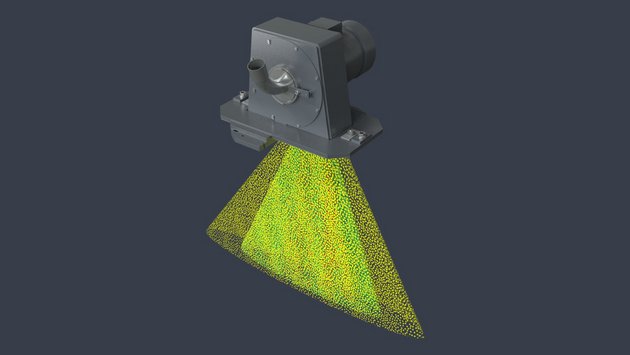
Turbine blasting is the most effective and fastest way to deflash plastic parts. In this process, the blast media is propelled onto the workpiece via a turbine or blasting wheel. The maximum throughput rate when using plastic blast media for turbine blasting is 20kg/min. The turbine itself consists of a rotating wheel that spins at up to 4,500 rpm and is equipped with a series of throwing blades. The blast media accelerated by the turbine produces a so-called blasting pattern (impact area) of around 100 x 500 mm (depending on the distance to the workpiece).
Different exit speeds and kinetic energy of the blast media grain are required for deburring plastic parts, depending on the flash situation and blast media grain size. Up to 70 m/s can be achieved with the turbine, up to 90 m/s with special drives. With pressure blasting (for plastics deflashing usually injection blasting is used), media speeds of up to 60 m/s can be achieved. Turbine blasting is characterised by a very low, specific energy requirement and a high degree of efficiency.
Turbine blasting is generally considered to be the most economical blasting method for large quantities of plastic parts made of thermoset and some types of thermoplasts. This process shows a very good dosability of the blasting energy (blast media volume and release speed). Turbine blasting has limitations or restrictions when it comes to deflashing geometries that are difficult to access, such as small openings and shaded interior areas. Relatively small blast media grain sizes (approx. < 0.5 mm) can only be used to a limited extent with turbines. Injection blasting can be used as an effective alternative in these cases.
Injection blasting

Injection blasting is less effective than turbine blasting, especially in terms of surface area, because the blasting pattern of an injection blasting nozzle only reaches a diameter of around 20-25 millimetres, depending on the distance to the workpiece, and the blast media throughput is a maximum of 2 kg/minute when using a plastic blasting medium. On the other hand, this method can be used for more targeted work and the procurement costs of the systems are comparatively low, especially for beginners.
With injection blasting, the blast media is conveyed by means of compressed air and directed through the blasting nozzle onto the workpiece at a final accelerated speed. It reaches a speed of up to 60 m/s. In addition to the actual exit speed, the blasting effect of the injection nozzle is positively influenced by the fact that the compressed air flow accompanies the blasting media grains to the workpiece, which minimises the loss of speed of the blast media. Although less effective over a large area than turbine blasting, injection blasting can achieve a very high level of efficiency at specific points. This is particularly advantageous when flashes need to be removed in areas that are extremely difficult to access.
Injection blasting systems are often lower in investment than turbine blasting systems, which are often also significantly larger. Due to the relatively high consumption of compressed air as energy source, injection blasting is generally more cost-intensive than turbine blasting in relation to the achievable production volume. Nevertheless, the process is indispensable for processing smaller series, more complex geometries and sensitive parts.
Plastic deflashing machines
The Rösler RMBC-S tumble belt blast machine, the Rösler RMTS multi-tumbler, the Rösler RSAB wire mesh belt blast machine and the Rösler RSBS loop belt blast machine are equipped with turbines as standard. Depending on customer requirements, the Rösler swing chamber system RWS is available with a turbine, with nozzles or even with a combination of both shot blasting systems.
Pure nozzle blasting installations are e.g. the Rösler blast cabinet RSKI and the Rösler satellite table blast machine RSA. Depending on customer requirements, the Rösler swing camber system RWS is available with a turbine, with nozzles or even with a combination of both shot blasting systems.