Unlimited applications â no matter what your requirements
Rösler mass finishing offers more than 1,000 surface finishing options.Metal, plastic, ceramic or wood, deburring, descaling, rust removal or polishing â the uses for mass finishing machines are almost limitless and they have been used successfully day in and day out for decades in many industries such as aerospace, medical technology, the automotive sector and the coin and jewelry industries. Nowadays, almost every workpiece requires functional or aesthetic surface finishing.
Mass finishing, also referred to as tumbling or vibratory finishing, is a technique derived from nature â surfaces are polished using grinding media and compounds in the same way that sand and water smooth pebbles in the riverbed.
Mass finishing offers a big advantage over other competing methods. By combining processes, several production steps can often be carried out simultaneously. As a result, processing time is reduced, fewer resources are used and it is more cost-effective.
Everything you need from a single source â our offer to you
As the market and technology leader in the field of vibratory finishing, we have an almost unlimited selection of different mass finishing machines and technologies. Our range includes robust all-rounders, such as the well-established rotary vibrator, fully-automated high-precision machines, such as our drag finishing machines and Surf-Finisher, as well as fully automated linked systems.
Choosing equipment from Rösler isnât the end of your journey with us. Our Rösler complete service provides all the components, peripheral solutions and services you need â optimized and individually adapted to your requirements.
This includes:
- A choice of approx. 15,000 consumables developed and produced in-house
- Dedicated peripheral equipment, such as sustainable drying solutions, resource-saving centrifugal technology, and industrial washing systems
- Digital monitoring of process water for more reliable and cost-effective processes
- Expert advice and extensive testing in our worldwide Customer Experience Centers
- Individually tailored servicing contracts
- Worldwide support from our own service and application engineers on site
- Training and professional development opportunities for your employees in our Rösler Academy
- State-of-the-art manufacturing sites with a unique in-house production range
We offer everything you need from a single source â Rösler. This makes us unique and you successful!
Professional & individual â we develop your custom process

Letâs compare mass finishing to the familiar art of cooking: Simply using the right ingredients, doesn't make you a great chef. It is only by combining experience with the right quantities of individual ingredients that we achieve the desired result. Mass finishing works in just the same way.,
Here at Rösler, we draw on our extensive experience gathered over the past 90 years in the mass finishing sector â experience which you naturally benefit from. We have consistently developed our process know-how by performing hundreds of thousands of tests for a wide range of industries in our worldwide Customer Experience Centers. True to our company motto âfinding a better wayâ, we aim to give you the competitive edge in terms of quality and profitability. Whether you're looking for a standard process, a special solution or highly automated production cells, your surfaces are in the best hands thanks to our globally unique product range.
Dynamic, sustainable, economical â added value thanks to Rösler
Many mass finishing processes and machines used today throughout the world have been customized by us to meet specific customer requirements.
When it comes to the post-processing of complex, high-quality precision parts, many high-tech industries rely on the Rösler Surf-Finisher. Its six-axis articulated robotic arm enables the reliable, cost-effective and repeatable post-processing of workpieces which until now still had to be partially finished by hand.
From the point of view of resource conservation, using process water in an environmentally responsible way is becoming increasingly important. Thanks to our continuous development of machine technology and consumables (finishing media, compounds and process-water cleaner), today almost any mass finishing equipment can be connected with a Rösler process water system.
The process water resulting from vibratory grinding is then fully recycled via a closed-loop system. This process can be monitored around the clock and from any location using the digital process water management system from our new brand, Rösler Smart Solutions. It also quickly and simply provides you with the best recommended courses of action, if required.
We have also taken another step toward increased sustainability in mass finishing with our RT Euro-DH rotary dryer. This latest model impresses with its newly developed heating blocks, which enable energy savings of up to 40 percent and thereby make vibratory grinding solutions more environmentally friendly and sustainable.
What are the key points about mass finishing?
A look at frequently asked questions.
Mass finishing, trowalizing and vibratory finishing are different terms that describe the same technology, namely the mechanical surface finishing of components. This technology is using polishing or grinding media (frequently also called âchipsâ or âtumbling stonesâ) and, usually, a liquid additive (a mix of water and a chemical compound) in special equipment such as vibratory, centrifugal force or drag/surf finishing machines. A similar process is tumble finishing, in which the material is removed without vibration and only by a rotational movement.
During mass finishing process, the machines set the media and work pieces in motion causing a constant ârubbingâ action. The resulting â more or less pronounced â abrasion removes material from the work piece surface and, thus, produces the desired deburring, smoothing, polishing or cleaning effect.
Mass finishing is employed across a wide range of industries. For example, it is used for treating single large components, such as automotive wheels or large ship propellers. But it is equally effective for the consistent, economical and easily controllable surface finishing of large batches of smaller work pieces.
In the most common finishing machines the motion of media and work pieces is induced by vibration: Together with suitable grinding or polishing media, made from plastic or ceramic, the raw, untreated work pieces are placed into a round or rectangular processing bowl. An electric motor with attached imbalance unit(s) induces a vibration into the bowl and causes the constant rubbing of the media against the work pieces. This results in the removal of material from the work piece surface. Through the addition of, mostly, liquid chemical compounds additional surface effects like corrosion protection, degreasing or general cleaning, can be achieved.
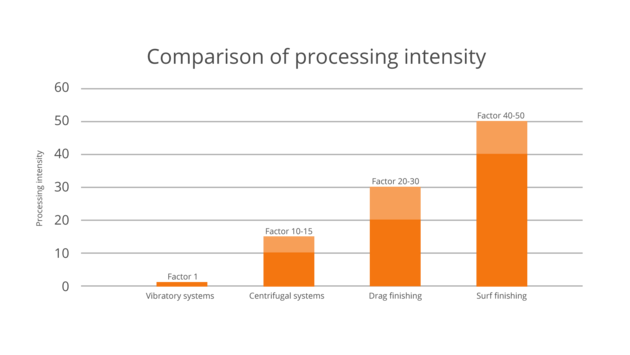
The most popular mass finishing machines for processing large volumes of non-delicate work pieces are rotary vibrators, which are available in different versions and sizes. They allow the finishing of practically all work pieces made from a variety of different materials, provided they are not too big and not fragile. For processing long, relatively bulky work pieces tub vibrators with a rectangular processing bowl are available. Compared to vibratory equipment special mass finishing systems like centrifugal disk finishing machines as well as drag and surf finishers offer a significantly higher processing intensity. They allow the finishing of difficult-to-machine materials in surprisingly short cycle times. For example, surf finishing, optimized by Rösler, is the most intensive mass finishing technology available in the market. Compared to vibratory systems, surf finishing is up to 50 times more intensive. Another benefit of drag and surf finishing is that the work pieces do not touch each other during the entire finishing operation. This is especially advantageous for treating extremely delicate components such as orthopedic implants and jet engine parts.
-
Deburring
Many users employ the mass finishing technology primarily for deburring, i.e., the removal of sharp edges, material overflow in the form of flashes and general edge imperfections produced by previous manufacturing steps. Most of the time, further downstream manufacturing operations are only possible after the work pieces have undergone a mass finishing operation, frequently called âtrowalizingâ. With suitable grinding & polishing media and compounds practically all materials, even work pieces made from plastic, wood and rubber, can be treated. -
Polishing
Polishing is one of the most important applications for mass finishing. The polishing goals can be of a purely esthetic nature, but they can also be functional, for example, the reduction of friction. Polishing is characterized by minimal abrasion, which removes very little material but makes the work piece surface extremely smooth and shiny. Particularly glossy surfaces are achieved by utilizing different media in combination with special polishing agents like pastes in multi-step processes.
-
Surface cleaning
Removal of dirt, oxide layers and other contaminants from the work piece surface. Like other surface treatment operations, cleaning is in many instances an essential pre-condition for safe and effective downstream manufacturing operations. For example, deep-drawn components are covered with oil and grease and must be cleaned, before they can be further processed. Mass finishing is also used for somewhat unusual applications like cleaning cutlery in large-scale gastronomical operations or cleaning and polishing of coin blanks. -
Edge radiusing
Edge radiusing, a particularly intensive type of deburring, is another important application for mass finishing. Sharp edges as well as burs are usually generated in previous manufacturing operations. Radiusing (rounding) such sharp edges produces many positive effects: It helps to reduce the wear of down-stream manufacturing equipment and reduces the risk of injury during assembly operations. Furthermore, it increases the usable life of the respective components. And, if the components are coated, it improves the durability of the coating.
The mass finishing technology is at home in nearly all industries. Among others it is used in:
- The automobile industry for deburring, surface smoothing and polishing of transmission components, piston rings or bearing parts; also for surface refinement of visible items and automotive wheels.
- In the aerospace industry for deburring and smoothing of turbine blades and other high-precision components.
- In medical engineering for polishing orthopedic implants, like hip and knee joints, and surgical instruments.
- In machine building for surface refinement of tools, bearing components and machinery assemblies.
- In the jewelry industry for smoothing and polishing trinkets made from precious metals.
- In electronics for surface treatment of housings and electrical contact areas.